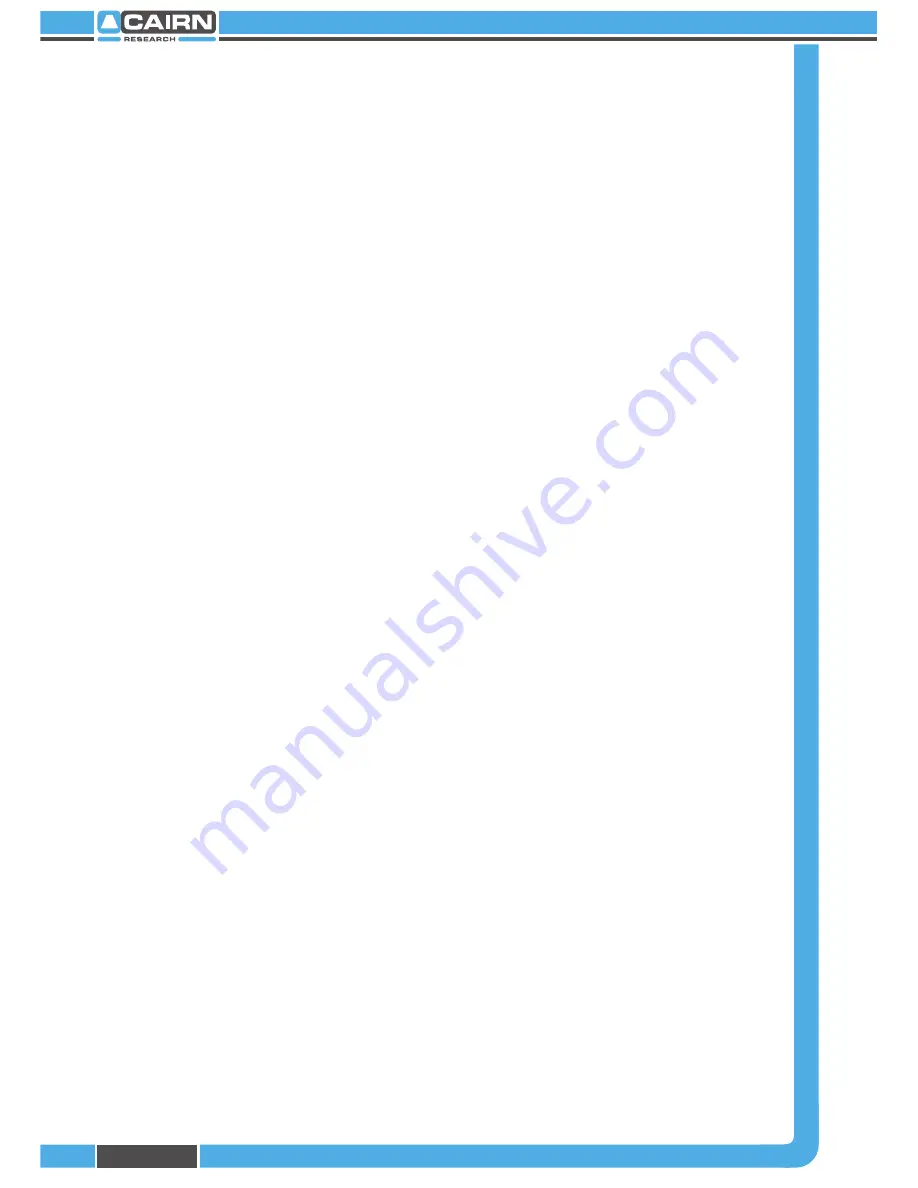
3
Technical summary
Internal jumper links and Presets
The controller contains two identical circuit boards, one for each LED.
The circuit board nearer the front panel corresponds to the right-hand
set of LED controls, and the function of each of the presets and jumper
links is as follows.
J1 and J2
These are labelled “Hold1 Pol” and “Hold2 Pol” respectively. These
control the polarity of potentially two gating inputs, although only one of
these (Hold2) is currently used. J1, the jumper for the unused input,
must be left in the left-hand (H) position. The controller is supplied with J2
in the right-hand (L) position, which means that a logic low level on the
gate input will switch the LED off. This input is low by default if it isn't
connected to any signal source. If J2 is moved to the left-hand (H)
position, a logic high level on the gate input will now be required to switch
the LED off.
J3
This jumper is actually brought out as a front panel switch, for controlling
the pulsed mode of operation.
J4 and J5
These two jumpers set the current range, which is normally set to 5A by
default. The other ranges are 1A (both jumpers disconnected), 2A and
10A. Of these, 2A is likely to be the most useful alternative. The 10A
range is not officially specified, since amongst other reasons the power
supply cannot provide sufficient current (except maybe for transients).
We included it in case LEDs that required such high currents became
available, but in practice it seems that manufacturers prefer to make
more “powerful” LEDs by connecting two or more chips in series, so it's
the voltage rather than the current that needs to go up. Note that if you
change the current range, then for correct operation of the optical
feedback, you will also need to adjust the preset in the LED head for that
channel, to give 10V fullscale for the new current range at the monitor
output (in practice we recommend that you do this for a current that's
about 10-20% of the fullscale value and set the output accordingly).
J6
This jumper provides the connection between the digital control
electronics and the parallel shunt pathway that diverts the current
around the LED, and it should normally be left in the INT position. It is
provided to cater for possible applications in which users may wish to
control the shunt pathway directly, in which case the jumper link should be
removed and the logic-level control signal applied to the central pin.
PRE1
This zeroes out any voltage offset in the optical feedback pathway within
the controller. The procedure is to disconnect the LED head, and adjust
for zero output on pin 7 (second pin from upper left) of IC2. This IC is the
second one down from the top, near the left-hand edge of the board. Use
one of the BNC sockets as the ground reference for this and other
adjustments when required.
PRE2
This calibrates the pulse length (not frequency - see PRE4 for that) for the
pulsed mode of operation. The point to observe the pulses corresponds
to the right-hand pin of J3. This is connected to one of the contacts on the
continuous/pulsed switch on the front panel, which is most easily
identified by tracing the wiring to it, and where it is most conveniently
measured. To ensure correct adjustment, it is recommended that the
preset is first set fully clockwise, with the pulsewidth control on the front
panel set to maximum. It should then be advanced anticlockwise until the
pulse is high nearly all the time; if advanced too far it will suddenly change
to a square wave. Note that this preset will be need to be readjusted to
achieve this condition if PRE4 is adjusted to change the pulse frequency.
PRE3
This sets the 10V internal reference voltage. The most convenient
measurement point is the clockwise end (front tag) of the current control
potentiometer.
PRE4
This sets the frequency of the internal oscillator that is used for the pulsed
mode of operation. It is most conveniently measured at pin 3 of IC10.
This is the second IC down from the top right-hand side of the board, and
pin 3 is the second pin from the right at the bottom. The nominal
frequency range is 20-100KHz, and we normally recommend using the
lower part of this range, say 25-30KHz, although higher frequencies
should also be ok. Note that if this preset has changed, then PRE2 will
also need to be readjusted as described above.
PRE5
This zeroes the offset in the current-driving circuitry for the LED. With the
LED “on”, as judged by the indicator light, the current control should be set
to its minimum value. PRE5 should then be adjusted to just extinguish any
light emission from the LED.
'ROTARY DIN' Socket
This is an 8-pin locking DIN socket for connection to the LED head. In case
you would like to make up your own custom LED heads, the connections
are described in the Appendix.
'GATE 1' and 'GATE 2' BNC's
The OptoLED has two "GATE" inputs so that it can be simultaneously
driven by two separate devices. These BNC inputs can be configured
internally for a range of different logic states, but the default is for the
OptoLED to require both inputs to be TTL logic high for the LED to switch
on when the front panel "GATE" switch is selected. The standard
configuration is to connect one BNC to the software controller and the
second to the "Integrate" or "Read" output of a scientific camera. In
fluorescence microscopy, the LED will then only be switched on for those
periods when it has been instructed to by the software AND the camera
is actually integrating photons. This can significantly reduce phototoxicity
and motion artefacts, as the preparation is only exposed to light during
the camera exposure and not during the read-out or any dead time. An
alternative use of this dual gating is to allow an interlock where one of the
inputs has to be actively driven high before the other input can be used.
A BNC link cable is included with the OptoLED in case only one control
input is available.
'MONITOR' BNC
This is an output signal from a photodiode and its associated amplifier in
the LED head. The gain of this amplifier is set by a preset resistor in the
LED head, and is normally configured so that a full range LED drive current
gives an output signal of +10V. To a first approximation, the light output
from an LED is proportional to the drive current, but temperature and
other effects can and do change this proportionality somewhat.
Conversely, the photodiode detection system is both linear and very
stable, so it can be used as an accurate record of the actual behaviour of
the LED.
PRESETS
These presets can be adjusted to ensure that when using the remote
control,
different wavelengths of LED's can be used at their maximum intensity.
To increase intensity turn the presets clockwise, to decrease turn
anti-clockwise.
(Note: if the Overload indicator on front panel is flashing, turn
anti-clockwise, if it is not turn clockwise until it begins to flash, and then
turn it back slightly)
'REMOTE/FRONT PANEL' Switch
This switch determines whether the unit is controlled by the optional
remote slider or the front panel controls. The remote control slider plugs
into the rear on the power supply, as described later.
'LED ON' Indicator
This indicator is illuminated whenever the digital control signals (both
from the “GATE” input and the internal pulse generator) put that channel
into the “ON” state. Under these circumstances the corresponding LED
should also be on, as long as a non-zero current has been set on the level
control, or a non-zero external control voltage has been applied via its
rear panel BNC input socket. Since its status is affected by the digital
control signals, this indicator appear to be illuminated more or less
brightly when those signals are changing too rapidly to be followed by eye.
'OVERLOAD' Indicator
If either the steady or the transient power through the LED exceed values
preset by components within the LED head, this indicator will illuminate
for about 1 sec, during which time the drive current will be switched off to
protect the LED. Resetting is automatic, but the overload condition will
keep re-triggering for as long as the power remains above these values.
For users who, at their own risk of course(!), wish to experiment with the
overload parameters, and/or wish to make their own custom LED heads
(See Appendix).
'
CURRENT' Controller
This is a 10-turn calibrated control which sets the LED drive current
when the ext/level switch on the rear panel is in the “OFF” position
(otherwise control is via an external voltage). The full-scale current is
normally 5A, but can be changed to 2A or 1A by changing the positions
of internal jumper links.
'POWER – CURRENT' Meter and Switch
This allows the meter to display either the current in amps or the power
in watts for each LED. The OptoLED's electronics set the current through
the LED, so the power is the set current multiplied by the actual voltage
drop across the LED (or LEDs in the case of multiple devices in series),
which is typically a few volts for a single LED. In both cases, the displayed
values are the average ones, so for example a 2A current which is gated
on for 25% of the time will give a reading of 0.5A.
'METER'
This is a liquid crystal display, with a maximum reading of 19.99. The units
are amps or watts, according to the setting of the current/power switch.
Selection of this condition is made automatically by the LED head, as
described above and in the Appendix.
2
Installation Guide
Depending on the required configuration the LED heads may have been
preinstalled in a combiner box or microscope coupling, or they may be
separately. Either way we would recommend connecting two LEDs to the
controller box using the DIN plugs provided and pointing the LEDs (or
output of coupling) at a piece of white paper, NEVER VIEW THE LEDS
DIRECTLY. Next connect the power supply to the mains, and read the
following description of the controls before verifying operation.
Note: - the main unit houses two fully independent controllers, each
applying to the appropriate DIN on the rear of the unit.
2.1
Front Panel
OFF/ GATE/ON' Switch
This switch allows the digital control signals to be overridden. These
signals are applied via the "GATE" input on the rear panel, but in the "OFF"
position the LED is always off, and in the "ON" position the LED is on, so
long as a non-zero internal or external drive level has been set. The
"GATE" position gives normal control of the LED by the gate input.
When looking at the front panel, the left hand preset controls the left
hand bank.
'AUX' Connector
This is not currently being used, but has been included to future-proof the
controller for further development.
'REMOTE' Connector
This connector is for the (optional) remote control slider. Please note, in
order to control the unit using the remote control, the switch must be in
the 'REMOTE' position on the front panel of the unit.
2.2
Rear Panel
'EXT LEVEL' BNC and Switch
This is an external analogue input for the LED drive level, active when the
adjacent switch is in the “ON” position. The input range is 0 to +10V, and
is always the same as for the current control on the front panel, i.e. 1, 2
or 5A full scale according to the setting of internal jumper links.
'FEEDBACK' Switch
In normal operation, the current through the LED is set by using a
feedback loop which compares it with a control voltage. This voltage is
either derived from an internal reference via the front panel current
control, or provided externally via the 'ext level' BNC input. When the
feedback switch is in the “ON” position, the feedback loop uses the output
of the photodiode amplifier instead, so the control voltage now sets the
optical output of the LED rather than the current through it. Use of this
facility is strongly encouraged for critical applications. The only downside
is that the optical response time for switching purposes is now rather
longer, although at around 10 micro- seconds it's still fast enough for
most applications. However, this is still too slow to allow proper operation
of the variable mark:space ratio pulsing facility, so that is automatically
disabled when optical feedback is selected.
4
General Operating Notes
LED technology is continuing to develop rapidly. The first LEDs operated
only in the red or infra-red, and were not particularly powerful. However,
they are now available not only across the optical spectrum, but even
extend into the near ultraviolet. Intensities have also increased by literally
orders of magnitude, now rivalling incandescent lamps, and even
beginning to compete with some arc lamps. The continual intensity
improvements have caused some manufacturers to run short of
superlatives for their newer devices, which therefore have to be called
"superhyperultrabright" or some similar nonsense.
Of course, the major incentive for the development of brighter devices
has been their potential use as illumination sources, rather than just as
indicators. The Luxeon "Lumiled" and similar devices are a good example
of the current state of the art here, which at the time of writing (late
2005) is continuing to improve at an impressive pace. Our LED power
supply has been designed very much with these particular devices in
mind, but at the same time we have endeavoured to make it suitable for
a wide range of alternatives, as well as attempting to anticipate future
further improvements in this technology.
The general characteristics of LEDs are as follows. Since they are a type
of diode, they have the basic characteristics of such devices, i.e. they only
pass current in one direction, and the current rises very rapidly once the
voltage in that direction exceeds a certain threshold. Ordinary silicon
diodes have a threshold voltage of about 0.65V, but LEDs have
significantly higher thresholds, e.g. around 1.2V for a standard red
indicator LED. Devices designed for shorter wavelengths tend to have
higher thresholds, of maybe around 2V or so, and in spite of the fairly
steep diode characteristic they may drop as much as 3 or 4V when
driven at full power. These figures are all for a single LED; please note
that some "LEDs" may actually consist of several devices in series, in
which case their operating voltages will be correspond -ingly higher. In all
cases the light output from an LED is approximately proportional to the
current, so this is the parameter that one needs to control for optical as
well as electrical reasons.
In order to drive an LED safely and reliably, a current source rather than
a voltage source is required. For low-power operation a voltage source
can be converted into a reasonable approximation of a current source by
applying a voltage significantly in excess of the device's threshold voltage
in series with an appropriate resistance. This is fine for indicator LEDs,
where the current is low and unlikely to be varied, but is far less suited for
power applications. In this case the only way to vary the power with
reasonable efficiency is to vary the series resistance, and this really isn't
feasible to do directly. Instead, a constant-current power supply with a
variable current output is far more suitable, so this is what we are using
here.
However, just as a constant-voltage power supply has a maximum output
current, so does a constant-current power supply have a maximum
output voltage, and for general cost and efficiency reasons it is important
to match the current or voltage limits to match what is reasonably to be
expected. The OptoLED controller therefore normally has a maximum
output voltage of about 10V. We chose this value because it can drive
two Lumiled or similar devices in series, while not being too much of an
overkill for a single device. However, LED modules containing multiple
elements may require a higher output voltage. Under these
circumstances the controller automatically switches to higher voltage
ranges, allowing the maximum to be raised to up to about 20V.
As to current ranges, indicator LEDs typically have maximum current
ratings of a few tens of mill amps at most, whereas those used for
illumination may require up to several amps. The standard drive current
range for our supply is 0-5A, but it can be reconfigured internally to either
0-1A or 0-2A if preferred. To allow future flexibility or customisation, the
internal electronics is potentially capable of handling currents of up to
10A.
Although LEDs may become somewhat less efficient at higher currents,
their maximum output is ultimately limited not by optical saturation but by
thermal dissipation. Therefore, it is perfectly permissible for an LED to be
driven transiently at a higher current than the safe steady-state limit. The
extent to which this can be done, i.e. how much higher a current can be
applied for how long, will depend on the characteristics of that particular
type of LED, but information about this may be available in the device's
data sheet. Otherwise, as a rough guide, we're talking about times of up
to perhaps a few tens of milliseconds. In any case, since most LEDs are
relatively cheap, and they can be destroyed without damaging the power
supply, then trial and error may well be a perfectly acceptable way of
exploring their safe operating limits.
One obvious situation which permits transient over driving is when one is
repeatedly switching between two or more LEDs of different wavelengths.
Their outputs can be combined by one or more dichroic mirrors, so the
sample is illuminated all the time, but each LED can be over driven in
proportion to how many are in use - so long as the "on" time for each LED
is reasonably short in relation to its thermal time constant. However,
there is a potential problem here, to which the OptoLED also provides an
effective solution.
The problem is that the optical efficiency of an LED tends to fall with
increasing temperature, and with some types this effect can be quite
significant, e.g. 10% or more. Unless the pulse duty cycle is quite short
in comparison with the thermal time constant of the LED, the increase in
temperature during the pulse can be enough to cause a noticeable droop
in the light output. The solution here is to provide optical feedback, which
uses a photodiode to monitor the optical output, and the LED is driven
correspondingly harder as its efficiency goes down, in order to maintain
the same level of illumination. Another advantage of this approach is that
since the response of a photodiode to light is significantly more linear
than the light output of an LED is to the drive current, the LED output is
now precisely proportional to the drive signal instead of merely
approximately so. This can of course be very useful in some applications,
and we've been using this technique for years to ensure a linear
current-passing characteristic in our "Optopatch" patch clamp amplifier.
On the other hand, one may not want to use optical feedback all the time.
Any feedback system has an associated response time, so the LED
switching times will not be quite so fast when optical feedback is in use.
Actually though, the gating facility will switch off the LED just as quickly as
for the non-feedback case. The switch on at the end of the pulse will be
somewhat affected, but even here the effect is only partial.
Although the feedback photodiode can in principle be positioned
anywhere in the optical pathway, the most convenient location is likely to
be next to the LED itself. The actual LED chip tends to radiate over a wide
angular range, and although the light may be focussed over a somewhat
narrower range by a built-in lens, generally enough light still escapes at
more extreme angles for an appropriately placed photodiode to pick up
enough to provide the optical feedback, without obstructing the primary
light path from the LED. We have no evidence that the angular
characteristics of the LED light emission change with the operating
conditions, so an "out-of-the-way" location for the photodiode is likely to be
just as effective as one that is somehow positioned within the primary
light path.
For the record, the spectral characteristics of an LED may change
somewhat with the drive current (perhaps at least partly an indirect
result of a temperature-dependent effect), and optical feedback cannot
correct for that effect. However, if the LED is being used with a
narrowband filter, then the effect of any spectral shift will be reduced if
the light monitored by the photodiode has first passed through the same
or a similar filter, so such considerations may influence the positioning of
the photodiode in this case. At the time of writing this manual (June
2010), we are just about to introduce this as an option for those LED
types which may benefit from it.
To the extent that the spectral characteristics of an LED change just with
the drive current (and not with temperature), then this effect can be
avoided by using the variable pulsewidth facility. Here the instantaneous
LED current is either a constant value (set by the current control as
before) or zero, and one now varies the average LED intensity by varying
the mark:space ratio of the pulse waveform. To be effective, the pulsing
frequency needs to be high in comparison with the time-scales that are
of experimental interest, and the 20-100KHz range over which our
system can operate is likely to meet this criterion in practice. However,
this facility is unfortunately not compatible with optical feedback.
Especially at low mark:space ratios, the pulse waveform contains
significant high harmonic frequencies, which the optical feedback system
could not follow with sufficient accuracy.
Finally, a few notes about the most suitable types of LED. For general
illumination purposes, the more powerful types are clearly to be
preferred. However, for microscope illumination the situation is rather
different, and in practice better results may be achieved from using a
less powerful LED here. The reason for this is as follows. A
high-magnification microscope needs to use the condenser (or objective
in the case of epi-illumination) to focus the light onto a very small area.
This requires the light going into the condenser or objective to be nearly
parallel, which is only the case if it has come from (or behaves as if it has
come from) a very compact source. Unless the output per unit source
area is also higher, any increase in source size above about 1mm is
unlikely to give brighter illumination, although it will make set-up less
critical. The chip size and configuration in the device is easily observable,
and a common configuration for the multi chip devices is to have four
emitters in a square array. For more general illumination, LED arrays
with many more devices are also available. The OptoLED can drive any of
these as long as their required voltage and current requirements are
within the specifications given over leaf.
Page 10