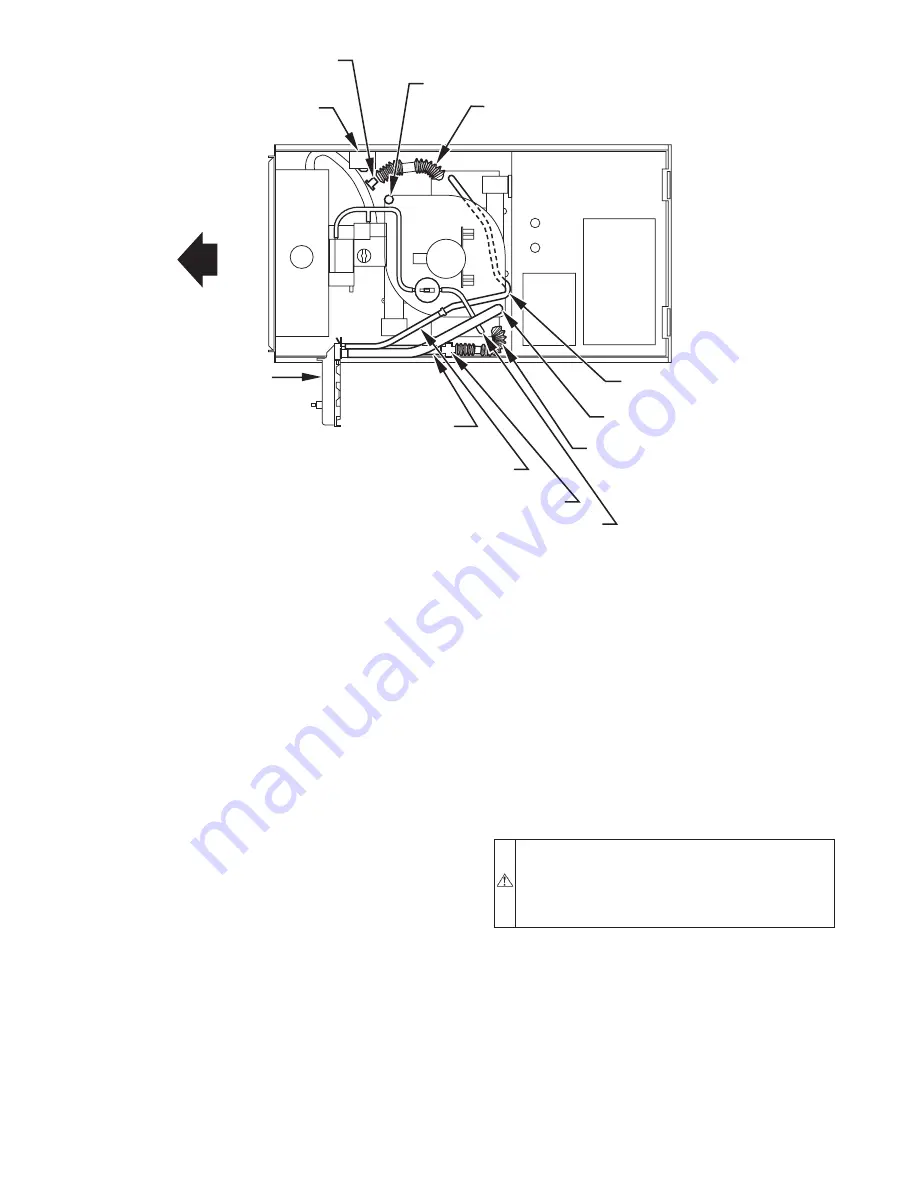
c. Determine appropriate length, cut, and connect tube.
d. Clamp tube to prevent any condensate leakage.
3. Relief Port Tube
a. Extend collector box tube (green label) which was
previously connected to the condensate trap by splicing
to small diameter tube (factory-supplied in loose parts
bag).
b. Route extended collector box pressure tube to relief port
connection on the condensate trap.
c. Determine appropriate length, cut, and connect tube.
d. Clamp tube to prevent any condensate leakage.
C.
Condensate Trap Field Drain Attachments
Refer to Condensate Drain section for recommendations and
procedures.
D.
Pressure Switch Tubing
The LOWER collector box pressure tube (pink label) is factory
connected to the pressure switch for use when furnace is installed
in UPFLOW applications. This tube MUST be disconnected,
extended, rerouted, and then reconnected to the pressure switch in
HORIZONTAL LEFT applications.
NOTE:
See Fig. 10 or tube routing label on main furnace door to
check for proper connections.
Modify tube as described below.
1. Disconnect collector box pressure tube (pink label) attached
to pressure switch.
2. Use smaller diameter tube (factory-supplied in loose parts
bag) to extend tube disconnected in item 1.
3. Route extended tube:
a. Behind inducer housing.
b. Between blower shelf and inducer housing.
c. Behind inducer motor bracket.
d. Between inducer motor and pressure switch.
4. Determine appropriate length, cut, and reconnect tube to
pressure switch connection labeled COLLECTOR BOX.
E.
Condensate Trap Freeze Protection
Refer to Condensate Drain Protection section for recommenda-
tions and procedures.
F.
Construct a Working Platform
Construct working platform where all required furnace clearances
are met. (See Fig. 3 and 11.)
CAUTION:
The condensate trap MUST be installed
below furnace. See Fig. 5 for dimensions. The drain
connection to condensate trap must also be properly
sloped to an open drain. Failure to follow this caution will
result in intermittent unit operation.
NOTE:
Combustion-air and vent pipes are restricted to a mini-
mum length of 5 ft. (See Table 7.)
NOTE:
A 12-in. minimum offset pipe section is recommended
with short (5 to 8 ft) vent systems. This recommendation is to
reduce excessive condensate droplets from exiting the vent pipe.
(See Fig. 11 or 34.)
V.
HORIZONTAL RIGHT (SUPPLY-AIR DISCHARGE)
APPLICATIONS
A horizontal right furnace application is where furnace blower is
located to the left of combustion and controls section of furnace,
and conditioned air is discharged to the right.
Fig. 10—Horizontal Left Tube Configuration
A00215
CONDENSATE
TRAP
AUXILIARY
"
J
"
BOX
PLUG
CAP
INDUCER HOUSING
DRAIN TUBE (VIOLET)
COLLECTOR BOX
DRAIN TUBE (BLUE)
COLLECTOR BOX TUBE (PINK)
RELOCATE TUBE BETWEEN BLOWER SHELF AND INDUCER HOUSING FOR
040, 060, AND 080 HEATING INPUT FURNACES
COLLECTOR BOX
EXTENSION TUBE
COLLECTOR BOX
DRAIN TUBE
(BLUE AND WHITE STRIPED)
DRAIN TUBE COUPLING
COLLECTOR BOX
TUBE (GREEN)
COLLECTOR
BOX EXTENSION
DRAIN TUBE
—10—
→
Summary of Contents for CONDENSING GAS FURNACE 350MAV
Page 50: ... 50 ...
Page 51: ... 51 ...