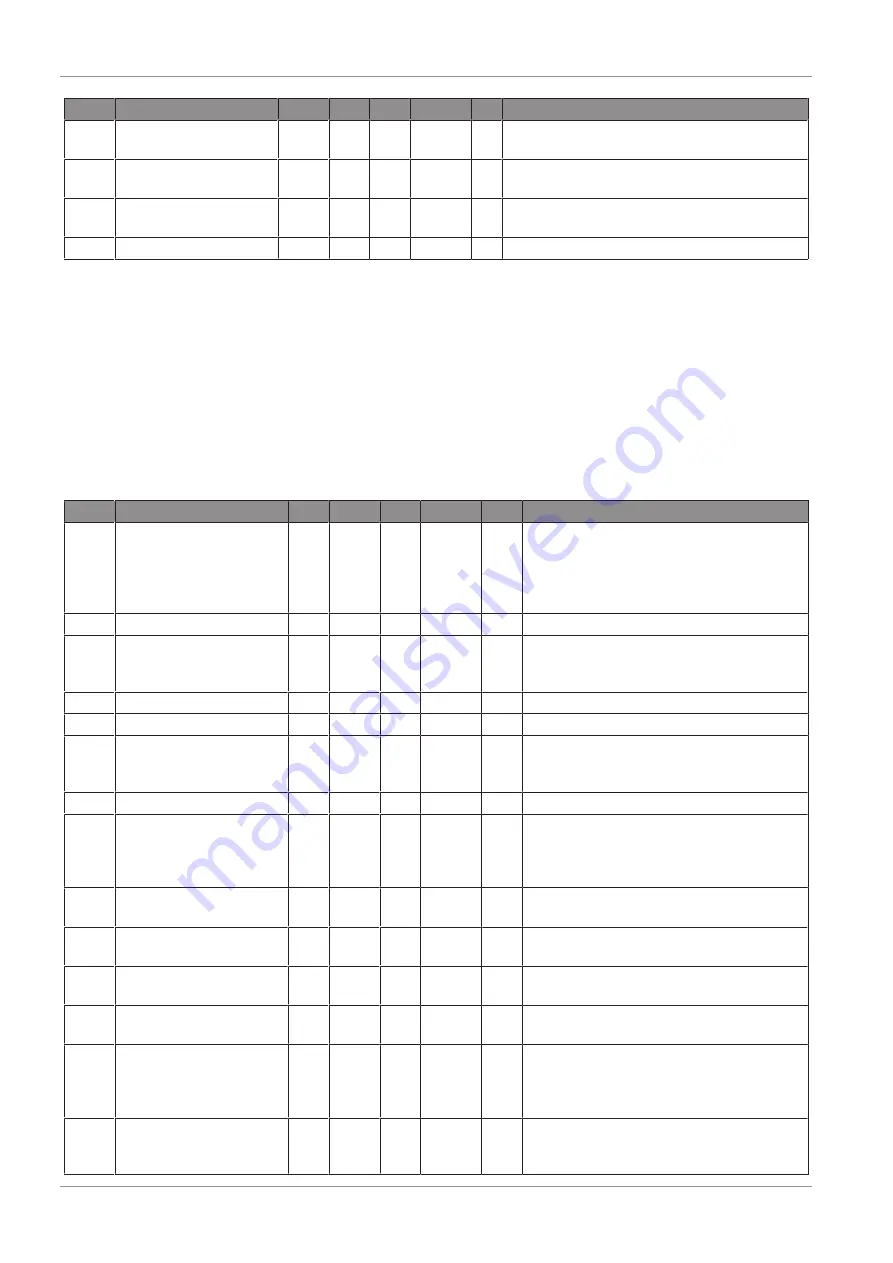
7 | Parameter Overview
22 / 56
0870166596_MV0040-0080C-D_PCI_A0004_IM_de_MD
Code Parameter
Min.
Max. Unit Default ID
Description
P8.18 Disable overvoltage
regulator
0
1
0
0 = Enable
1 = Disable
P8.19 Disable undervoltage
regulator
0
1
0
0 = Enable
1 = Disable
P8.20 Motor type
0
1
1
0 = Asynchronous motor
1 = Synchronous motor
P8.21 Torque boost
1
160
Hz
8
Frequency of maximum torque boost
*Depending on motor and machine sizes.
Visibility of the group depends on P1.16
7.11 Protections: Menu PAR G9
Parameters of Stall Protection (P9.4 to P9.6)
The motor Stall Protection protects the motor from short time overload situations such as one caused
by a stalled shaft. The stall state is defined with two parameters, P9.5 (Stall Time) and P9.6 (Stall Fre-
quency Limit). If the current is as high as the P1.5 (Current Limit) and the current limiter has reduced
the output frequency below the P9.6 for the time P9.5 than the set limit the stall state is true. There is
actually no real indication of the shaft rotation. Stall Protection is a type of overcurrent protection.
Code Parameter
Min. Max.
Unit Default ID
Description
P9.1
Respond to 4 mA
reference fault
(< 4 mA)
0
4
1
700
0 = No action
1 = Warning
2 = Fault
3 = Warning if start active
4 = Fault if start active
P9.2
4 mA fault detection time
0
10
s
0.5
1430 Time limit
P9.3
Earth fault protection
0
2
2
703
0 = No action
1 = Warning
2 = Fault
P9.4
Motor stall protection
0
2
2
709
See P9.3
P9.5
Motor stall delay
0
300
s
5
711
Maximum allowed time for stall stage.
P9.6
Motor stall minimum
frequency
0.1
320
Hz
15
712
For a stall state to occur, the output fre-
quency must have remained below this
limit for a certain time.
P9.7
Underload protection
0
2
0
713
See P9.3
P9.8
Underload load curve at
nominal frequency
10
150
%
50
714
This parameter gives the value for the
minimum torque allowed when the output
frequency is above the field weakening
point.
P9.9
Underload load curve at
zero frequency
5
150
%
715
This parameter gives value for the min-
imum torque allowed with zero frequency.
P9.10 Underload time
1
300
s
716
Maximum allowed time for underload
state to exist.
P9.11 Thermal protection of the
motor
0
2
704
See P9.3
P9.12 Motor ambient
temperature
-20
100
°C
705
Ambient temperature in °C
P9.13 Motor cooling factor at
zero speed
0
150
%
706
Defines the cooling factor at zero speed in
relation to the point where the motor is
running at nominal speed without external
cooling.
P9.14 Motor thermal time
constant
1
200
min
707
The time constant is the time within which
the calculated thermal stage has reached
63% of its final value.
Summary of Contents for Mink MV 0040 C
Page 55: ...Note ...