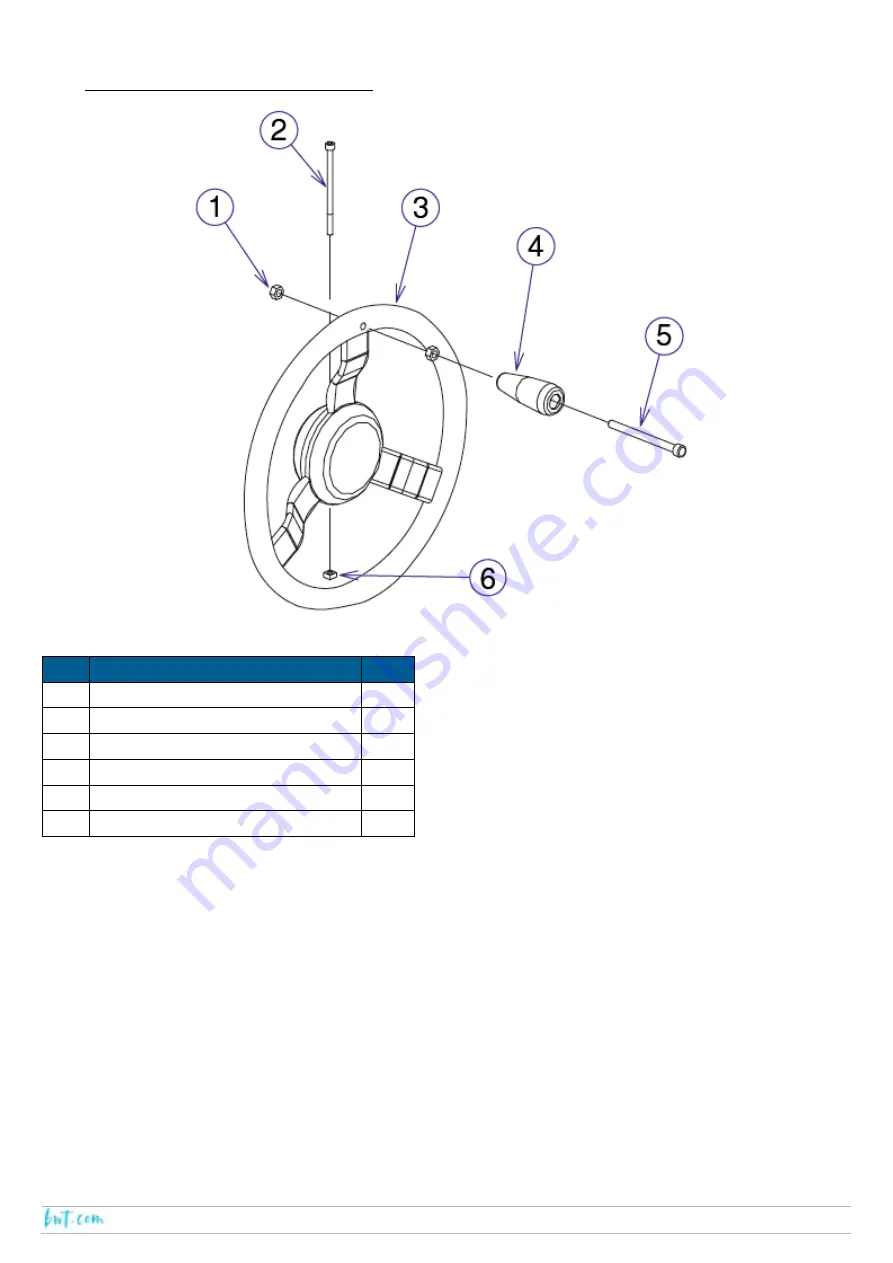
PROTECTION & SAFETY
21
2021/07 - Version: C - Code : 34681
10.
Assembly of the flywheel
The flywheel is supplied to allow the pool to be secured in the event that the motor is out of order.
Ref
Description
Qty
1
Stainless steel nut M8
2
2
Stainless steel screw 6x100
1
3
Flywheel Ø 300mm
1
4
Hand grip
1
5
Stainless steel screw 8x100
1
6
Stainless steel square nut M6
1