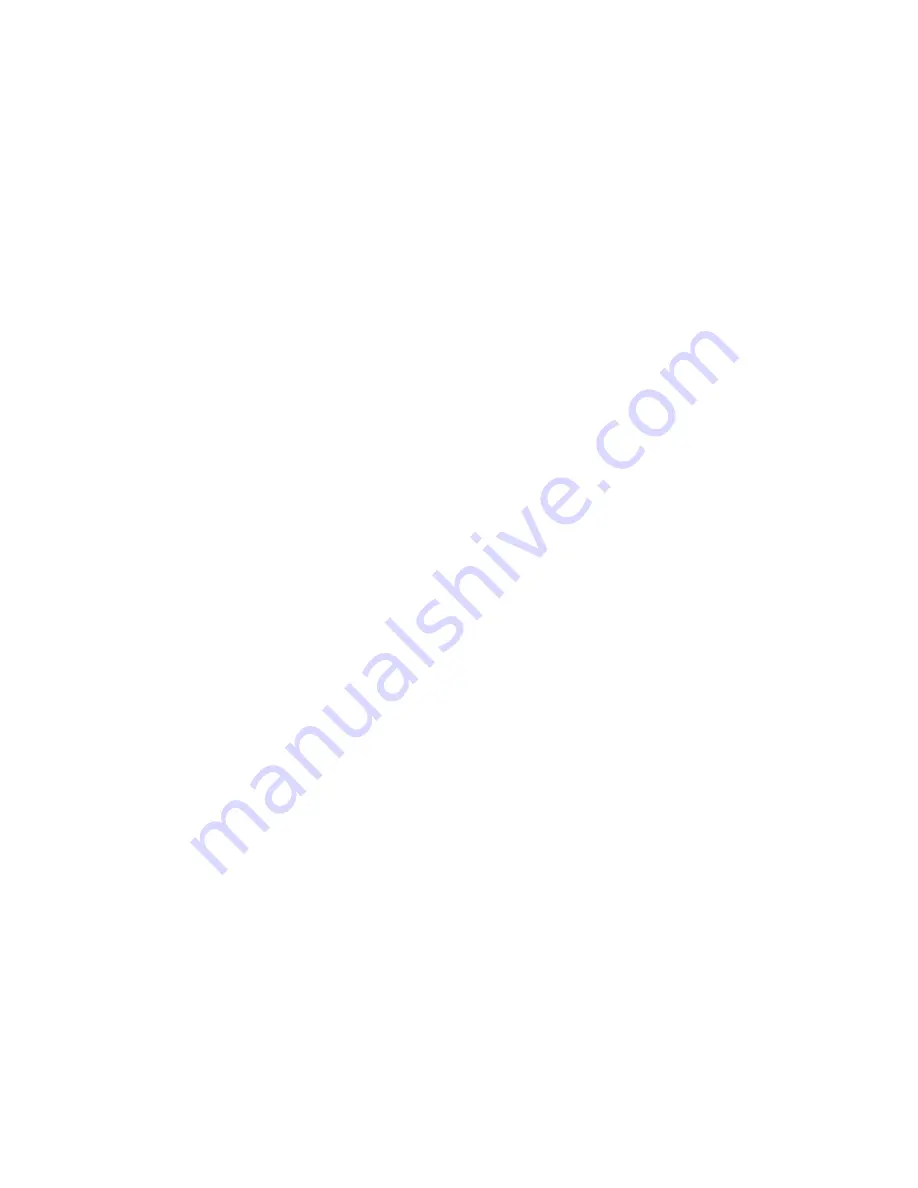
12
To program a complete new shape ( press ‘A’ ):
Count the number of segments or operations and enter the total.
For each segment, enter:
TYPE:
select from 1 through 8
Quadrant: 1,2,3 or 4; refer to chart
Size:
One or more dimensions per segment as described below; 100 per inch
or 10 per mm ( depending on machine version ); or for time, 100 per sec.
of delay. Eg. 150 = 1.5", or for metric 375 = 37.5 mm
Detailed description of TYPES :
Type 1.
Clockwise, 90
0
arc segments.
Quadrant determined by which quarter of a full circle makes the arc. (See chart) .
Dimensions required: Radius only.
Type 2.
Counterclockwise, 90
0
arc segments.
Quadrant determined by which quarter of a full circle makes the arc. (See chart).
Dimensions required: Radius only.
Type 3.
Line along X or Y axis.
Quadrant determined by direction of movement. (See chart)
( East: 1, North: 2, West: 3, South: 4 ).
Dimensions required : Length only.
Type 4.
Angled straight line.
Quadrant determined by direction of movement. (See chart)
(NE: 1, NW: 2, SW: 3, SE: 4 ).
Dimensions required : (1) X - dimension ; movement along X axis
(2) Y - dimension ; movement along Y axis
Type 5.
Functions or other operations.
Quadrant by selecting function. ( See chart )
1.
Weld/oxygen ON : turn ON weld contact relay or cutting oxygen solenoid.
Dimensions required : None.
2.
Weld/oxygen OFF.
Dimensions required : None.
3.
Pause : Machine stops and waits until Start/Run button is pushed again.
Dimensions required : None.
4.
Delay : Machine stops and holds position for a programmed time period, up to 99.99
seconds.
Dimensions required : time in .01 second units. (eg. 2.5 seconds = 250)
DATA ENTRY REQUIRED FOR PROGRAMMING