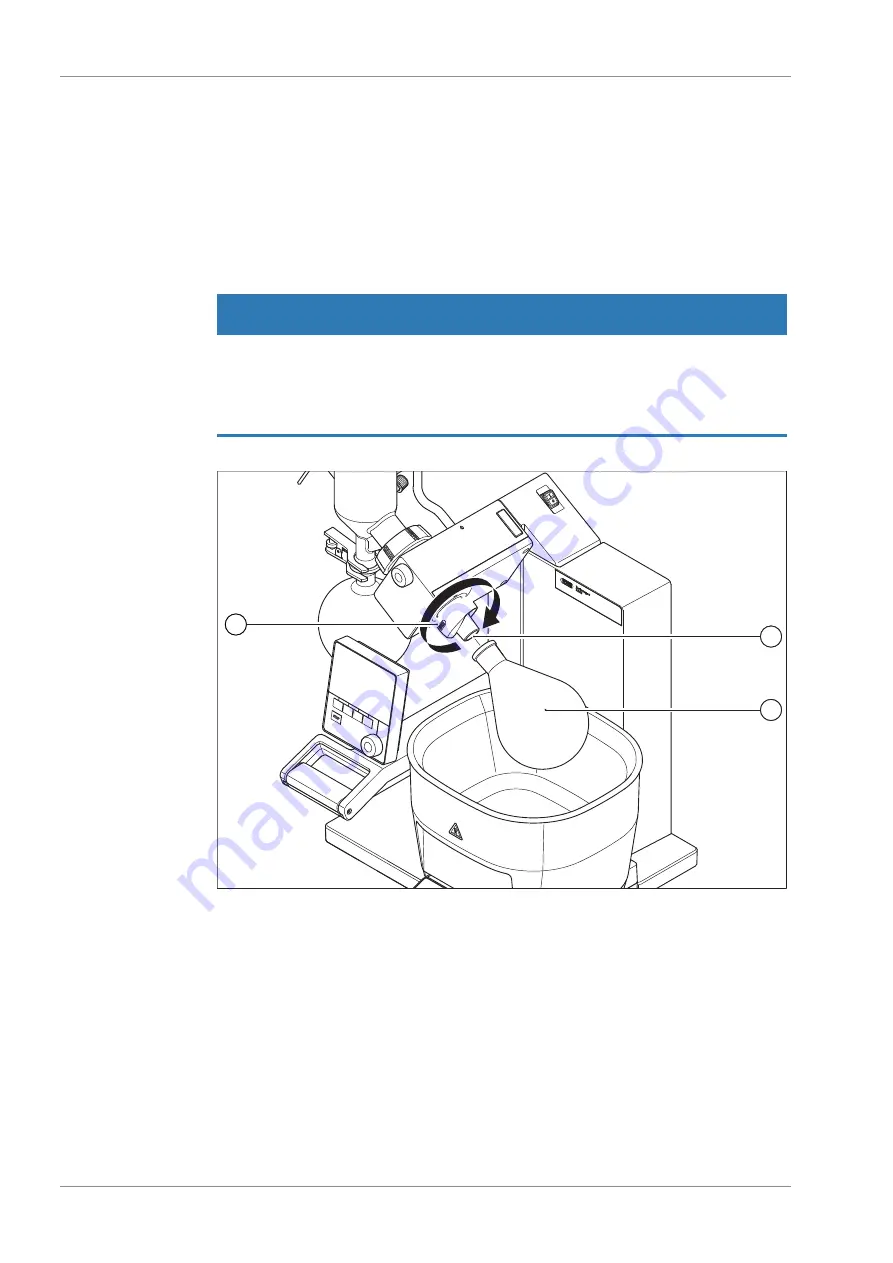
6 | Operation
BÜCHI Labortechnik AG
50/116
Operation Manual Rotavapor® R-300
u
Switch on the device at the master switch (5).
ð
The heating bath temperature (4) last set is displayed.
u
Set the maximum temperature (1), see Chapter 5.18 "Basic settings", page 47.
u
Set the desired temperature using the control knob (9).
ð
The current actual temperature (3) and the specified temperature (4) are
shown on the display.
u
Lock the set temperature, see Chapter 5.18 "Basic settings", page 47.
6.1.2
Fitting the evaporating flask
NOTICE
Risk of evaporating flask damage if fitted incorrectly
u
When fitting the evaporating flask make sure that the edge of the glass does not
strike the vapor duct.
u
Tighten combi-clip no more than hand-tight.
1
2
3
Fig. 30: Fitting the evaporating flask
1
Combi-clip
3
Evaporating flask
2
Vapor duct
u
Carefully fit evaporating flask (3) onto the vapor duct (2).
u
Screw combi-clip (1) clockwise until hand-tight.