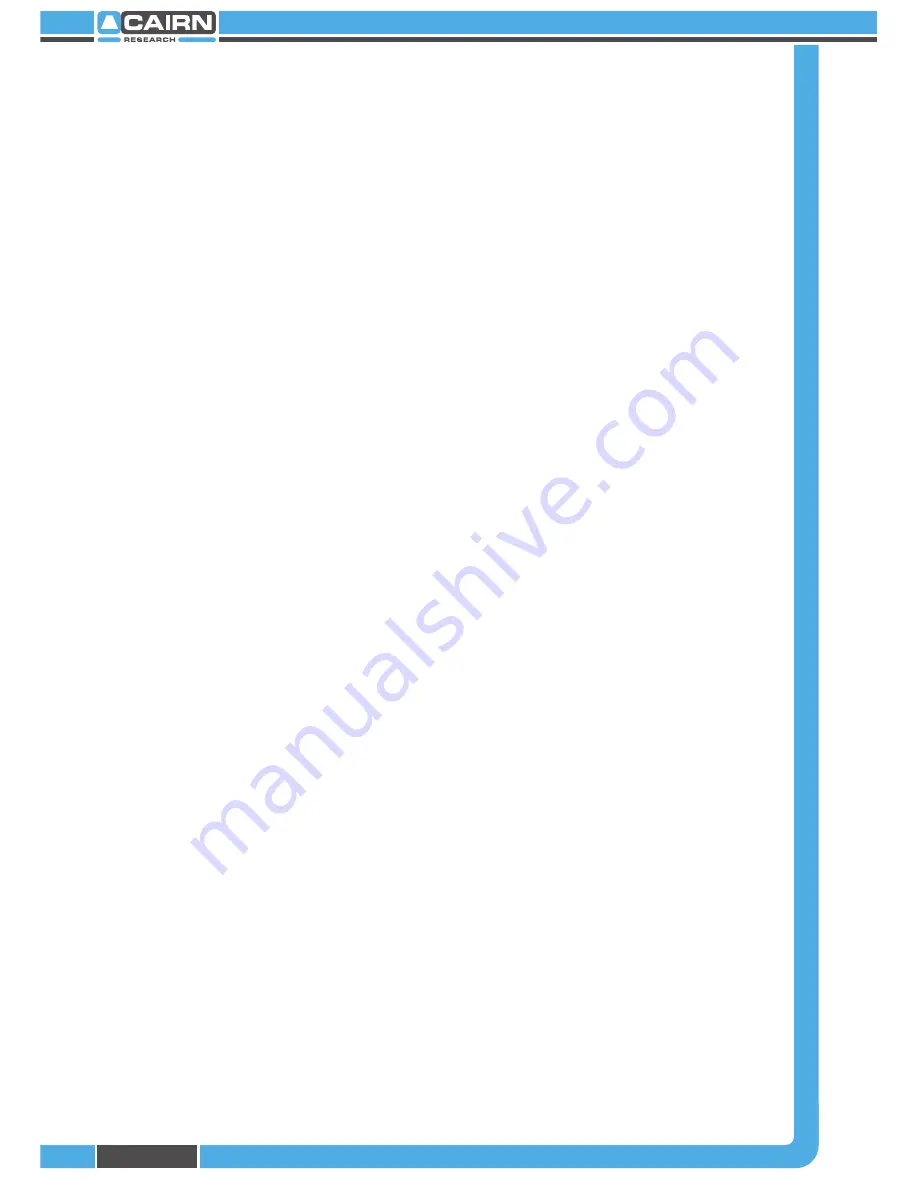
7 Appendix
The information given here is provided to allow users to construct their
own LED heads if they wish to do so. Alternatively - and perhaps more
conveniently - it will allow heads supplied by us to be customised to use
other LEDs if required.
7.1
LED Head Connections
The LED head has an 8-way locking DIN connector. The pin numbering
for these connectors can most politely be described as bizarre, having
evolved from connectors with fewer and more widely spaced pins.
Therefore the pin numbers are just given here for reference, as the
following visual description is likely to be much more helpful. Looking into
the back (cable side) of the plug, oriented with the locator slot at the
bottom, you will see seven pins forming most of a circle, with an eighth
one (which actually is pin 8!) near the centre. The connections are
described in a sequence going clockwise from the pin to the left of the
locator slot, and ending with the near-central one.
Pin 6 Positive connection to the LED.
Pin 1 Negative (ground) connection to the LED.
Pin 4 “Array” signalling connection. If this pin is connected to a positive
voltage source, i.e. the positive supply voltage for the photodiode
amplifier on pin 7, the “array” indicator on the controller will be
illuminated, and the power readings on the meter will be reduced
by a factor of 10, to allow power levels of 20W or more to be
displayed. Otherwise this pin should be left disconnected.
Pin 2 The input connection for the overload protection network. The
resistors and capacitor comprising this network should be
connected between here and ground, i.e. pin 3.
Pin 5 The signal output from the photodiode amplifier.
Pin 3 The ground connection for the protection network and the
photodiode amplifier.
Pin 7 Positive supply (+12 to +24V, depending on the drive voltage
requirements for the LED, which are selected automatically) for
the
photodiode amplifier.
Pin 8 Negative supply (-5V) for the photodiode amplifier. Note that the
controller detects the presence of an LED head by the current
drawn from here by the photodiode amplifier. Therefore if no
amplifier is fitted, a 10Kohm resistor should be connected from
here to ground (pin 3) in order to provide a dummy load.
8W
32.3K
33K
9W
27.6K
27K
10W
24K
22K
12W
19K
18K
15W
14.4K
15K
17W
12.3K
12K
20W
10.1K
10K
25W
7.7K
7K5
30W
6.1K
6K2
40W
4.3K
4K3
50W
3.2K
3K3
100W
1.04K
1K
These resistor values correspond to tenfold higher power levels in array
mode, which is signalled as described in the LED head connections
section of this Appendix. Note that the highest power that can be
metered is 20W (200W for an array, although that power can't be
achieved in practice), but the overload circuitry can in theory measure
power levels of up to 100W.
For many LEDs the maximum drive specification may be given as a
current rather than a power. In such cases the voltage drop across the
LED at its maximum rated current should be measured and then
multiplied by the current to determine the equivalent power level. This
voltage is likely to be in the 3-4V range for green and blue LEDs, possibly
rather more for UV devices and rather less for red ones. The
permissible transient power levels may well not be quoted, so may need
to be determined by trial and error if you want to exploit this possibility.
Transient levels of 2-4 times the steady-state level, with a decay time
constant of around 10-20msec or possibly a little longer, will probably be
about as far as we can go.
For setting a higher transient power overload level, another resistor Rp,
in series with a capacitor C is connected in parallel with the resistance R
calculated as above. The steady-state overload level will be the same as
before, and the transient level will be given by the value of the two
resistances in parallel. The procedure is to choose the effective parallel
resistance value, Reff, of R and Rp to give the required transient level, and
then to calculate Rp from the relation Rp = 1/(1/Reff - 1/R).
The time constant with which the overload power level declines from its
transient to its steady-state value is set by the capacitance C that is in
series with the parallel resistor, in conjunction with an equivalent
resistance Re, to give a time constant of ReC. The procedure for
7.2
Overload Protection
The overload protection is programmed by an RC network in the plug for
the LED head. This network forms part of a voltage divider from the
measured power signal. Normally the power signal is 100mV/W,
except when an LED array is used (detected by another connection in the
LED head plug), in which case the signal is 10mV/W to allow higher
powers to be controlled.
In both cases the power signal is connected to one of two comparator
inputs (the signal input) in the OptoLED via a 100K resistor. This
comparator input also connects to the RC network in the plug via a 1K
series resistor (the resistor slightly complicates the RC network
calculations but is there to protect the comparator input), and the other
end of the RC network is connected to ground. The other comparator
input (the reference input) is connected to a 200mV internal reference
input.
Overload is triggered as soon as the signal input at the comparator
exceeds the reference input; this cuts the power for about 1 second. If
the protection “network” is just a single resistor, overload will be
triggered as soon as the power exceeds the value set by this resistor. In
practice, however, LEDs can be transiently overdriven, and this can be
permitted by connecting a second resistor in partallel with the first, but
with a capacitor in series with the second resistor. The peak (transient)
power is set by the parallel value of the two resistors, and this declines to
the steady-state value set by the first resistor, with a time constant that
depends on the resistor and capacitor values.
The resistance value R in Kohms to set a given steady-state power level P
in watts is given by
R = 20/(0.1P-0.2) - 1
Solving for P rather than for R we obtain
P = 2 + (200/R+1)
These relations give a minimum power of 2W (or 20W for an array)
when R is infinite. Calculated values and nearest preferred resistor values
for higher powers are as follows:
Power
Calculated
Preferred
3W
199K
200K
4W
99K
100K
5W
65.7K
68K
6W
49K
47K
7W
39K
39K
calculating C for a given time constant T is as follows. First calculate Re,
which is given by R+1K in parallel with 100K, in series with Rp, i.e. Re =
1/{1/(R+1K) + 1/100K} + Rp. Then calculate the required value of C
from C = T/Re.
These components are connected between pins 2 (signal) and 3 (ground)
of the connector plug. The orientation is unimportant, but by convention it
makes more sense to have the capacitor on the ground side.
A practical example may be helpful in order to give some idea of the
typical size of C. Let us assume we want a transient power level of 10W,
declining to a steady-state level of 5W with a 10msec time constant.
From the table we select 68K for R to get 5W steady-state power, and
then select Rp to give a resistance of 24K (for R and Rp in parallel) to get
10W transient power. This requires Rp to be 37K, for which the nearest
preferred value of 39K will be close enough. We now calculate Re as
above to get a value of 79.8K, giving a required value of C of about 125nF,
for which either 120nF, or 100nF in parallel with 22nF, would be close
enough.
Page 16