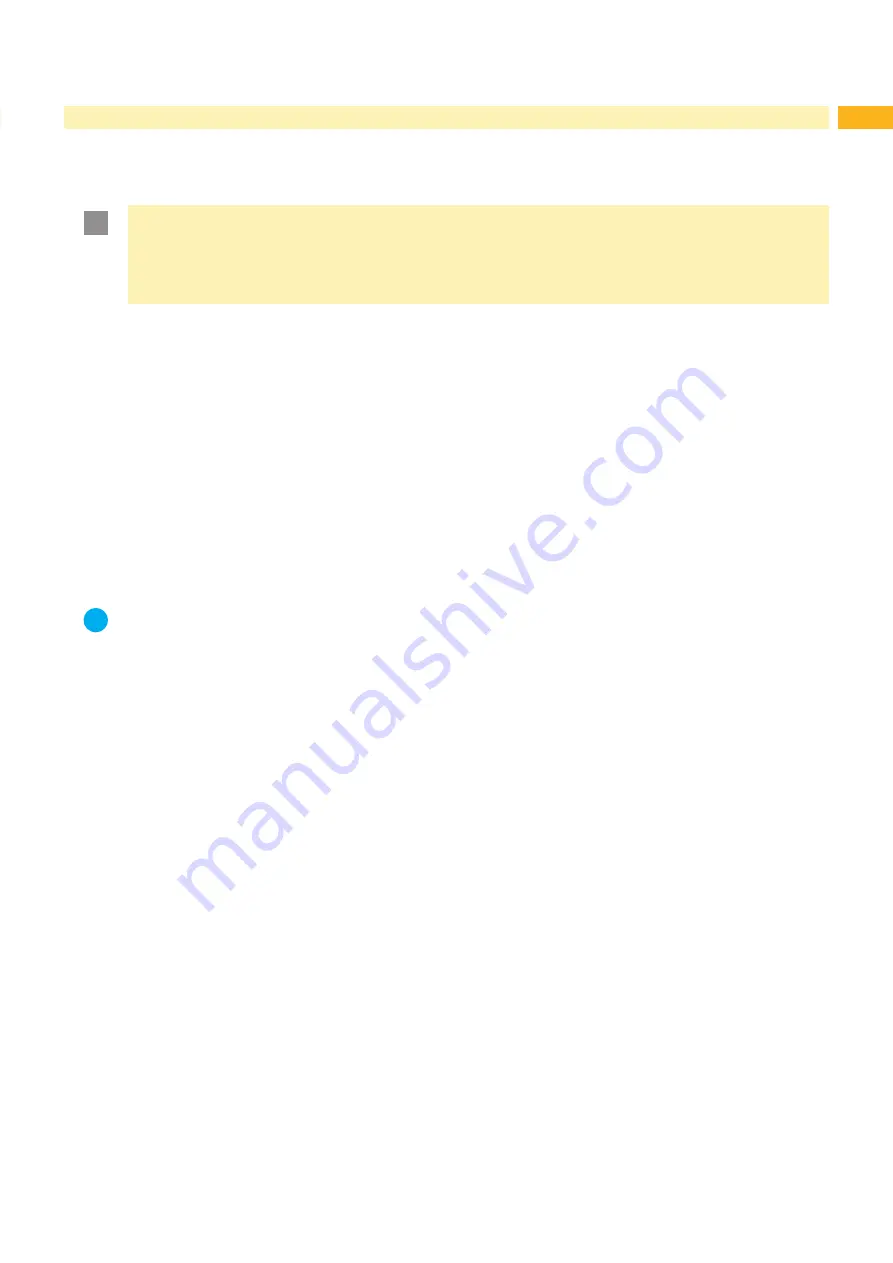
18
19
8.3
Setting the Peel Position
To optimize the transfer of the labels from the printer to the applicator there two different parameters are available for
adjusting the peel position.
!
Attention!
First adjust the parameter "Peel Position" in the printer configuration.
Following adjust the additional peel-off offset in the software.
It is very important to follow that procedure for a certain start after label loading and for the re-start after
error treatment.
Parameter "Peel Position" in the printer configuration
Check the basic setting in the printer setup. Perform labelling cycles by alternately pressing the
feed
key and the
„9.1 Test Mode without Print Job“.
Adjust the "Peel Position" in such a way, that the blank labels are peeled-off completely from the liner
Peel-off offset in the software
Check the setting in the software. Perform labelling cycles by repeatedly pressing the the pre-dispense key
„9.2 Test Mode with Print Job“
Adjust the peel-off offset in such a way, that the printed labels are peeled-off completely from the liner
Programming manual or software documentation.
8.4
Activation of Peel-off Mode
i
Notice!
For labelling operation activate the peel-off mode in the software.
For direct programming use the P command
Programming manual.