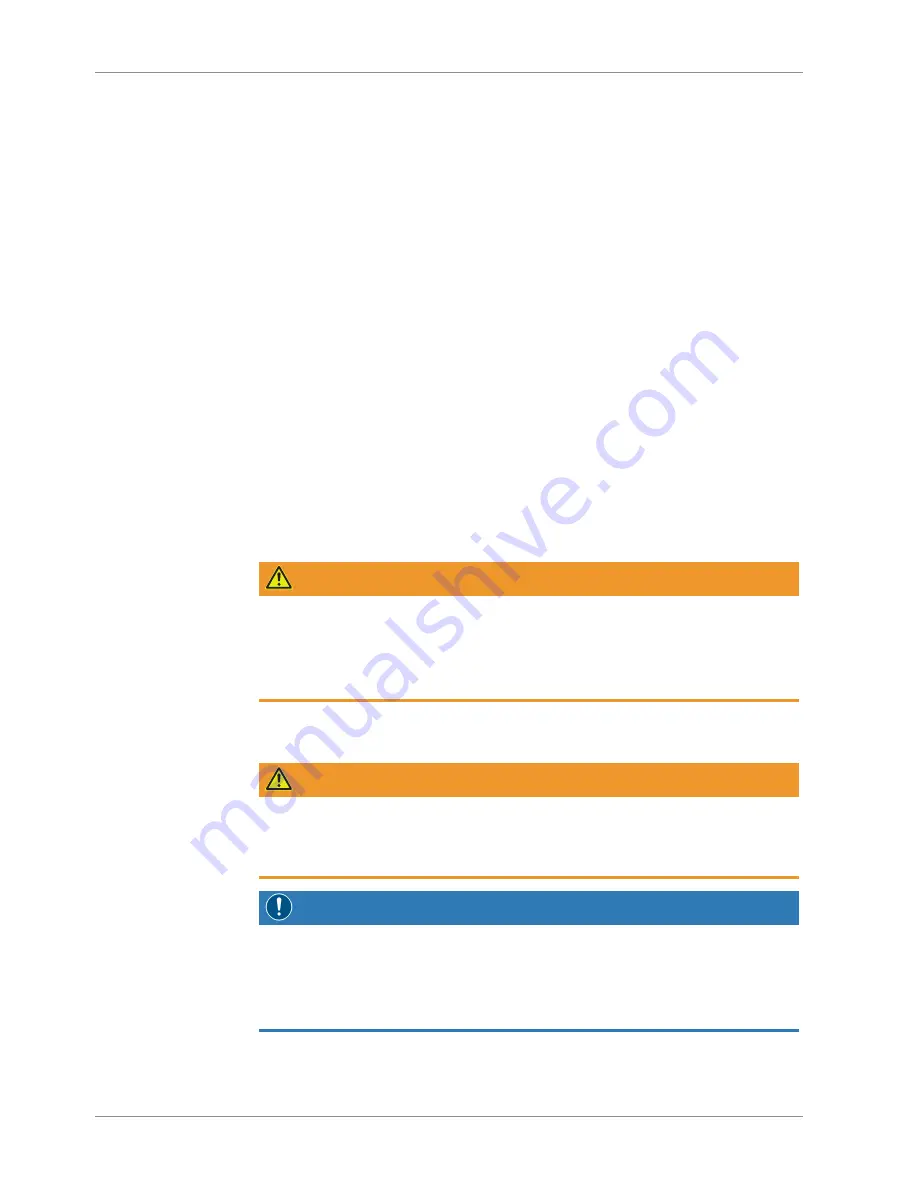
5 | Installation
8 / 28
0870169116_RH0003-0021B_-0002_IM_en
• Make sure that the installation space or location is vented such that sufficient cooling
of the machine is provided.
• Make sure that cooling air inlets and outlets of the motor fan are not covered or ob-
structed and that the cooling air flow is not affected adversely in any other way.
• Make sure that the oil sight glass (OSG) or the oil level indicator (OLI) remains easily
visible.
• Make sure that enough space remains for maintenance work.
• Make sure that the machine is placed or mounted horizontally, a maximum of 1° in
any direction.
• Check the oil level, fill up if necessary, see
Filling Oil [
}
10]
.
• Make sure that all provided covers, guards, hoods, etc. are mounted.
If the machine is installed at an altitude greater than 1000 meters above sea level:
• Contact your Busch representative, the motor should be derated or the ambient
temperature limited.
5.2 Connecting Lines / Pipes
• Make sure that the connection lines cause no stress on the machine‘s connection, if
necessary use flexible joints.
• Make sure that the line size of the connection lines over the entire length is at least as
large as the connections of the machine.
In case of very long connection lines it is advisable to use larger line sizes in order to
avoid a loss of efficiency. Seek advice from your Busch representative.
WARNING
Internal pressure higher than 300 hPa (gauge).
Risk of severe injury!
Risk of damage to the machine!
• Make sure that the discharge line is not clogged (either pipe or oil mist separator).
5.2.1 Suction Connection
WARNING
Unprotected suction connection.
Risk of severe injury!
• Do not put hand or fingers in the suction connection.
NOTICE
Intruding foreign objects or liquids.
Risk of damage to the machine!
In case of the inlet gas contains dust or other foreign solid particles:
• Install a suitable filter (5 micron or less) upstream the machine.
Connection size:
– ISO-KF 25