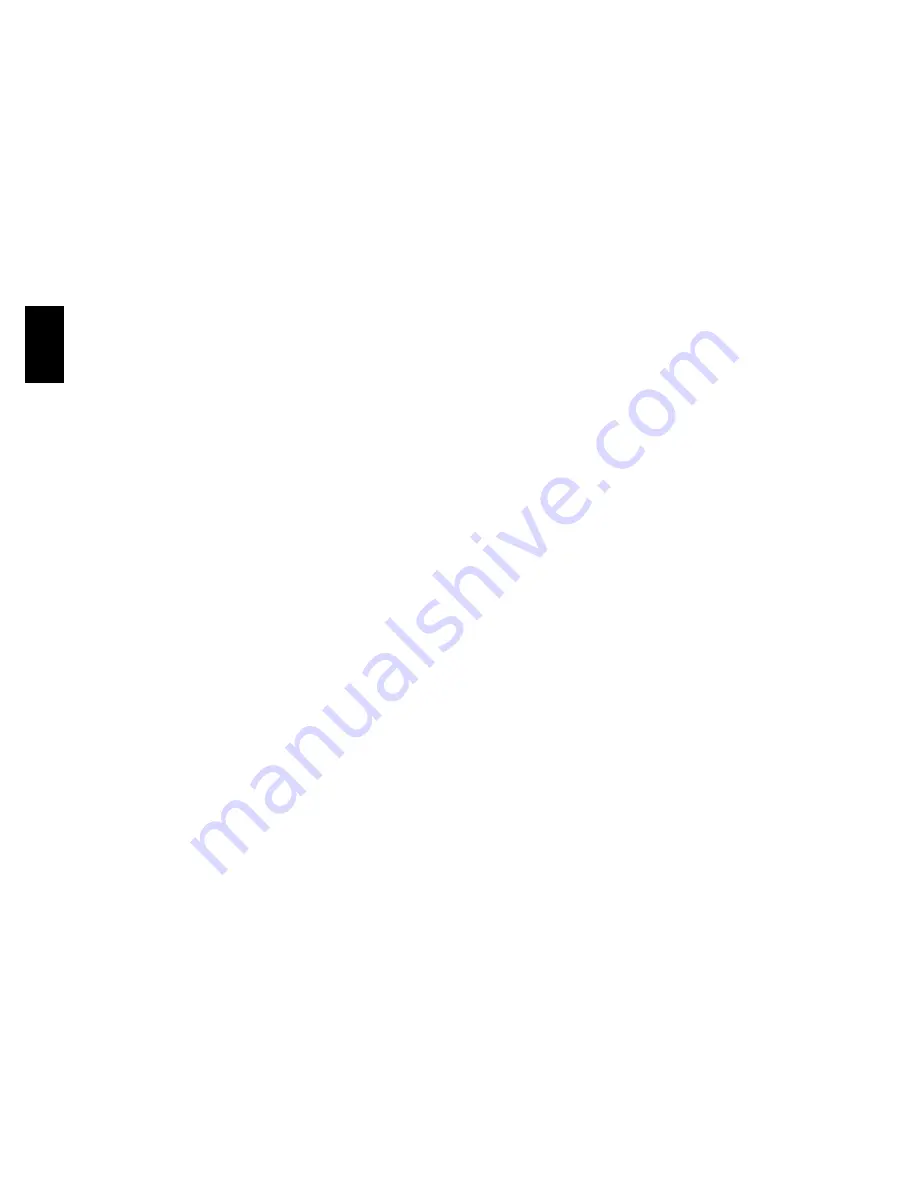
48
DAMPER MOVEMENT —
Damper movement from full open to
full closed (or vice versa) takes 2 1/2 minutes.
THERMOSTATS —
The Economizer control works with conven-
tional thermostats that have a Y1 (cool stage 1), Y2 (cool stage 2), W1
(heat stage 1), W2 (heat stage 2), and G (fan). The Economizer control
does not support space temperature sensors. Connections are made at
the thermostat terminal connection board located in the main control
box.
OCCUPANCY CONTROL —
The factory default configuration
for the Economizer control is occupied mode. Occupied status is
provided by the black jumper from terminal TR to terminal N. When
unoccupied mode is desired, install a field supplied time clock
function in place of the jumper between TR and N. See Fig. 44. When
the time clock contacts are closed, the Economizer control will be in
occupied mode. When the time clock contacts are open (removing the
24--v signal from terminal N), the Economizer will be in unoccupied
mode.
DEMAND CONTROLLED VENTILATION (DCV)—
When
using the Economizer for demand controlled ventilation, there are
some equipment selection criteria which should be considered. When
selecting the heat capacity and cool capacity of the equipment, the
maximum ventilation rate must be evaluated for design conditions.
The maximum damper position must be calculated to provide the
desired fresh air. Typically the maximum ventilation rate will be about
5 to 10% more than the typical CFM required per person, using
normal outside air design criteria. An exponential anticipatory
strategy should be taken with the following conditions: a zone with
a large area, varied occupancy, and equipment that cannot exceed the
required ventilation rate at design conditions. Exceeding the required
ventilation rate means the equipment can condition air at a maximum
ventilation rate that is greater than the required ventilation rate for
maximum occupancy. An exponential--anticipatory strategy will
cause the fresh air supplied to increase as the room CO
2
level increases
even though the CO
2
set point has not been reached. By the time the
CO
2
level reaches the set point, the damper will be at maximum
ventilation and should maintain the set point. In order to have the CO
2
sensor control the economizer damper in this manner, first determine
the damper voltage output for minimum or base ventilation. Base
ventilation is the ventilation required to remove contaminants during
unoccupied periods. The following equation may be used to
determine the percent of outside--air entering the building for a given
damper position. For best results there should be at least a 10
_
F
(12.2
_
C) difference in outside and return--air temperatures.
(T
o
x OA/100) + (T
R
x RA/100) = T
M
T
O
= Outdoor--Air Temperature
OA = Percent of Outdoor Air
T
R
= Return--Air Temperature
RA = Percent of Return Air
T
M
= Mixed--Air Temperature
Once base ventilation has been determined, set the minimum damper
position potentiometer to the correct position. The same equation can
be used to determine the occupied or maximum ventilation rate to the
building. For example, an output of 3.6 volts to the actuator provides
a base ventilation rate of 5% and an output of 6.7 volts provides the
maximum ventilation rate of 20% (or base plus 15 CFM per person).
Use Fig. 42 to determine the maximum setting of the CO
2
sensor. For
example, a 1100 ppm set point relates to a 15 CFM per person design.
Use the 1100 ppm curve on
Fig. 42 t
o find the point when the CO
2
sensor output will be 6.7 volts. Line up the point on the graph with
the left side of the chart to determine that the range configuration for
the CO
2
sensor should be 1800 ppm. The Economizer controller will
output the 6.7 volts from the CO
2
sensor to the actuator when the CO
2
concentration in the space is at 1100 ppm.
The DCV set point may be left at 2 volts since the CO
2
sensor
voltage will be ignored by the Economizer controller until it rises
above the 3.6 volt setting of the minimum position potentiometer.
Once the fully occupied damper position has been determined, set
the maximum damper demand control ventilation potentiometer to
this position. Do not set to the maximum position as this can result
in over ventilation to the space and potential high--humidity levels.
CO
2
SENSOR CONFIGURATION —
The CO
2
sensor has preset
standard voltage settings that can be selected anytime after the sensor
is powered up. Use setting 1 or 2 for equipment. See Table 16.
1. Press Clear and Mode buttons. Hold at least 5 seconds until
the sensor enters the Edit mode.
2. Press Mode twice. The STDSET Menu will appear.
3. Use the Up/Down button to select the preset number. See
Table 16.
4. Press Enter to lock in the selection.
5. Press Mode to exit and resume normal operation.
The custom settings of the CO
2
sensor can be changed anytime
after the sensor is energized. Follow the steps below to change the
nonstandard settings:
1. Press Clear and Mode buttons. Hold at least 5 seconds until
the sensor enters the Edit mode.
2. Press Mode twice. The STDSET Menu will appear.
3. Use the Up/Down button to toggle to the NONSTD menu
and press Enter.
4. Use the Up/Down button to toggle through each of the nine
variables, starting with Altitude, until the desired setting is
reached.
5. Press Mode to move through the variables.
6. Press Enter to lock in the selection, then press Mode to
continue to the next variable.
DEHUMIDIFICATION OF FRESH AIR WITH DCV
CONTROL—
Information from ASHRAE indicates that the largest
humidity load on any zone is the fresh air introduced. For some
applications, an energy recovery unit can be added to reduce the
moisture content of the fresh air being brought into the building when
the enthalpy is high. In most cases, the normal heating and cooling
processes are more than adequate to remove the humidity loads for
most commercial applications.
If normal rooftop heating and cooling operation is not adequate for
the outdoor humidity level, an energy recovery unit and/or a
dehumidification option should be considered.
604D
--
--
A
Summary of Contents for LEGACY 604D-A
Page 4: ...4 A09471 Fig 2 604D A24 36 Unit Dimensions 604D A ...
Page 5: ...5 A09472 Fig 3 604D A42 60 Unit Dimensions 604D A ...
Page 12: ...12 A10197 Fig 11 Connection Wiring Schematics 208 230 1 60 604D A ...
Page 13: ...13 A10197 Fig 11 Cont Ladder Wiring Schematics 208 230 1 60 604D A ...
Page 14: ...14 A10194 Fig 12 Connection Wiring Schematics 208 230 3 60 604D A ...
Page 15: ...15 A10194 Fig 12 Cont Ladder Wiring Schematics 208 230 3 60 604D A ...
Page 16: ...16 A10195 Fig 13 Connection Wiring Diagram 460 3 60 604D A ...
Page 17: ...17 A10195 Fig 13 Cont Ladder Wiring Diagram 460 3 60 604D A ...
Page 25: ...25 A09070 Fig 17 Cooling Charging Table Subcooling 604D A ...
Page 43: ...43 A10059 Fig 44 Economizer Wiring Diagram 604D A ...
Page 45: ...45 A10200 Fig 45 Cont Ladder Wiring Diagram 230 3 604D A ...
Page 46: ...46 A10199 Fig 46 Connection Wiring Diagram 460 3 604D A ...
Page 47: ...47 A10199 Fig 46 Cont Ladder Wiring Diagram 460 3 604D A ...