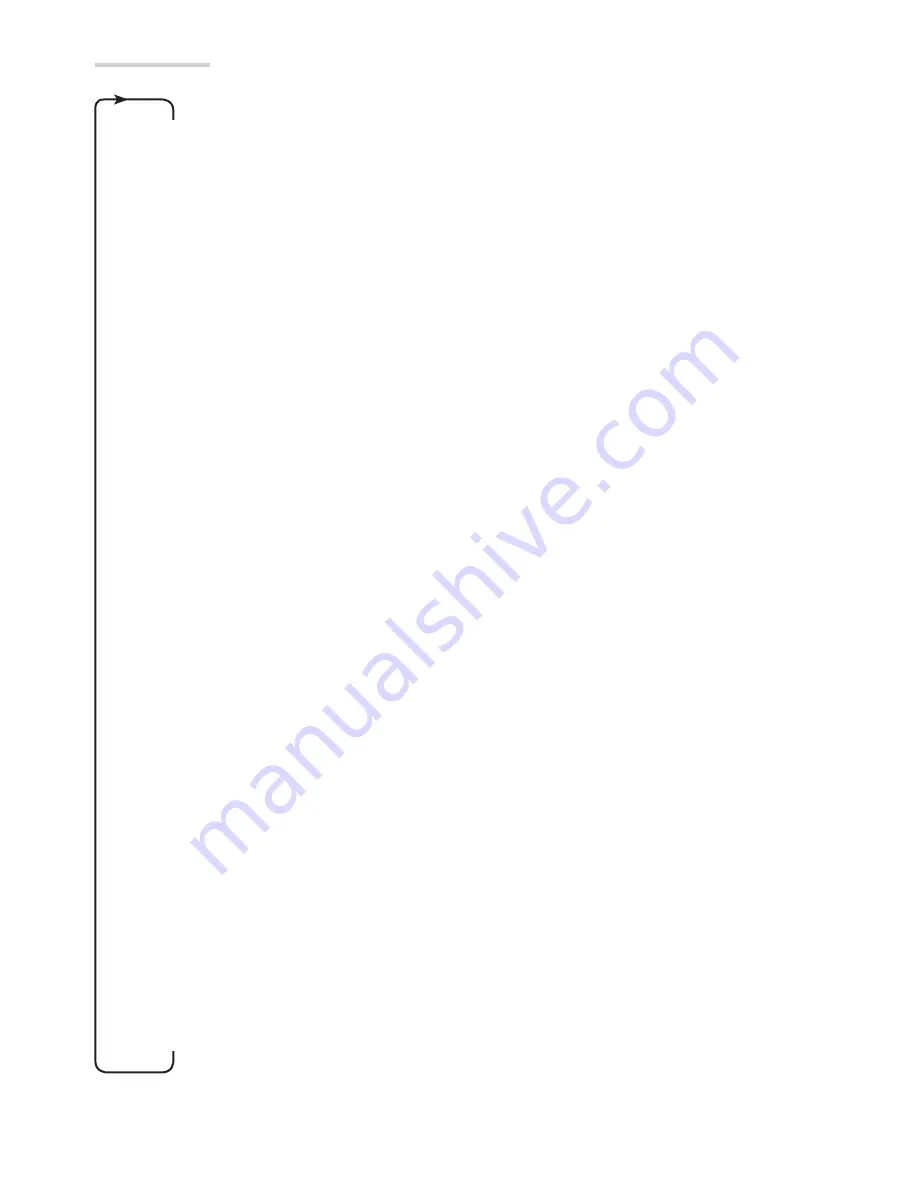
p.
1
8
18
- M
an
u
al
c
od
e
F
A
0
0
0
1
4
-
E
N
F
A
000
1
4
-E
N
v.
33
04/2
0
1
6 - © C
am
e S
.p.
A
. T
h
e c
onte
nt
s o
f th
is
m
an
u
al
m
ay b
e c
h
an
g
ed at a
ny ti
m
e w
ith
ou
t p
ri
or n
oti
ce
.
Functions map
F 1
Total stop function (1-2)
F 2
Function associated to input 2-CX
F 3
Function associated to input 2-CY
F 5
Safety test function
F 6
Maintained action function
F 7
Control mode on 2-7
F 8
Control mode on 2-3P
F 9
Obstruction detection with motor idle function
F 10
Function associated to the gate-open signaling output
F 11
Encoder exclusion
F 12
Slowed-down start function
F 14
Sensor type selection function
F 18
Additional light function
F 19
Automatic closing time
F 20
Automatic closing time after partial opening
F 21
Prefl ashing time
F 28
Adjusting opening speed
F 30
Adjusting opening slow-down speed
F 34
Sensitivity during movement
F 35
Sensitivity during slow-down
F 36
Adjusting partial opening
F 37
Adjusting the gearmotor's opening slow-down starting point
F 38
Adjusting the gearmotor's closing slow-down starting point
F 49
Managing the serial connection
F 50
Saving data in memory roll
F 51
Reading memory roll data
F 52
Transferring parameters from Master to Slave
F 54
Opening direction
F 56
Peripheral number
F 63
Changing COM speed
F 65
Function associated to the RIO-EDGE [T1] input
F 66
Function associated to the RIO-EDGE [T2] input
F 67
Function associated to the RIO-CELL [T1] input
F 68
Function associated to the RIO-CELL [T2] input
F 71
Partial opening time
U 1
Entering new user with an associated command
U 2
Deleting single users
U 3
Deleting all users
A 1
Motor-type setting
A 3
Calibrating travel
A 4
Resetting parameters
A 5
Counting maneuvers
H 1
Software version