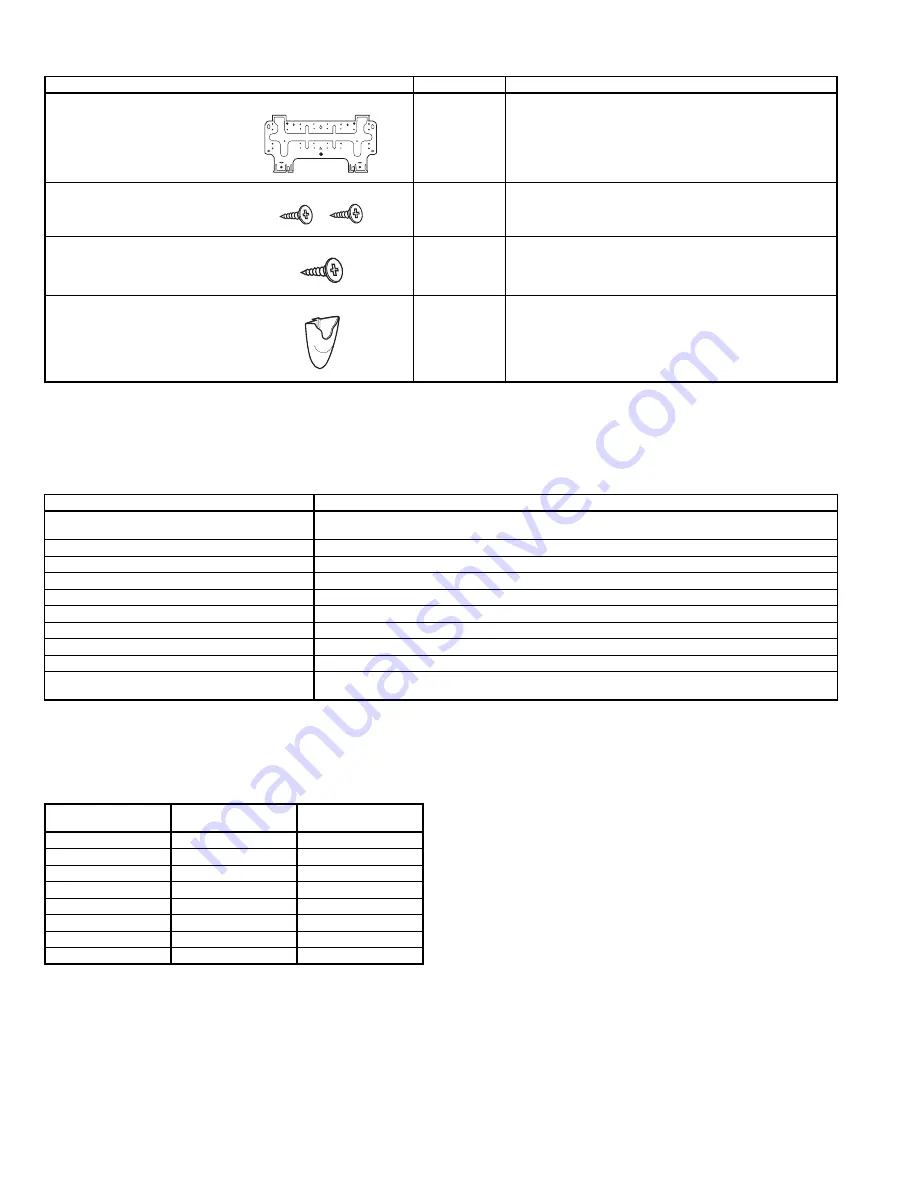
—2—
Table 1A — Installation Materials — Included In Shipment
*619ENF01824, 619ENQ018,024: 5
619ENF,ENQ030,036: 14
Table 1B — Installation Materials — Field-Supplied
LEGEND
Table 2 — Matching Indoor Units to Outdoor Units
See Fig. 2 for unit dimensions. Allow sufficient space for air-
flow clearance, wiring, refrigerant piping, and servicing
units. See Fig. 3.
Avoid mounting the unit in areas that are:
• exposed to direct sunlight
• too close to heat sources
• too close to humid conditions
• located in an area with oily ambient conditions.
DESCRIPTION
QTY
USAGE
Wall Hanging Bracket
1
For indoor unit installation.
Screws, 4xL10
2
For affixing unit and hanging bracket.
Screws, 5xL25
5/14*
For wall hanging bracket installation.
For wireless remote control mounting bracket installation.
Wireless Remote Control
Mounting Bracket
1
For wireless remote control installation.
NAME
SPECIFICATIONS
Connection Pipe (nominal capacity)
Liquid line:
3
/
8
in. (619ENF,ENQ018-036)
Mixed Phase line:
5
/
8
in. (619ENF01824 and 619ENQ018,024),
3
/
4
in. (619ENF,ENQ030,036)
Wall Sleeve
—
Wall Cap
—
Finishing Tape
PVC Film
Fastening Tape
—
Pipe Insulation
—
Drain Hose
5
/
8
in. (619ENF01824 and 619ENQ018,024)
3
/
4
in. (619ENF,ENQ030,036)
Sealer Putty
—
Power Supply Cable
AWG 14 or higher
Electrical Connecting Cable Between
Indoor and Outdoor Unit
Cable Type: AWG 14 synthetic rubber insulation with Neoprene coating, according to NEC codes.
AWG —
American Wire Gage
NEC —
National Electrical Code
OUTDOOR UNIT
COOLING ONLY OR
HEAT PUMP
INDOOR UNIT
538ENF018
Cooling Only
619ENF01824
538ENF024
Cooling Only
619ENF01824
538ENF030
Cooling Only
619ENF030
538ENF036
Cooling Only
619ENF036
538QNF018
Heat Pump
619ENQ018
538QNF024
Heat Pump
619ENQ024
538QNF030
Heat Pump
619ENQ030
538QNF036
Heat Pump
619ENQ036
Summary of Contents for 619ENF
Page 9: ... 9 Fig 16 619ENF01824 Matched with 538ENF Typical Wiring Schematic ...
Page 10: ... 10 Fig 17 619ENQ018 024 Matched with 538QNF Typical Wiring Schematic ...
Page 11: ... 11 Fig 18 619ENF030 036 Matched with 538ENF Typical Wiring Schematic ...
Page 12: ... 12 Fig 19 619ENQ030 036 Matched with 538QNF Typical Wiring Schematic ...
Page 16: ...Copyright 2006 Bryant Heating Cooling Systems Printed in U S A CATALOG NO 02 619E0001 SI ...