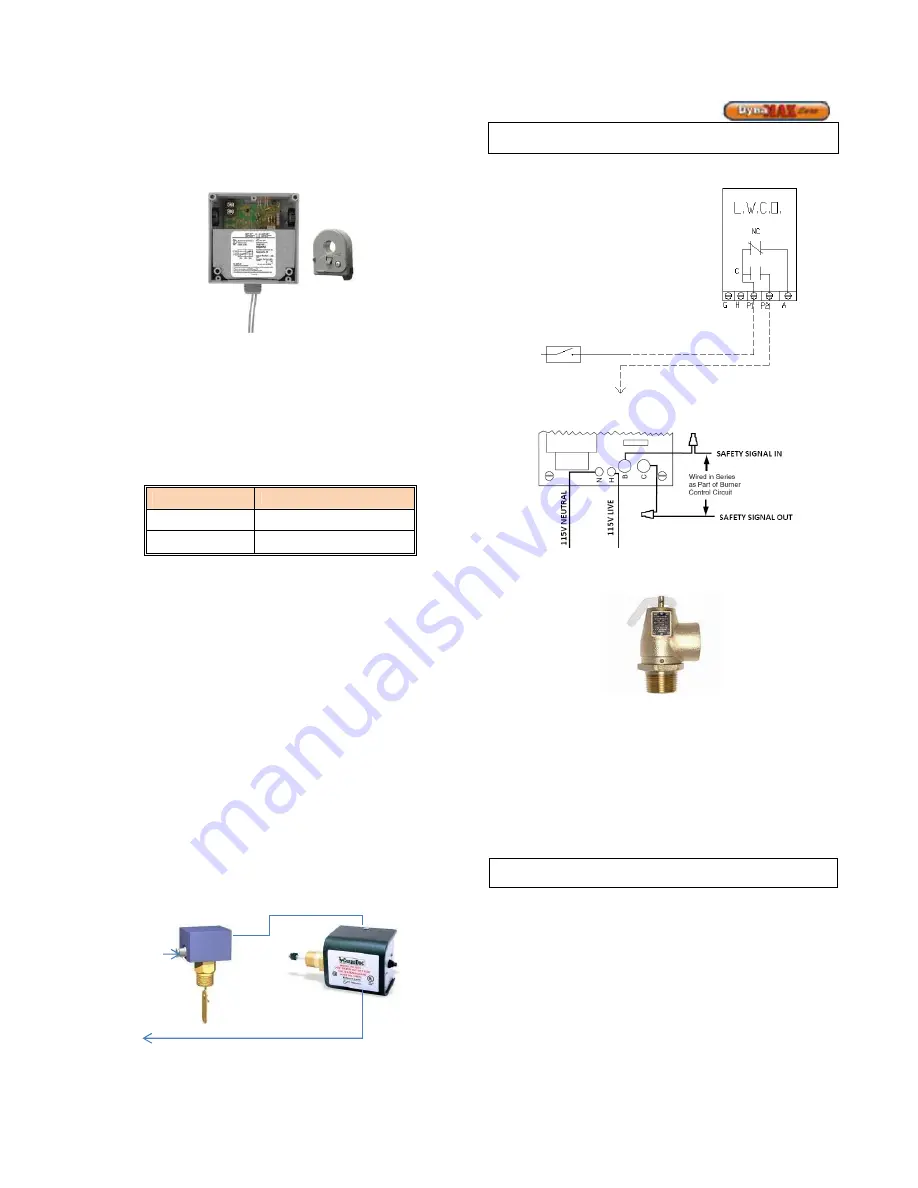
18
4.8
FLOW PROVING DEVICE (wall mount
models and combination models only)
Figure 20: Flow Proving Device
The flow proving device is designed to detect when flow is
present. This is done by detecting the amount of current
(amperes) that exists in the neutral wire from the pump.
When the current becomes too low a ILK error is displayed
indicating a lack of water inside the boiler. The flow proving
device is provided on all DynaMax HS wall mount models
(DM 80 – 250) and combination floor model units (213 –
803). This switch is factory wired.
Table 13: Flow Proving Device Indicator LED’s
LED Illuminated
Symptom
Left
Normal operation
Right
Current under trip point
When testing the operation of the flow proving device always
ensure that 115Vac is being supplied to the pump.
4.9
WATER FLOW SWITCH (Floor mount
hydronic and DHW models only)
A paddle style water flow switch is shipped loose and is to
be installed in the outlet piping on all floor model heating
boilers (DM 211-801) and hot water supply heaters (DM 212
– 802). The flow switch is to be installed in a horizontal run
of pipe in order to provide effective contact. The flow switch
is to be wired into the DynaMax HS terminal board labelled
‘Flow Switch’.
4.10
LOW WATER CUTOFF (If Equipped)
If this boiler is installed above radiation level, a low water
cut-off device must be installed at the time of boiler
installation. Some local codes require the installation of a low
water cut-off on all systems. Electronic low water cut-offs are
available as a factory supplied option on all models. Low
water cut-offs should be tested every six months. The
normally open switch contact of the low water cutoff is to be
wired in series with the flow switch. This can be wired into
the DynaMax HS terminal labelled ‘Flow Switch’.
CAUTION
Remove jumper when connecting to 24 VAC circuit.
Figure 21: Low Water Cut Off Electrical Connections (Watts)
Figure 22: Low Water Cut Off Electrical Connections (ITT)
4.11
RELIEF VALVE
Figure 23: Relief Valve
This appliance is supplied with a relief valve sized in
accordance with ASME Boiler and Pressure Vessel Code,
Section IV (“Heating Boilers”). If this component is shipped
loose, no valve is to be placed between the relief valve, and
the appliance. To prevent water damage, the discharge from
the relief valve shall be piped to a suitable floor drain for
disposal when relief occurs. No reducing couplings or other
restrictions shall be installed in the discharge line. The
discharge line shall allow complete drainage of the valve and
line. Relief valves should be manually operated at least once
a year.
CAUTION
Avoid contact with hot discharge water
4.12
DHW TUNING VALVE (combination models
only)
A DHW tuning valve is provided with all DynaMax HS
combination models. In cases where flow control is not
possible by the end user the DHW tuning valve is designed
to act as a maximum flow controller. The tuning valve is
designed to provide the correct amount of hot water for each
particular DynaMax HS model and application. Refer to
section 10.9 Domestic Hot Water with Plate Heat Exchanger
for further details.
To Terminal #10 on
Terminal Board
Connection detail for placing
L.W.C.O in 24V circuit
WARNING: Be sure to remove the
jumper between H and P1
Water Flow Switch
From
Terminal #9
on Terminal
Bpard
From
Terminal #7
on Terminal
Board
To Terminal #8 on
Terminal Board