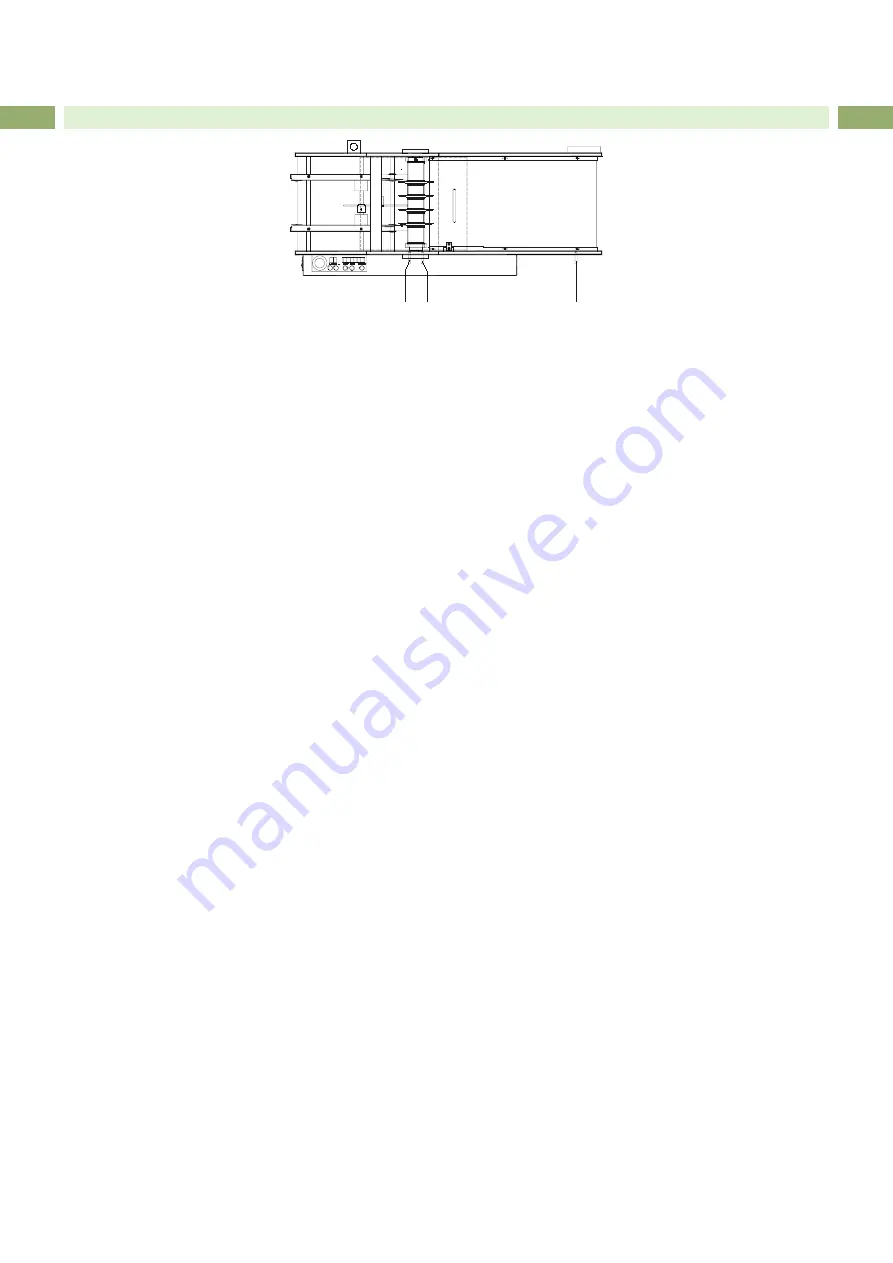
26
26
Figure 28 Maintenance
The following steps are to be performed regularly to maintain the MAESTRO 5L PCB separator:
Before each shift :
Check the laser beam of the sensors (1), (2) and (3).
Clean the leaving hole of the laser beam if necessary.
After each shift :
Remove dust and PCB scrap from the MAESTRO 5L.
Use a vacuum for this procedure if possible.
Check blade wear.
Check the alignment of upper and lower blades. The difference between the blades should be less than 0.1mm.
Weekly :
- Check all screws for tightness.
It is necessary to be sure all screws are secure to maintain the quality of separation.
Every 2 month :
Clean all gears in the gearbox and lubricate as necessary.
To perform this operation, the front cover must be removed (see section 12.2).
Check the supply belt wear.
11
Maintenance
1 2
3