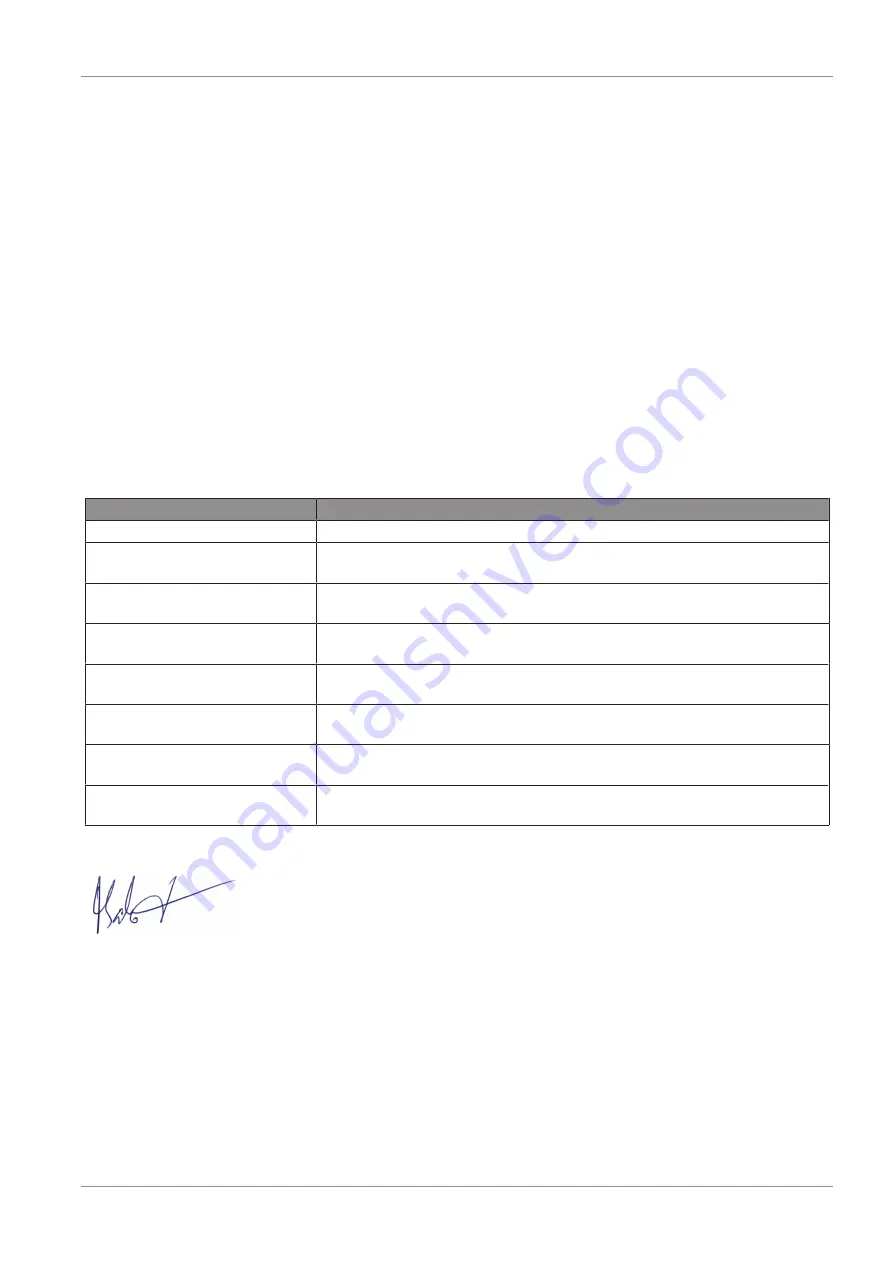
EU Declaration of Conformity | 14
Instruction Manual R5 RA 0155 A_EN_en
25 / 28
14 EU Declaration of Conformity
This Declaration of Conformity and the CE-mark affixed to the nameplate are valid for the machine within the
Busch scope of delivery. This Declaration of Conformity is issued under the sole responsibility of the manufacturer.
When this machine is integrated into a superordinate machinery the manufacturer of the superordinate machinery
(this can be the operating company, too) must conduct the conformity assessment process for the superordinate
machine or plant, issue the Declaration of Conformity for it and affix the CE-mark.
The manufacturer
Busch Produktions GmbH
Schauinslandstr. 1
DE-79689 Maulburg
declares that the machine(s):
R5 RA 0155 A
has (have) been manufactured in accordance with the European Directives:
– ‘Machinery’ 2006/42/EC
– ‘Electromagnetic Compatibility’ 2014/30/EU
– ‘RoHS’ 2011/65/EU + Commission Delegated Directive (EU) 2015/863, restriction of the use of certain haz-
ardous substances in electrical and electronic equipment
and the following standards:
Standard
Title of the Standard
EN ISO 12100 : 2010
Safety of machinery - Basic concepts, general principles of design
ISO 13857 : 2019
Safety of machinery - Safety distances to prevent hazard zones being reached
by the upper and lower limbs
EN 1012-1 : 2010
EN 1012-2 : 1996 + A1 : 2009
Compressors and vacuum pumps - Safety requirements - Part 1 and Part 2
EN ISO 2151 : 2008
Acoustics - Noise test code for compressors and vacuum pumps - Engineering
method (grade 2)
IEC 60204-1 : 2016
Safety of machinery - Electrical equipment of machines - Part 1: General re-
quirements
IEC 61000-6-2 : 2016
Electromagnetic compatibility (EMC) - Generic standards. Immunity for indus-
trial environments
IEC 61000-6-4 : 2018
Electromagnetic compatibility (EMC) - Generic standards. Emission standard
for industrial environments
EN ISO 13849-1 : 2015
(1)
Safety of machinery - Safety-related parts of control systems - Part 1: General
principles for design
(1)
In case control systems are integrated.
Maulburg, 01.06.2020
Dr. Martin Gutmann
General Manager
Summary of Contents for R5 RA 0155 A
Page 26: ...Note ...
Page 27: ...Note ...