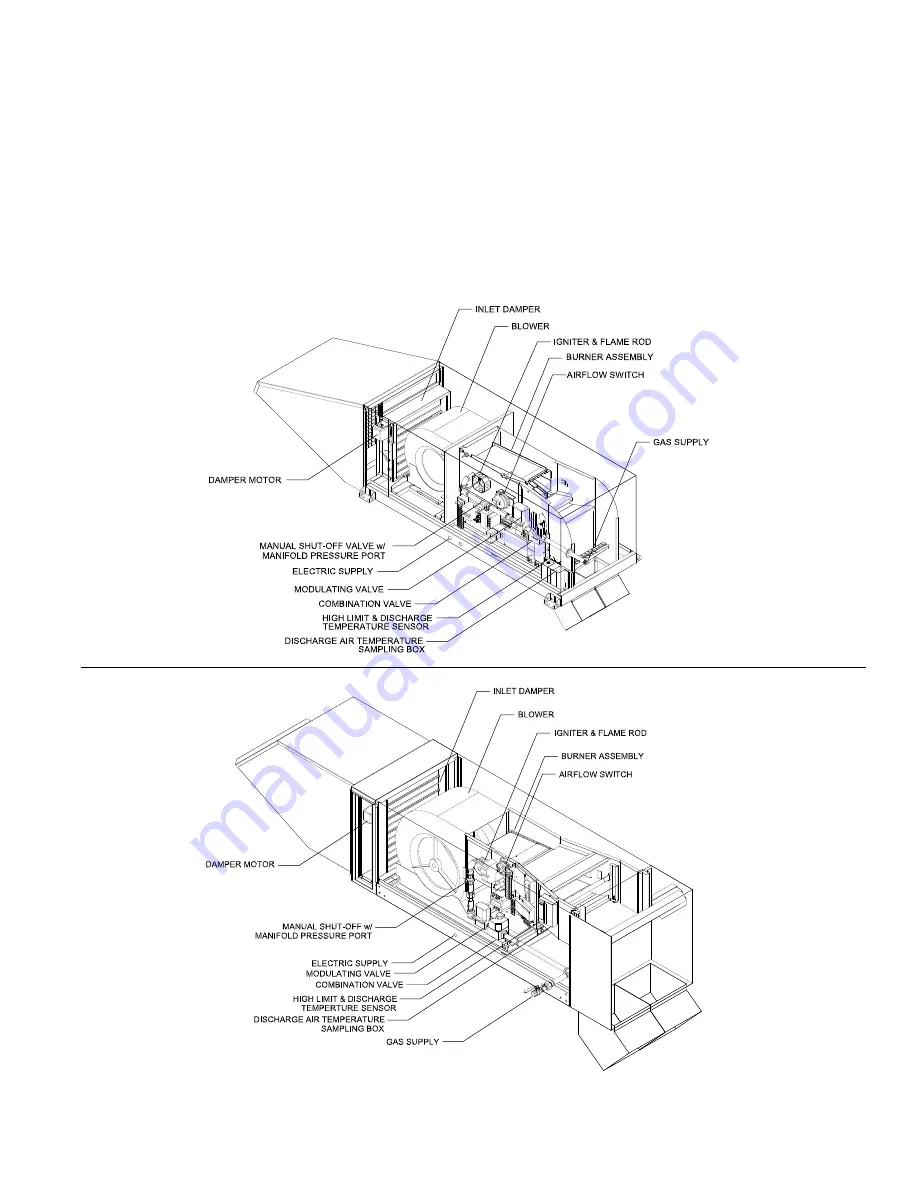
SA-Series Technical Manual
5
Cambridge Air Solutions
HEATER CONFIGURATION
Cambridge SA-Series Blow-Thru
®
heaters are utilized
to meet the space heating requirements of commercial
or industrial buildings. The control system is typically
designed to cycle the heaters on and off in response to
the rise and fall of the space temperature. The heater
will discharge air at the temperature selected (up to
160ºF). The operating thermostat is typically located
near the perimeter of the building in a location which
is out of the direct path of the heated discharge air,
insulated from cold surfaces, and shielded from cold
drafts created by air infiltrating the building.
TYPICAL SYSTEM OVERVIEW
HEATER OPERATION
SA250
SA350