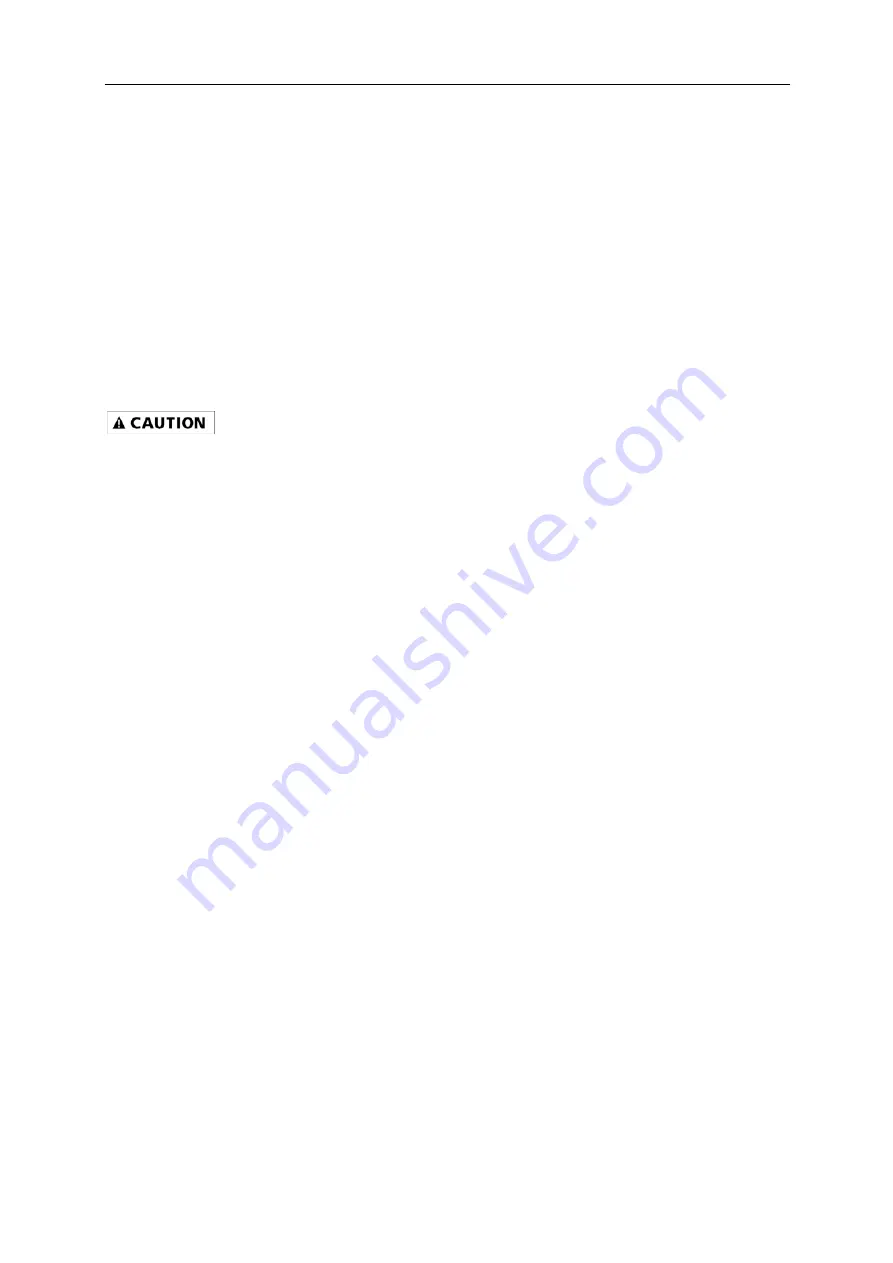
11
Readjust the spool tension using the wing nut as necessary to correct for either problem.
4.2.7.After checking to make sure that your welder is disconnected from the AC power source, free the leading end
of the wire from the spool, but DO NOT LET GO OF IT until it is secure in the drive system or the wire will unspool
itself.
4.2.8. Using a wire cutter, cut the bent end off the leading end of the wire so that only a straight leading end
remains.
4.2.9. Loosen the tension adjusting knob holding the drive tension arm in place and lift the tension arm up off the
drive roller.
4.2.10. Insert the leading end of the wire into the inlet guide tube. Then push it across the drive roller and into the
MIG gun/torch assembly about six inches.
• Make certain that the welding wire is actually going into the torch liner. If not, the wire will jam in the mechanism.
4.2.11 Be sure the wire lines up in the groove of the drive roller then place the drive tension arm back in place
above the drive roller.
4.2.12 Position the quick release drive tension back up into position into the drive tension arm.
4.2.13 Tighten (turn clockwise) the drive tension adjusting knob until the tension roller is applying enough force on
the wire to prevent it from slipping out of the drive assembly. Do not over tighten.
4.2.14. NOW YOU CAN LET GO OF THE WIRE.
4.2.15. Plug in and turn the welder ON. Set the VOLTAGE switch to the voltage (heat) setting recommended for
the gauge metal that is to be welded. Refer to the set up chart on the inside of the wire feed compartment door.
4.2.16. Set the WIRE SPEED control in the middle of the wire speed range.
8.17. Straighten the MIG gun cable, pull the trigger on the welding torch to feed the wire through the torch
assembly. When at least one inch of the wire sticks out past the end of the torch, release the trigger.
4.2.18 Turn the Power Switch to the OFF position.
4.2.19 Select a contact tip stamped with the same diameter as the wire being used.
NOTE:
Due to inherent variances in flux-cored welding wire, it may be necessary to use a contact tip one size larger than
your flux core wire if wire jams occur.
4.2.20. Slide the contact tip over the wire (protruding from the end of the gun). Thread the contact tip into the end of
the gun adaptor and tighten securely.
4.2.21. Install the nozzle on the gun assembly. To keep spatter from sticking to inside of the nozzle use
anti-spatter spray or gel.
4.2.22 Cut off the excess wire that extends more than
¼
” past the end of the nozzle.
4.2.23. Turn the welder ON
8” wire
spool
Summary of Contents for HIT140
Page 5: ...5 Assembly B FOR GASLESS WELDING ...
Page 6: ...6 C FOR GAS WELDING D FOR MMA WELDING ...
Page 21: ...21 ...
Page 22: ...22 ...