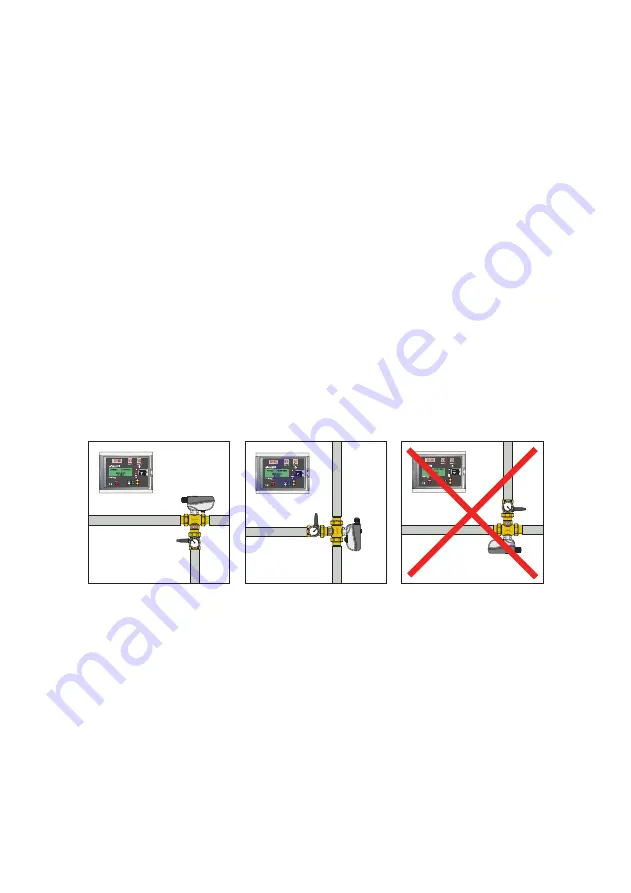
Plumbing installation
Before installing the LEGIOMIX electronic mixing valve, pipes must be flushed to prevent impurities in
the water from affecting performance. Always install strainers of appropriately sized capacity at the inlet
from the water main supply. Caleffi LEGIOMIX electronic mixing valves must be installed as shown be-
low, conforming to applicable codes, and installed either vertically or horizontally, but the actuator must
never be oriented upside down.
System piping
Recirculation connections in hot water system should be located as near as possible to the fixtures they
serve.
Anti-scald mixing valves should be located at all points of use (i.e. sinks) to provide safe water tempera-
ture as specified in local codes or requirements.
All mixing valves should be identified and have their maximum discharge temperature measured and
documented on regular basis.
Where a mixing valve is installed within the hot water supply;
a) Precaution should be taken to prevent the buildup of high temperature water in piping during periods
of low or no use.
b) Check valves should be provided to prevent bypassing of hot and cold water through the mixing
valve.
The mixing valve body indicates with arrows, hot water inlet- red, cold water inlet - blue.
∞
∞
∞
∞
∞
∞
∞
∞
∞
∞
∞
∞
Check valve
In systems with inlet pressure fluctuations, check valves should be installed to prevent backflows, as
is shown in the application diagrams. Check valves, code NA10366 (for 1” and 1¼” LEGIOMIX) and
NA10367 (for 1½” and 2” LEGIOMIX) may be used.
Commissioning
Due to the special purpose for electronic mixing valves, commissioning in accordance with current
regulations and by qualified personnel using suitable instruments is required. Check that the hot and
cold water supply pressures are within operating limits of the mixing valve, see technical specifications.
Check the temperature of the hot water coming from storage, greater than or equal to 140°F (60°C).
Record all parameters settings and measurements taken in the installation log book.
29