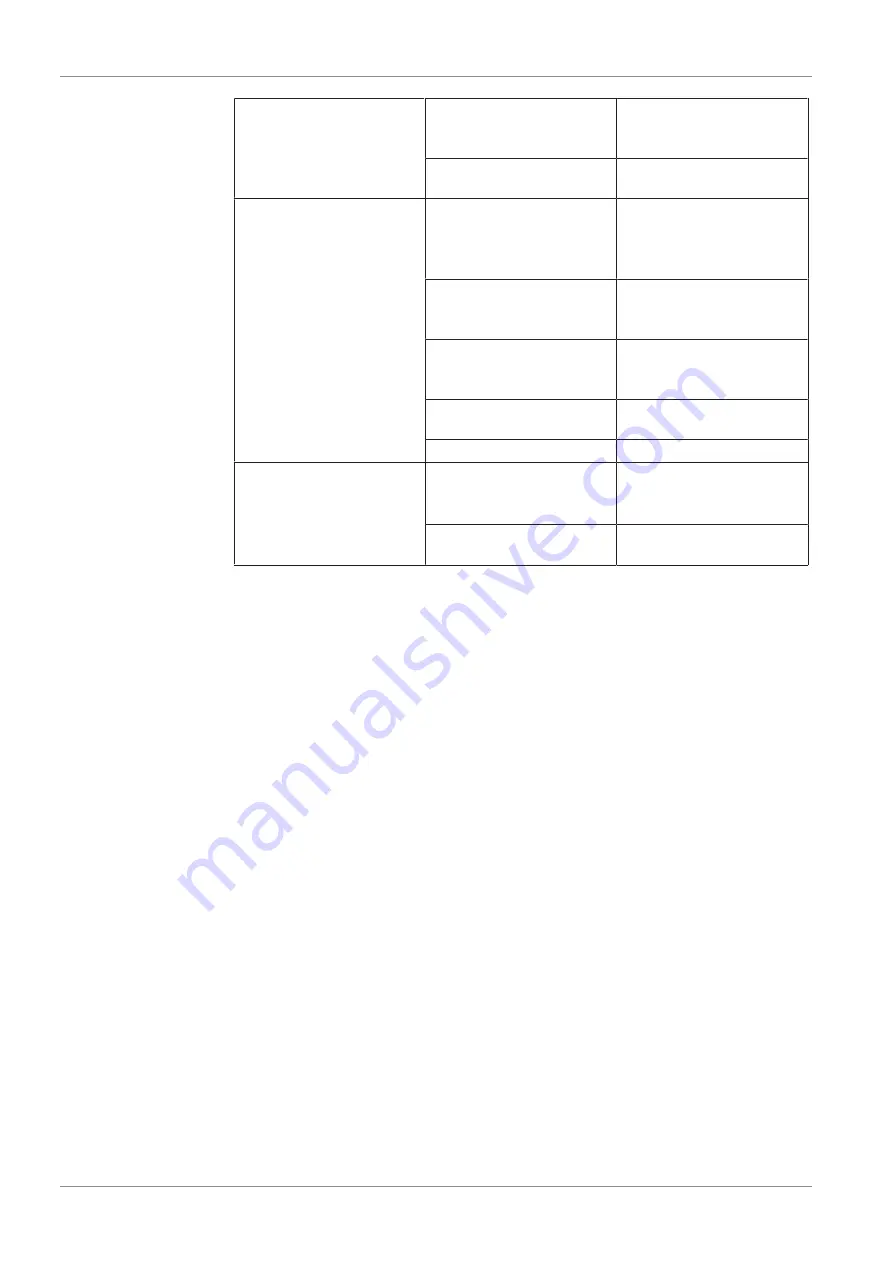
11 | Troubleshooting
54 / 60
0870203597_NC0100-0300B_WCV_Ex_-0001_IM_en
The machine runs very nois-
ily.
Wrong oil quantity or un-
suitable oil type.
• Use one of the recom-
mended oils in the correct
quantity, see
.
Defective gears, bearings or
coupling element.
• Repair machine (contact
Busch).
The machine runs too hot.
Insufficient cooling.
• Make sure to comply with
the cooling water require-
ments, see
Ambient temperature too
high.
• Observe the permitted
ambient temperature, see
Temperature of the process
gases at the inlet too high.
• Observe the permitted
gas inlet temperature, see
The cooling water pump is
defective.
• Repair the machine.
Oil level too low.
• Top up oil.
The oil is black.
Oil change intervals are too
long.
• Drain the oil and fill in
new oil, see
.
The machine runs too hot.
• See problem "The ma-
chine runs too hot".
For the solution of problems not mentioned in the troubleshooting chart contact your
Busch representative.
Summary of Contents for COBRA ATEX NC 0100-0300 B
Page 58: ...Note ...
Page 59: ...Note ...