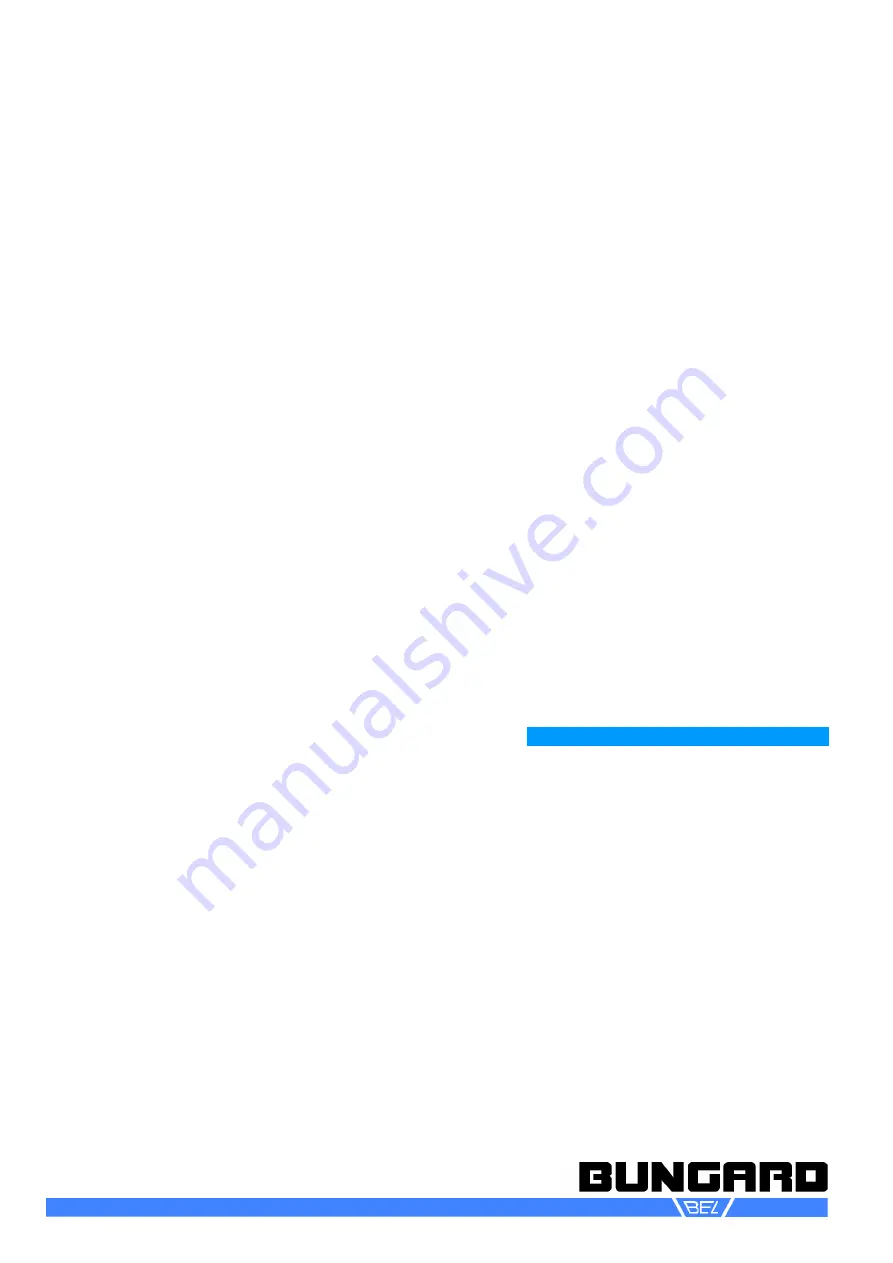
Page 6 / 8
Rectifier:
The rectifier has a separate on / off switch.
Current and voltage are preset manually by
potentiometer and read out by analog cur-
rent and voltage displays.
The rectifier offers constant current and con-
stant voltage supply.
For use with ABC chemistry we only need
constant current supply.
For that reason adjust the voltage (un-
loaded) to approx. 2 V.
Then adjust current according to PCB sur-
face in use. Standard working current setting
is 3 A/dm².
Through Hole Plating process sequence:
Cut your PCB to size with our board cutter
NE-CUT ensuring that the blank size is
about 20 mm larger than the required PCB
size.
Drill your blank board to the required hole
pattern by using our BUNGARD CCD or sim-
ilar. Note: allow + 0,05 to + 0,1mm extra dia-
meter for the drill bits because copper plat-
ing in the holes will reduce the effective dia-
meter.
After that use one of our brushing machines
(RBM series) for scrub cleaning, washing
and drying (if no brushing machine available,
brush and clean manually).
Fix the cleaned and deburred board in the
COMPACTA 3-finger board-holder and fix it
on the leftmost conveyor arm (bath1). Turn
on the switch for the conveyor. Process the
board in the bathes 1 to 4 and 6 from the left
to the right, in the sequence and with the
timings from the enclosed Process Flow
Table.
A step indication of "R" in this Flow Table
means a rinse step, consisting of a static
rinse in each of the two cascade rinse tanks
and a subsequent spray rinse.
The aim of bath 2, the Pre-Dip, is to protect
the expensive catalyst in bath 3 from intru-
sion of both other chemicals and rinse water.
That is why you must not rinse after Pre-Dip
but you have to go directly to the following
bath 3!
With the oscillating frame still moving and
the rectifier switched on and preset and the
air agitation switched on you now fix the
board over the galvanic plating bath.
Adjust correct current immediately (without
current you risk to etch off all catalyst ap-
plied). Standard working current setting is 3
A / dm².
Example:
Board size 200 x 300mm = 6 dm², 3 A /
dm² x 2 sides at 6 dm² = 3 x 2 x 6 = 36 A.
Every minute in the copper plating bath will
apply
0,7µm
copper.
Example:
18µm copper will be applied in 26 minutes of
copper plating.
Adjust timer accordingly and leave board in
the plating bath as long as necessary.
After that rinse carefully and dry the board
immediately to avoid oxidisation.
Cleaning and maintenance
Cleaning
The unit is made of PVC. Do not use organic
solvents to clean the machine. A cloth is un-
der normal conditions sufficient for cleaning.
For very resistant dirt (for example baked on
residues) use sulphuric acid for tanks 1,4
and 6 or diluted hydrochloric acid for tanks 2
and 3. After cleaning the inner of tank 3 re-
move all cloth fuzzles and rinse the tank
walls and ground with demineralized water.
Replenishment
Once your baths have been initially made
up, they can be easily replenished by simply
adding the appropriate product. See the in-
structions on the following Plating System
Step descriptions. Missing replenishment will
spoil the bath.
COMPACTA 30
Through hole plating machine
Instructions for use