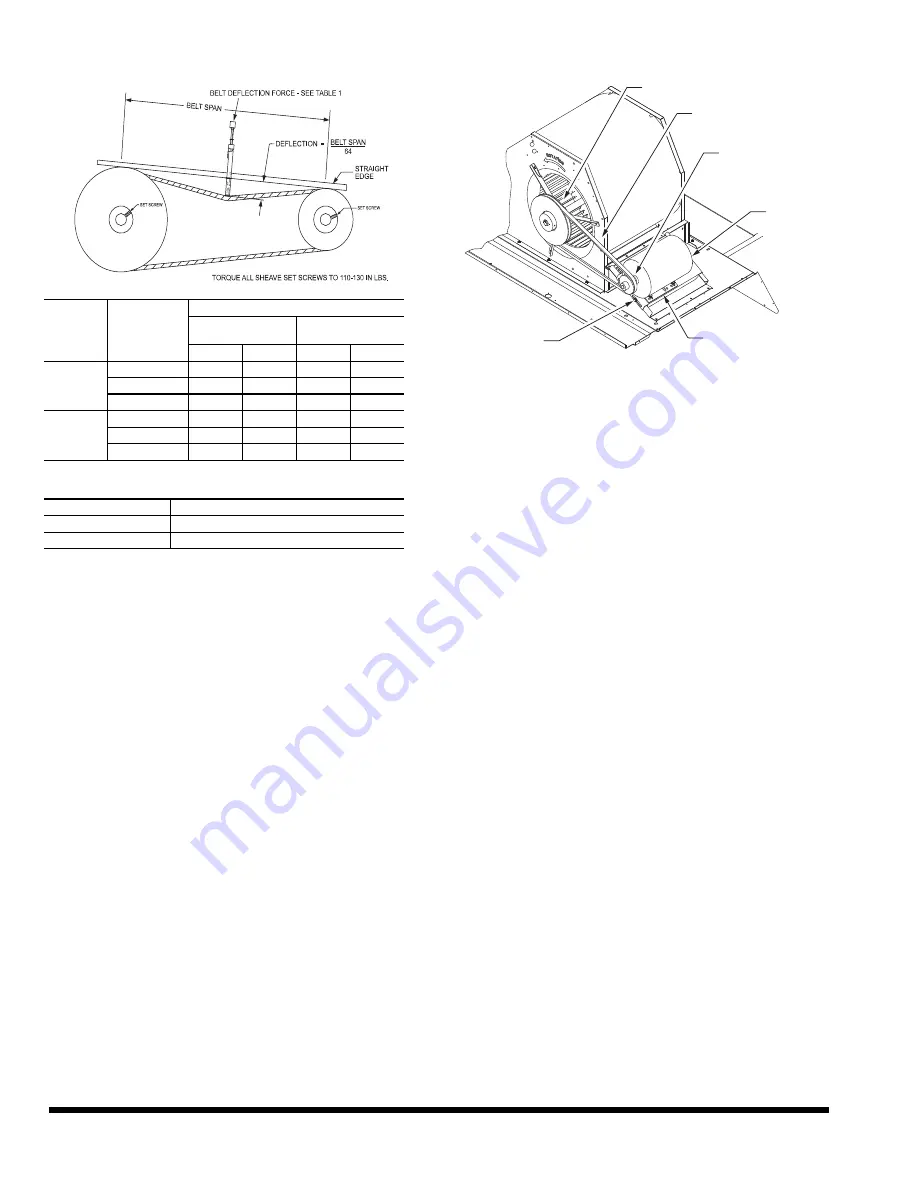
Manufacturer reserves the right to change, at any time, specifications and designs without notice and without obligations.
Replaces: II580J-17-30-V-02
Copyright 2018 Bryant Heating & Cooling Systems
Edition Date: 4/18
Printed in U.S.A
Catalog No: II580J–17-30-V–03
Fig. 65 — V-Belt Force Label
Fig. 66 — Belt Drive Motor Mounting
Pre-Start and Start-Up —
This completes the mechanical in-
stallation of the unit. Refer to the unit’s Service Manual for detailed
Pre-Start and Start-Up instructions. Download the latest versions
from HVAC Partners (www.hvacpartners.com).
Table 1
Table 2
BELT
CROSS
SECTION
SMALLEST
SHEAVE
DIAMETER
BELT DEFLECTION FORCE (LBS)
UNNOTCHED
BELTS
NOTCHED BELTS
USED
NEW
USED
NEW
A, AX
3.0-3.6
3.7
5.5
4.1
6.1
3.8-4.8
4.5
6.8
5.0
7.4
5.0-7.0
5.4
8.0
5.7
8.4
B, BX
3.4-4.2
—
—
4.9
7.2
4.4-5.6
5.3
7.9
7.1
10.5
5.8-8.6
6.3
9.4
8.5
12.6
BELT CONDITION
TENSION FORCE IN BELT (LBS)
New
100
Used
80
BLOWER PULLEY
V-BELT
MOTOR
PULLEY
MOTOR
MOTOR MOUNTING
PLATE
MOUNTING
BOLTS (4)
Summary of Contents for LEGACY 580J*20M Series
Page 4: ...4 Fig 2 Unit Dimensional Drawing 17 and 20 Size Unit...
Page 5: ...5 Fig 2 Unit Dimensional Drawing 17 and 20 Size Unit cont...
Page 6: ...6 Fig 3 Unit Dimensional Drawing 24 and 28 Size Unit...
Page 7: ...7 Fig 3 Unit Dimensional Drawing 24 and 28 Size Unit cont...
Page 8: ...8 Fig 4 Unit Dimensional Drawing 30 Size Unit...
Page 9: ...9 Fig 4 Unit Dimensional Drawing 30 Size Unit cont...
Page 13: ...13 Fig 8 Roof Curb Details 17 and 20 Size Units 17 20...
Page 14: ...14 Fig 9 Roof Curb Details 24 and 28 Size Units 24 28...
Page 15: ...15 Fig 10 Roof Curb Details 30 Size Units 30...
Page 25: ...25 Fig 33 Typical Perfect Humidity Adaptive Dehumidification System Humidistat Wiring...
Page 40: ...40 Fig 41 Typical RTU Open System Control Wiring Diagram...
Page 41: ...41 Fig 42 Typical RTU Open System Control Wiring Diagram with Perfect Humidity System...