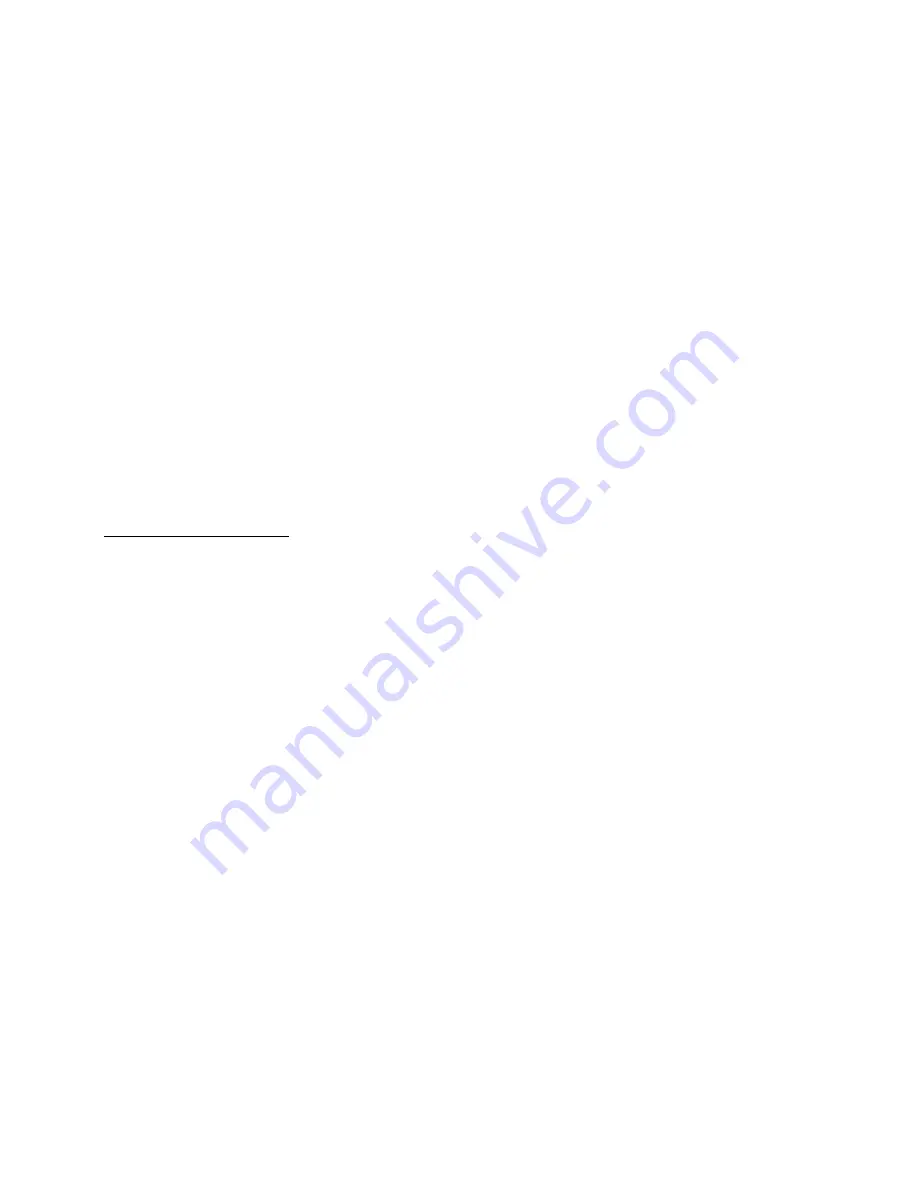
24
ASSET NUMBER
This function allows the operator to enter the machine's
asset number. This can be useful for tracking the usage
or service of an individual machine within a group.
Procedure to enter the asset number:
1. Press and hold the right hidden button until the
display reads
RECIPES.
Press the right hidden
button until the display reads
SERVICE
, then press
SELECT
. Press and release the right hidden switch
until the display reads
ENTER ASSET #?
2. Select
YES
. The display will now read
ANXXXXXX
.
3. Scroll down
(-)
or up
(+)
, to set the asset number
of the machine.
NOTE
: Starting from the right, each
digit will control the next digit, like an odometer.
4. When finished, press and release
DONE
. The display
will now read
SERVICE #
. To exit programming and
return to the
MAIN SCREEN
, press
ENABLE BREW
ON/OFF
switch.
NOTE
: To view the Asset Number, press and hold the
left hidden switch until the display reads
ASSET
NUMBER
. After releasing the switch, the display will
read
SERIAL NUMBER
then the software version.
SERVICE NUMBER
This function allows the operator to enter in the tele-
phone number to call if service is needed. The service
number will be displayed anytime there is a fault mes-
sage displayed.
Procedure to enter the service number:
1. Press and hold the right hidden button until the
display reads
RECIPES.
Press the right hidden
button until the display reads
SERVICE
, then press
SELECT
. Press and release the right hidden switch
until the display reads
ENTER SERVICE #?
2. Press and release
YES
. The display will now read
SCROL THRU #'S NEXT ->NEXT NUMBER,
followed
by
000-000-0000
. UP TO 16 CHARACTERS ARE
AVAILABLE.
3. Press the
SCROL
button to scroll through the num-
bers. When the desired number is shown, press
and release
NEXT
to move to the next digit in the
phone number.
4. Repeat Step 3 until the entire number is entered.
5. Press and release
DONE
. The display will now read
BREW COUNTERS
SERVICE
(FOR AUTHORIZED SERVICE PERSONNEL ONLY)
This function allows the testing of individual components
and the ability to check switches for proper function. This
function also tests the funnel sensor coil’s frequency
(diagnostic tool for troubleshooting purposes only).
Refer to Service Manual for in depth procedures.
Test Outputs:
The following components can be individually tested:
(L/R) Brew Valve(s)
(L/R) Bypass Valve(s) ITCB HV/ICB(TWIN)
(L/R) Dilution Valve(s) ITB/ITCB/HV (w/Dual Dilution)
Refill Valve
Tank Heater Relay
Tank Heater Triac
L/R Funnel Lock (Optional)
Sweetener Solenoid (Optional)
Test Switches:
The following components can be individually tested:
Membrane Switches
Test Frequency:
(NOT AVAILABLE ON ITB)
The following components can be individually tested:
L/R Smart Funnel read coils.
FACTORY DEFAULTS
This function allows the operator to erase
ALL
of the
previously entered recipes and ad messages. Factory-
set default values will replace
ALL
previous settings.
Procedure to set factory defaults:
1. Press and hold the right hidden button until the
display reads
RECIPES.
Press the right hidden
button until the display reads
SERVICE
, then press
SELECT
. Press and release the right hidden switch
until the display reads
FACTORY DEFAULTS
.
2. Press
YES
to restore defaults. The display will read
WILL REPLACE ALL BREW SETTINGS
followed with
ARE YOU SURE?
3. Selecting
NO,
will exit without resetting. Select
YES
to load the defaults. After factory defaults have
been restored, the display will return to the
MAIN
SCREEN
. The factory default values will have replaced
ALL
previously entered values. It will NOT reset the life
brew counter. If factory defaults are restored, it will be
necessary to recalibrate the flow rates.
PROGRAMMING BREWER (cont.)
PROGRAMMING FUNCTIONS (cont.)