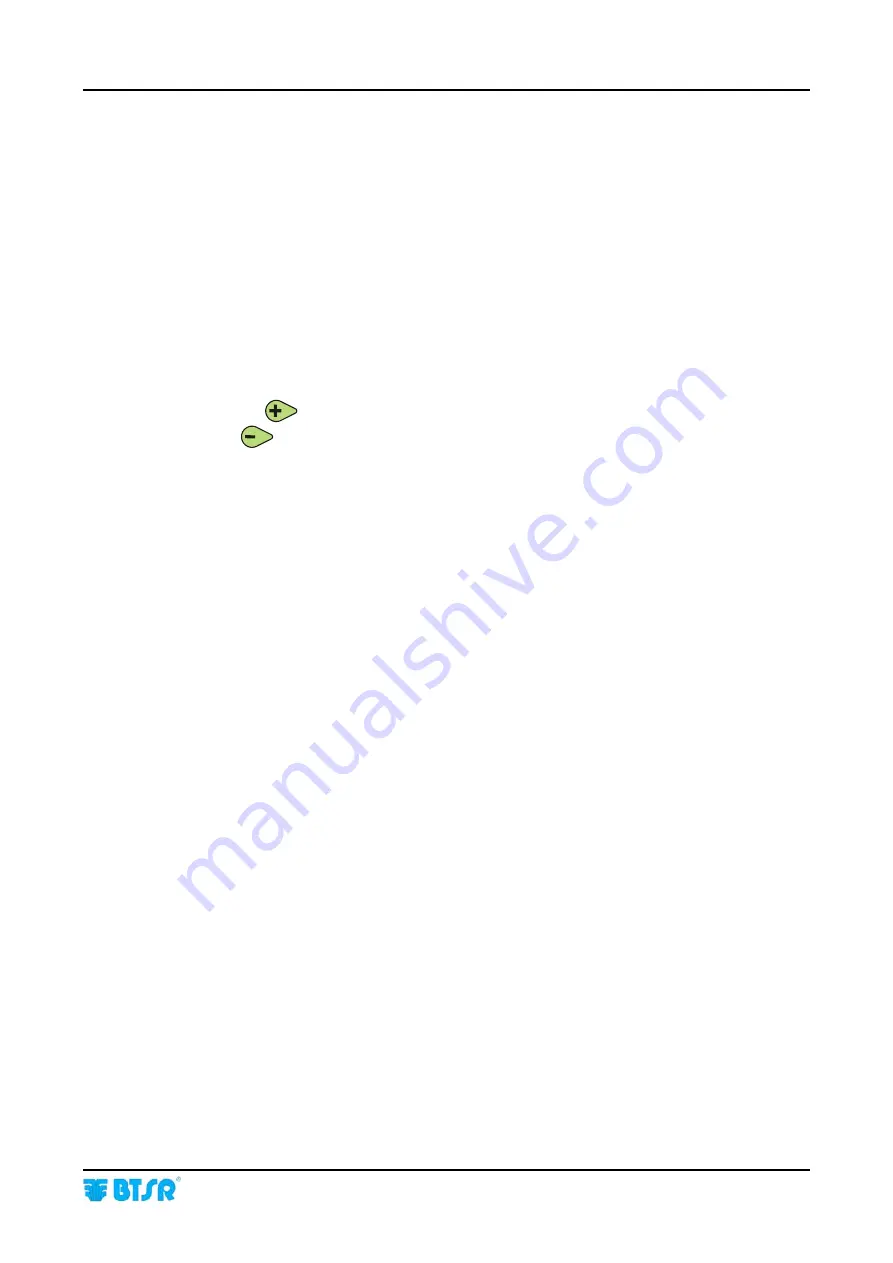
Operation
WINDINGFEEDER
- 3-7 -
Within the
P3 level
the following parameters can be programmed:
OFFSET AUTO
MOTOR CALIBRATION
ACCESS CODE
DEVICE IDENTIFICATION CODE
Within the
P4 level
the following parameter can be programmed:
MOTOR ROTATION DIRECTION
SENSOR TYPE
BAUDRATE
APPLICATION
(
REWIND
1/2
–
WARP
1/2)
YARN TYPE
(
ALL YARN OR ELASTIC
)
LANGUAGE SELECTION
USE OF INTELLIGENT TENSION CONTROL ACCESSORY
Press the
(Control)
button to switch from one programming level to the next one.
Press
(Reset)
button to quit the programming environment.
Summary of Contents for WINDINGFEEDER
Page 1: ...WINDINGFEEDER YARN CONTROL SYSTEM Operating Manual ENGLISH Rev 2 0 March 2011 ...
Page 4: ...Table of Contents ii WINDINGFEEDER Page intentionally left blank ...
Page 19: ...Technical Data and Installation WINDINGFEEDER 2 5 WINDINGFEEDER overall dimensions in mm ...
Page 22: ...Technical Data and Installation 2 8 WINDINGFEEDER Page intentionally left blank ...
Page 42: ...Operation 3 20 WINDINGFEEDER Page intentionally left blank ...