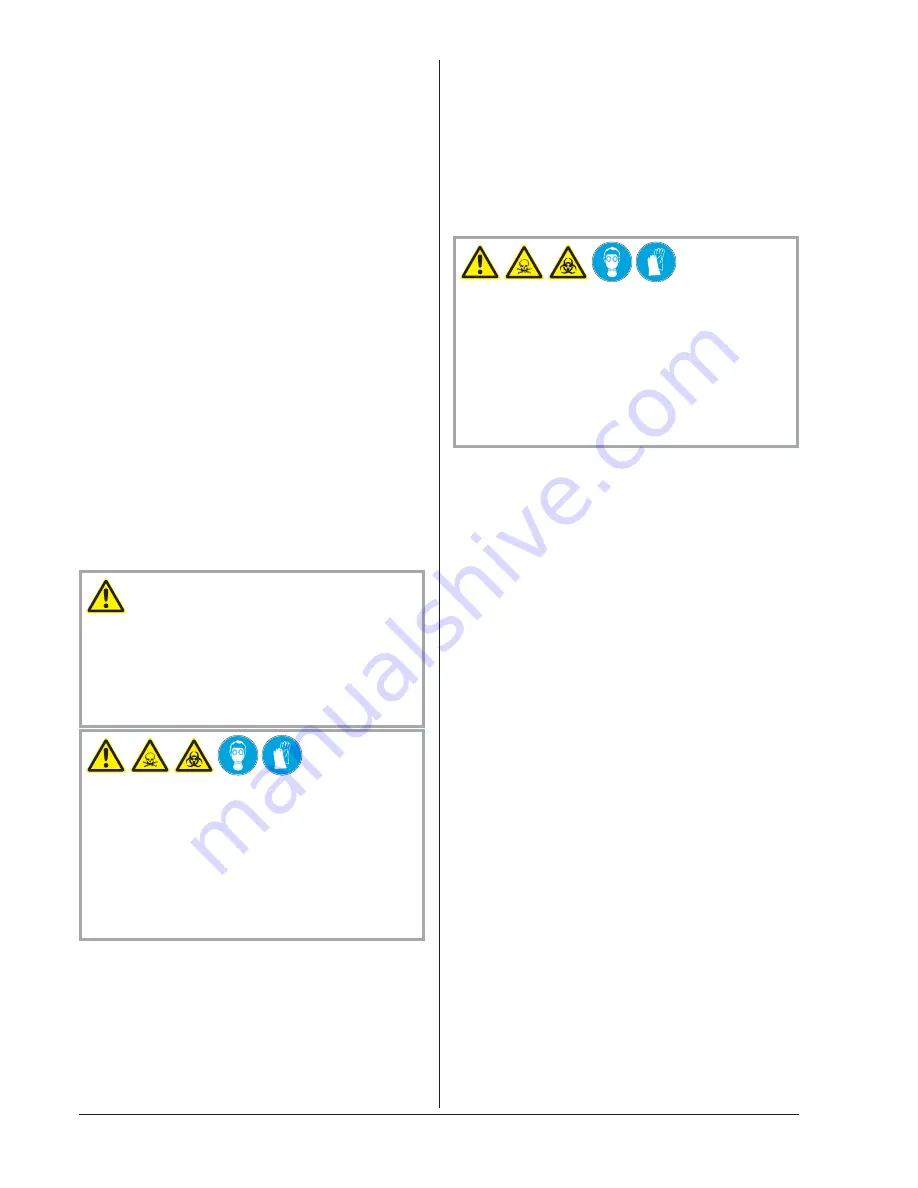
In case an inlet air filter (b) is installed:
◆
Replace the inlet air filter (b)
●
Check the inlet screen (715), clean if necessary
Every 20000 Operating Hours, At the Latest after
6 Years:
Note
gear oil Busch VS 150 only. Other gear oils reduce the change interval.
●
Change the synchronising gear oil
Changing Synchronising Gear Oil
●
Make sure that the compressor is shut down and locked against in-
advertent start up
●
Undo the venting valve (e, 72) for venting
●
Place a drain tray underneath the drain plug (h, 80)
●
Open the drain plug (h, 80) and drain the oil
●
Make sure that the seal ring (81) on the drain plug (h, 80) is ser-
viceable, replace if necessary
●
Firmly reinsert the drain plug (h, 80) together with the seal ring
(81)
●
Remove the venting valve (e, 72) completely
●
Fill in new gear oil until the level is slightly above the middle of the
sight glass (g, 76)
●
Make sure that the seal ring on the venting valve (e, 72) is undam-
aged, if necessary replace the venting valve (e, 72)
●
Firmly reinsert the venting valve (e, 72) together with the seal ring
●
Dispose of the used oil in compliance with applicable regulations
Overhaul
CAUTION
In order to achieve best efficiency and a long life the compressor
_a
was assembled and adjusted with precisely defined tolerances.
This adjustment will be lost during dismantling of the compressor.
It is therefore strictly recommended that any dismantling of the
compressor that is beyond of what is described in this manual shall
be done by Busch service.
DANGER
In case the compressor conveyed gas that was contaminated with
_age32
foreign materials which are dangerous to health, harmful material
can reside in pores, gaps and internal spaces of the compressor.
Danger to health during dismantling of the compressor.
Danger to the environment.
Prior to shipping the compressor shall be decontaminated as good
as possible and the contamination status shall be stated in a “Dec-
laration of Contamination” (form downloadable from
www.busch-vacuum.com).
Busch service will only accept compressors that come with a completely
filled in and legally binding signed “Declaration of Contamination”
Removal from Service
Temporary Removal from Service
●
(form downloadable from www.busch-vacuum.com).
Prior to disconnecting pipes/lines make sure that all pipes/lines are
vented to atmospheric pressure
Recommissioning
●
Observe the chapter Installation and Commissioning (
page 4)
Dismantling and Disposal
DANGER
In case the compressor conveyed gas that was contaminated with
_age32
foreign materials which are dangerous to health, harmful material
can reside in pores, gaps and internal spaces of the compressor.
Danger to health during dismantling of the compressor.
Danger to the environment.
During dismantling of the compressor personal protective equip-
ment must be worn.
The compressor must be decontaminated prior to disposal.
●
Drain the oil
●
Make sure that materials and components to be treated as special
waste have been separated from the compressor
●
Make sure that the compressor is not contaminated with harmful
foreign material
According to the best knowledge at the time of printing of this manual
the materials used for the manufacture of the compressor involve no
risk.
●
Dispose of the used oil in compliance with applicable regulations
●
Dispose of the compressor as scrap metal
Maintenance
MI 1502 BP
page 8
0870152627 / 101117
: The change interval of 20000 operating hours is valid for the