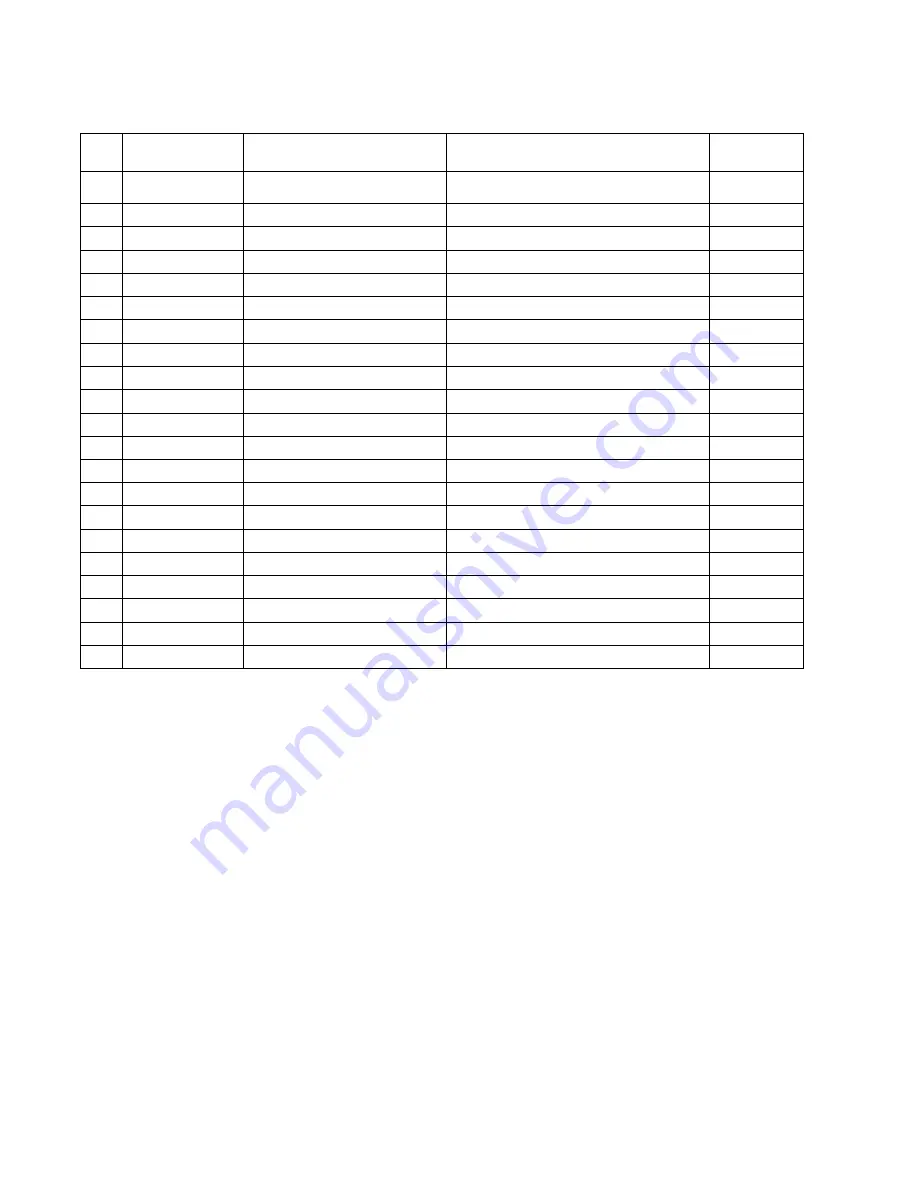
PAGE 16
PARTS LIST
No.
Part Number
Description
Reference
Qty
1
2.05.08.031
Handle
Black 155*42*27
1
2
1.1.01.01.1006
Encloser
PSTICK160KE.2
1
3
1.1.05.02.0558
Main control board
POWERSTICK 80KE (V1.3)
1
4
2.03.30.1235
STICK-TIG toggle switch
BLUEARC 90 STI
1
5
2.03.30.1219
Potentiometer wiring harness
POWER STICK 80KE (V1.0)
1
6
2.03.30.1217
Indicator light wiring harness
POWER STICK 80KE (V1.0)
1
7
2.05.05.961
Front panel
EXTM100-3 ABS 5VA
1
8
1.2.08.02.2108
"-" output cable
CARIARC 80
1
9
1.2.08.01.0518
"+" output cable
ST80i
1
10
2.07.11.016
Potentiometer knob
KDJII23-16-6J
1
11
1.1.01.05.2999
Front panel mounting
PSTICK200KE.1-1
1
12
2.07.28.041
Fast recovery diode
D92-02 20A/200V
4
13
1.1.01.04.1354
Bottom
PSTICK160KE.3-2
1
14
2.07.43.924
Fast recovery diode heat sink
HG2ZX7200KE.2-5
1
15
2.07.33.629
Single tube IGBT
RJH60F5DPK
4
16
2.07.43.925
IGBT heat sink
HG2ZX7200KE.2-3
2
17
2.05.02.458
Supporter
HG2ZX7200KE.2-1
1
18
1.1.12.18.0002
Fan wiring harness
POWER STICK 80KE (V1.0)
1
19
2.05.05.962
Back panel
EXTM100-5 ABS 5VA
1
20
2.07.80.211
Rocker switch
R220-1C2N-BBZ-NN 16A/250V
1
21
1.1.11.18.0090
Power cord
BLUEARC 90STI(POWER STICK 80KE)
1
201604