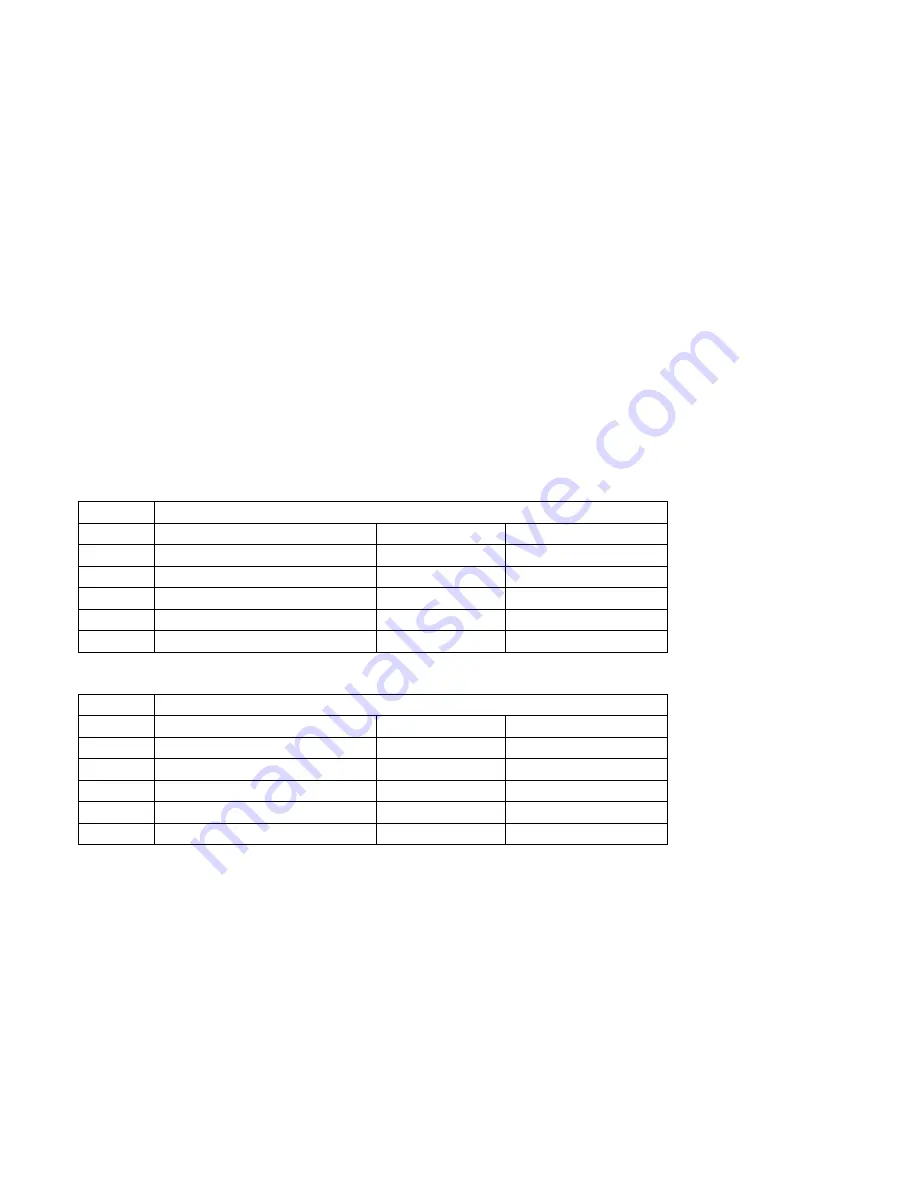
EN D 031 Rev D
Page 9 of 17
Only cracks may develop and as such need to be reviewed. All other indication types have been
addressed by the manufacturer during production. As such, the spider has left the factory with
indication (if at all) which were deemed acceptable. All cracks which have developed in service
are relevant and need to be examined.
Evaluation of indications:
Relevant indications: Only those indications with major dimensions greater than 1/16 Inch
(1.6mm) and associated with a surface rupture shall be considered relevant. Relevant indications
are indications that results from, discontinuities within the test part. Non relevant indications are
indications that results from excessive magnetizing current, structural design or permeability
variances within the test parts. Any indication believed to be non-relevant shall be regarded as
relevant and shall be re-examined to determine whether an actual defect exists. Linear
indications shall be considered as those having a length of more than three times the width.
Rounded indications shall be considered as those having a length less than three times the width.
A lined indication shall be considered as a group of three more indications which touch an
imaginary straight line connecting any two of the group.
For equipment certified in accordance with API 8A & 8C PSL 1:
Maximum Allowable Degree
Type Discontinuity Descriptions Critical Areas Non-critical Areas
I
Hot tears, cracks
None
Degree 1
II
Shrinkage
Degree 2
Degree 2
III
Inclusions
Degree 2
Degree 2
IV
Internal chills, chaplets
Degree 1
Degree 1
V
Porosity
Degree 1
Degree 2
For equipment certified in accordance with API 8A & 8C PSL 2:
Maximum Allowable Degree
Type Discontinuity Descriptions Critical Areas Non-critical Areas
I
Hot tears, cracks
None
None
II
Shrinkage
None
Degree 1
III
Inclusions
Degree 1
Degree 2
IV
Internal chills, chaplets
None
Degree 1
V
Porosity
Degree 1
Degree 2
Note: Only BVM authorized repair facilities are allowed to repair spiders with indications
outside the acceptance criteria.
Lubricator Maintenance
Note: Have spill kit nearby in case of spill while performing this maintenance operation.
1.
Close shutoff valve.
2.
Remove self-venting fill plug.
3.
Fill reservoir to within ¼” (6 mm) of top of bowl with industrial type ISO air tool
lubricant (Page 7).