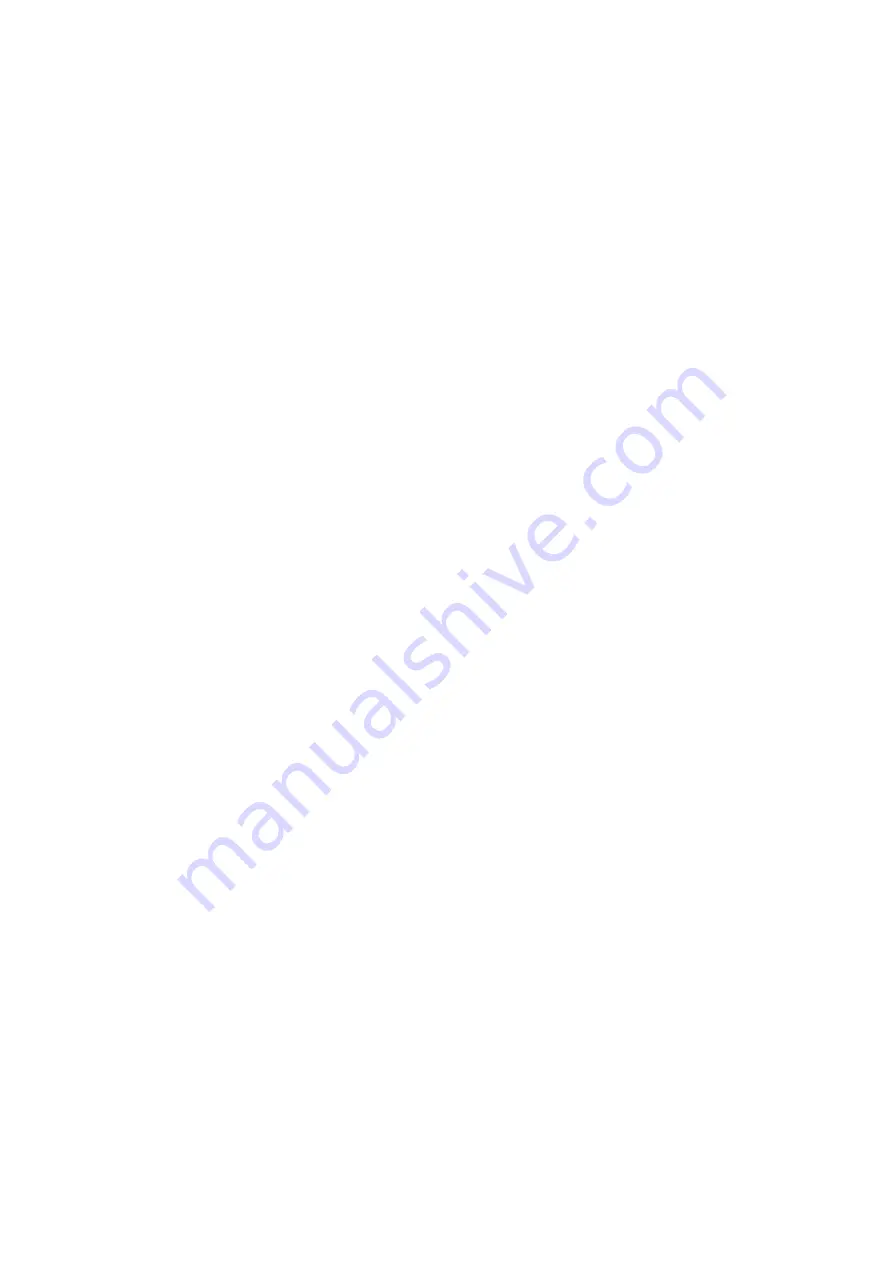
Rear Chain
The rear chain is adjusted by means of draw bolts at the fork ends at the back of
the wheel spindle. First slacken off the brake adjuster, as the brake rod may prevent
free movement of the wheel. Next, loosen the nut on the inside of the brake plate arm
at
C
, to allow the slotted arm to accommodate itself to a new position when the wheel
is moved. It is not necessary to disturb the speedometer drive unit. Slacken off the
spindle nuts
A
(Fig. 8) and tighten the adjusting nuts
B
until the chain tension is
correct.
The chain should be adjusted with the machine on its stand, i.e., with the rear
wheel in its lowest position in the rear suspension. The adjustment is correct when
the total up and down movement in the centre of the chain run at its tightest point is
¾ in.
Make sure that the adjusters are firmly against the fork ends when checking, and
also that the adjustment is equal on both sides of the wheel so that the latter is in
correct alignment in the frame. This can be done either by glancing along the line of
both wheels when the front wheel is set straight, or by means of a long straight-edge
or the edge of a plank placed along the sides of the wheels. The straight-edge should
touch the wall of each tyre in two places.
After adjusting, do not forget to retighten nuts
A
and
C
.
Brakes
The brakes should be adjusted whenever the handlever or foot pedal movement has
become excessive. The shoes should be just clear of the drum when the brake is off,
but close enough for immediate contact when the brake is applied. The brakes must
not be adjusted so closely however, that they are continually in contact with the
drum, otherwise excessive heat may be generated resulting in deterioration of braking
efficiency.
In the case of the rear brake a sleeve nut on the brake rod effects any adjustment
necessary, and a few turns are all that are required to improve braking efficiency.
The front brake is adjusted by means of the knurled ring nut on the cable stop at the
lower end of the forks.
STEERING AND SUSPENSION
Under normal conditions the only servicing which the front forks require is
occasional renewal of the oil. The need for this may be indicated by excessive
movement of the forks, but it should only be necessary after considerable mileage.
Prise out the cap on the top of the fork leg by means of the small hole provided for
the purpose, and with the aid of a tubular spanner unscrew the small nut thus
exposed. Then remove the large nut which carried the cap. Disconnect the
mudguard stay at the lower end of the fork leg, and unscrew the stud. Allow all the
oil to drain out, then apply the front brake and depress the forks a few times to drive
out any oil remaining in the system. Replace the drain stud and fibre washer.
pint of an S.A.E. 20 oil to each leg (see lubrication list, page 22) and
The procedure for draining and re-filling the forks is as above except that the filler
is a single cap nut on top of the fork leg and a drain screw is provided at the bottom
of the fork sliding member, near to the wheel spindle.