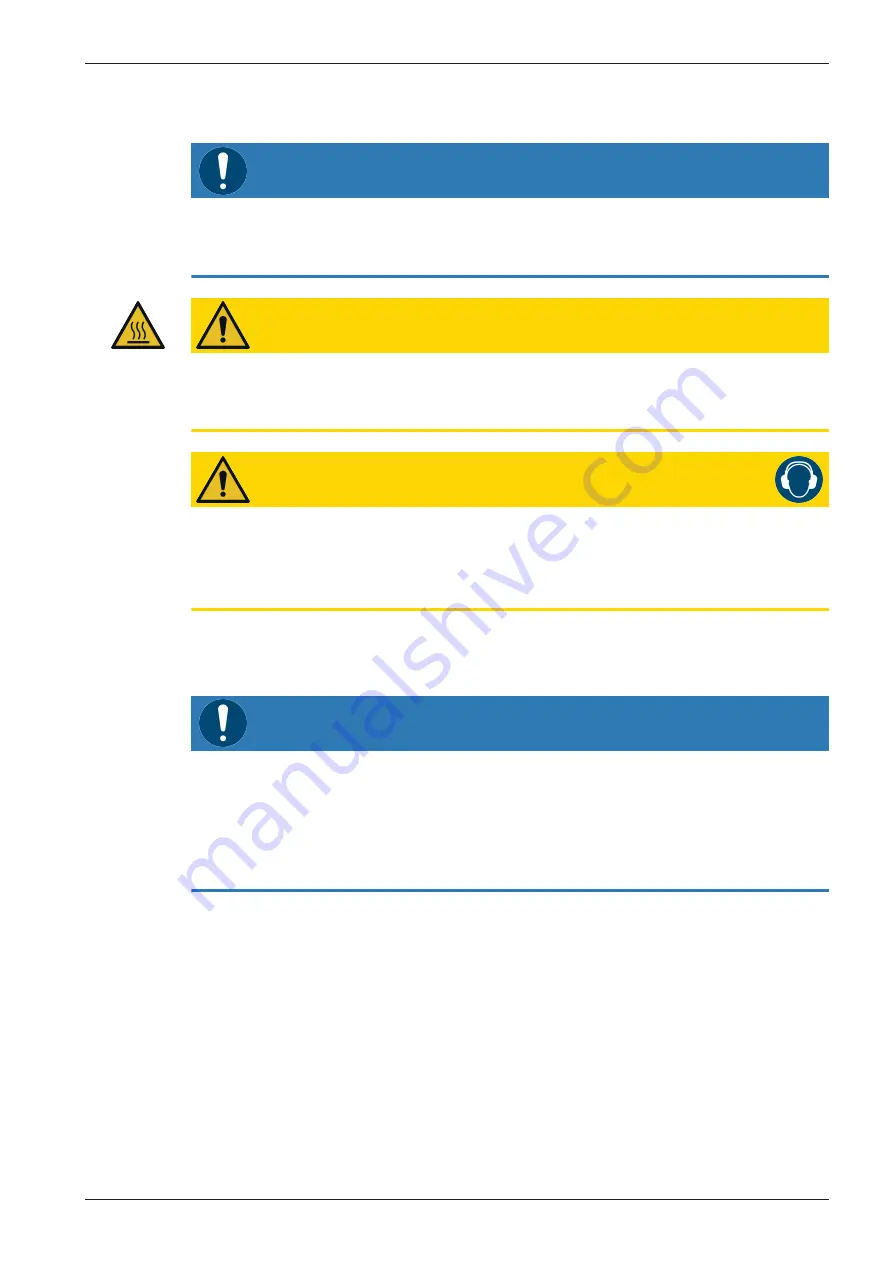
Commissioning | 6
Instruction Manual MINK MV 0500-0600 B_EN_en
15 | 40
6
Commissioning
NOTICE
Lubricating a dry running machine (compression chamber).
Risk of damage to the machine!
●
Do not lubricate the compression chamber of the machine with oil or grease.
CAUTION
During operation the surface of the machine may reach temperatures of more than 70°C.
Risk of burns!
●
Avoid contact with the machine during and directly after operation.
CAUTION
Noise of running machine.
Risk of damage to hearing!
If persons are present in the vicinity of a non noise insulated machine over extended periods:
●
Make sure that ear protection is being used.
●
Make sure that the installation conditions (see
10]) are met.
●
Switch on the machine.
NOTICE
Frequent starts and stops by connecting and disconnecting from the power supply.
Risk of damage to the machine!
Starting the machine by connecting and disconnecting the power supply is permitted max. 1x per
minute. Between disconnecting and connecting at least 10 seconds must have been passed. If the
process requires more frequent starts/stops of the machine:
●
Use the digital start signal.
●
Maximum permissible number of starts by using the digital signal: unlimited
As soon as the machine is operated under normal operating conditions:
●
Measure the motor current and record it as reference for future maintenance and
troubleshooting work.