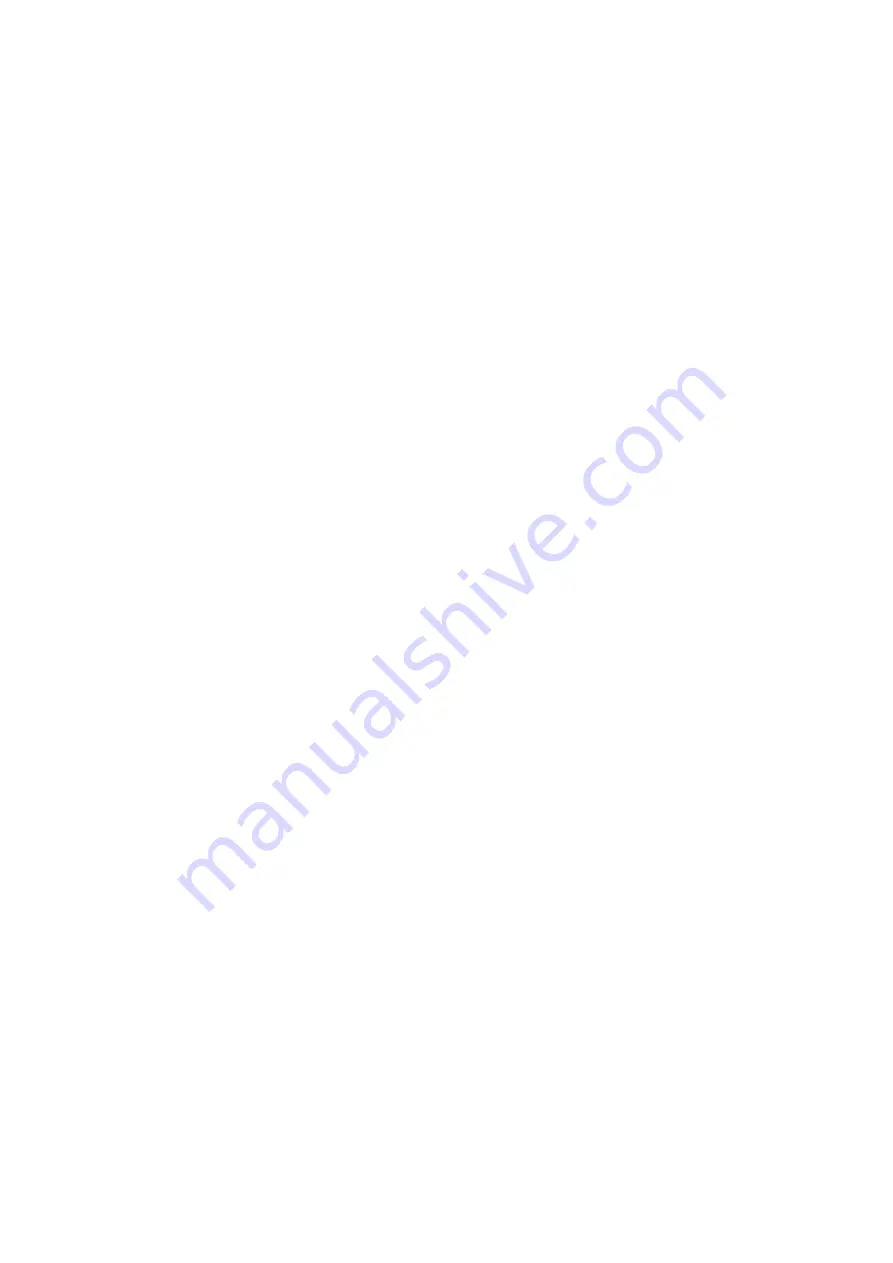
Argentina
Australia
Austria
Bangladesh
Belgium
Brazil
Canada
Chile
China
Colombia
Czech Republic
Denmark
Finland
France
Germany
Hungary
India
Ireland
Israel
Italy
Japan
Korea
Malaysia
Mexico
Netherlands
New Zealand
Norway
Peru
Poland
Portugal
Romania
Russia
Singapore
South Africa
Spain
Sweden
Switzerland
Taiwan
Thailand
Turkey
United Arab Emirates
United Kingdom
USA
www.buschvacuum.com
Busch
Vacuum Solutions
We shape vacuum for you.
0870551589/A0002_en
Summary of Contents for COBRA NC 1000 B
Page 31: ...Note...