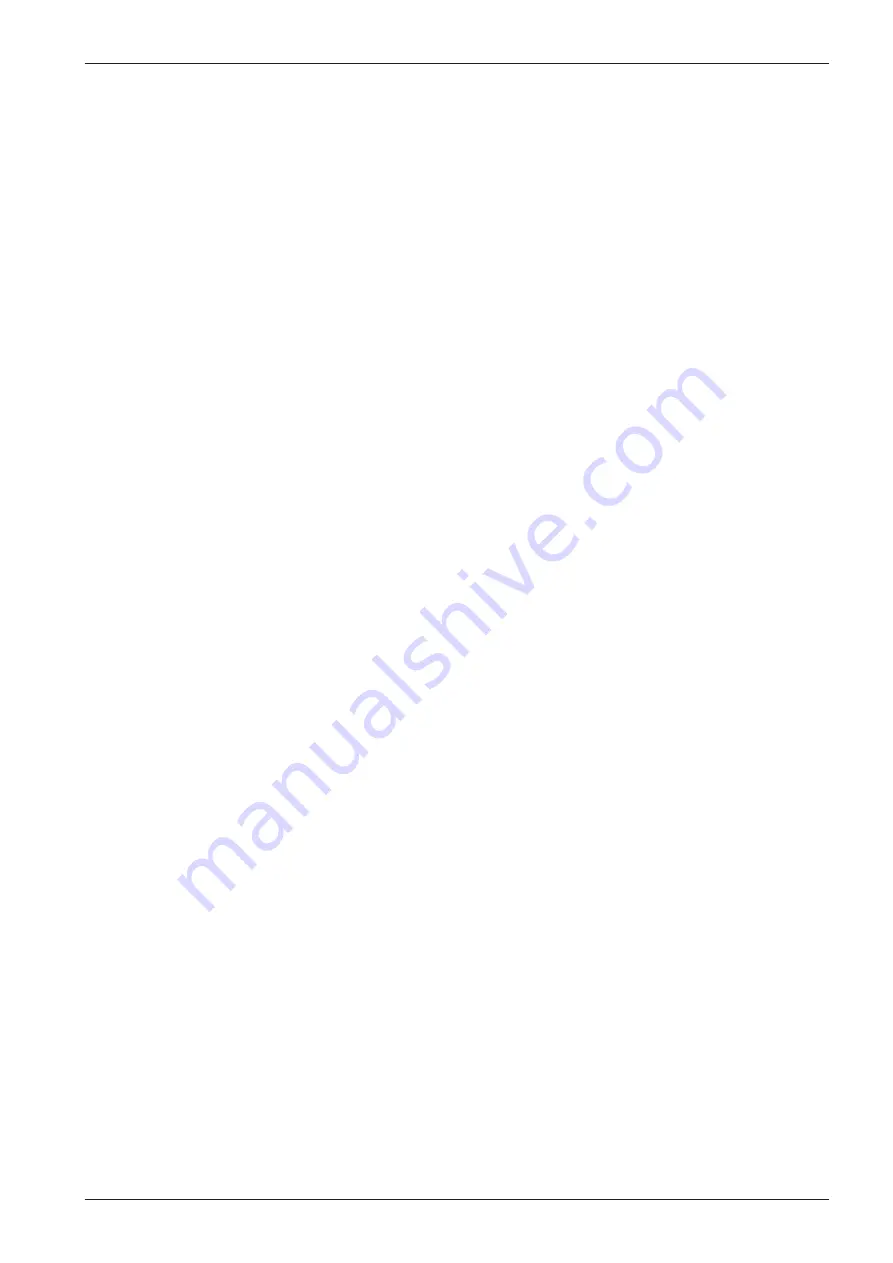
Product Description | 2
Instruction Manual Supplement DOLPHIN VL Systems_EN_en
9 | 36
Operating liquid control valve (OPC) allows the operating liquid flow rate to be regulated for opti-
mum performance of the system, with compound pressure gauge (CG) indicating the operating liq-
uid pressure at the vacuum pump inlet.
The suction non-return valve (NRV) prevents operating liquid from flowing back into the process
when the system stops under vacuum.
2.4.2
Partial Recovery (Open Circuit)
Approximately 50% of the operating liquid is recirculated within the system whilst additional liquid is
added via the fresh liquid line to maintain the liquid temperature. The process gas and operating liq-
uid are discharged from the vacuum pump together into the separator vessel (SV) where they are
separated. The gas leaves through the discharge connection, whilst the operating liquid level is
maintained as excess liquid drains from the separator overflow connection (OPO). The level indicator
(LI) provides visual indicator of the liquid level in the system.
Through the site control system (by others) the operating liquid temperature is monitored by resis-
tance thermometer (TSA1) opening and closing the solenoid valve (OPV) to allow fresh cooler liquid
into the system. Recommended temperature variation around the set point for switching is 3°C.
At the operating liquid inlet the Y-strainer (ST) prevents particles greater than 0.1 mm entering the
vacuum pump.
The manual fresh liquid isolation valve (IV) allows the system liquid inlet to be isolated whilst the
strainer is cleaned.
Operating liquid control valve (OPC) allows the operating liquid flow rate to be regulated for opti-
mum performance of the system.
Suction non return valve (NRV) prevents operating liquid from flowing back into the process when
the system stops under vacuum.
2.4.3
Total Recovery (Closed Circuit)
All the operating fluid is recirculated within the system allowing liquid other than water to be used
as the operating liquid. Constant liquid temperature in the system is maintained by a heat exchang-
er with a separate cooling liquid supply. The process gas and operating liquid are discharged from
the vacuum pump together into the separator vessel (SV), where they are separated. The gas leaves
through the discharge connection whilst high operating liquid level (condensing suction load) is pre-
vented by excess liquid draining from the separator overflow connection (OPO).
Through the site control system (by others) the operating liquid level is increased by the solenoid
valve (OPV) opening with low level signal from the low level switch. Valve closes on signal from the
high level switch. The level indicator (LI) provide visual indication of the liquid level in the system. At
the operating liquid inlet the strainer (ST) prevents particles greater than 0.1 mm entering the vacu-
um pump.
The manual fresh liquid isolation valve (IV) allows the system liquid inlet to be isolated whilst the Y-
strainer is cleaned.
Operating liquid control valve (OPC) allows the operating liquid flow rate to be regulated for opti-
mum performance of the system.
Suction non return valve (NRV) prevents operating liquid from flowing back into the process when
the system stops under vacuum.