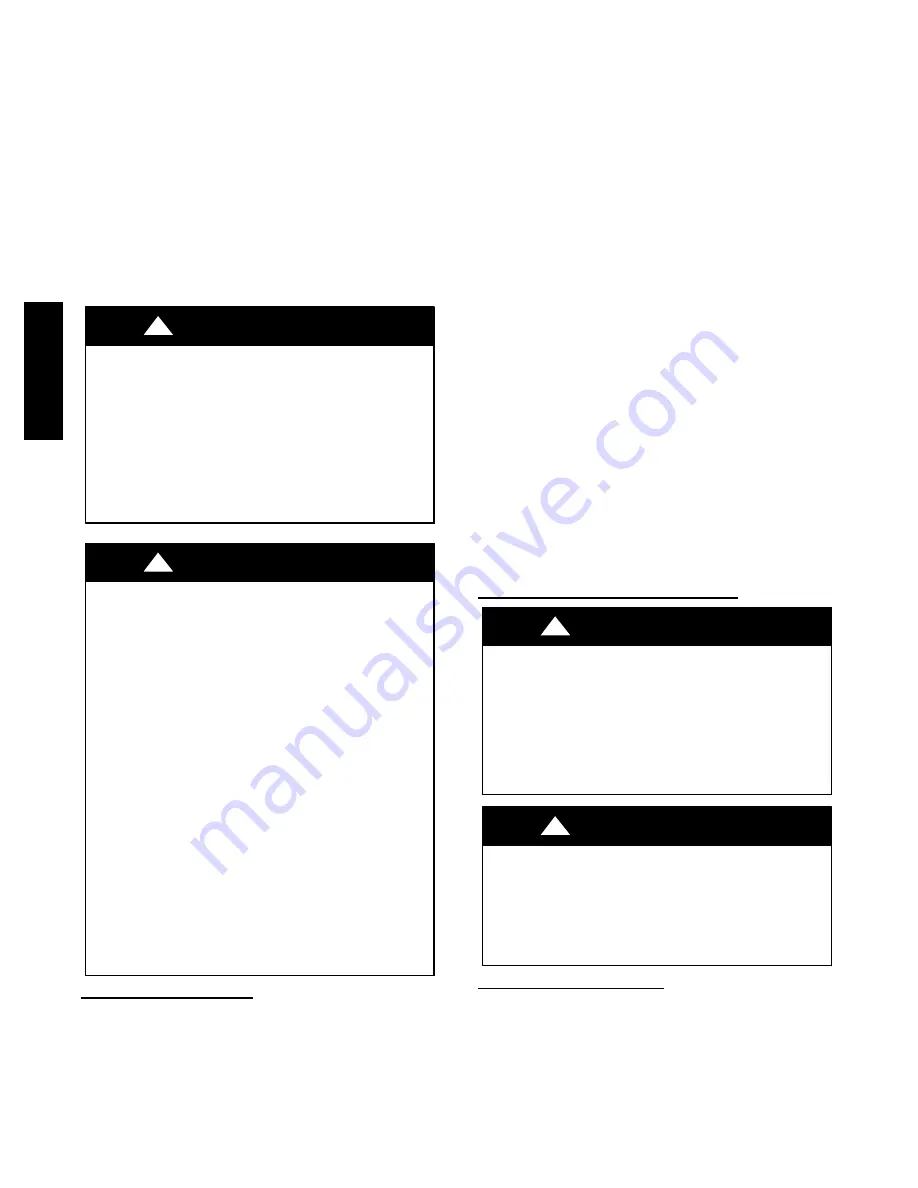
14
5. Size all ductwork for maximum required airflow (either
heating or cooling) for unit being installed. Avoid abrupt
duct size increases or decreases or performance may be
affected.
6. Adequately insulate and weatherproof all ductwork located
outdoors. Insulate ducts passing through unconditioned
space, and use vapor barrier in accordance with latest issue
of Sheet Metal and Air Conditioning Contractors National
Association (SMACNA) and Air Conditioning Contractors
of America (ACCA) minimum installation standards for
heating and air conditioning systems. Secure all ducts to
building structure.
7. Flash, weatherproof, and vibration isolate all openings in
building structure in accordance with local codes and good
building practices.
Step 10 — Install Electrical Connections
ELECTRICAL SHOCK HAZARD
Failure to follow this warning could result in personal
injury or death.
The unit cabinet must have an uninterrupted, unbroken
electrical ground. This ground may consist of an electrical
wire connected to the unit ground screw in the control
compartment, or conduit approved for electrical ground
when installed in accordance with NFPA 70 (NEC) (latest
edition) (in Canada, Canadian Electrical Code CSA C22.1)
and local electrical codes.
!
WARNING
UNIT COMPONENT DAMAGE HAZARD
Failure to follow this caution may result in damage to the
unit being installed.
1. Make all electrical connections in accordance with NFPA
70 (NEC) (latest edition) and local electrical codes
governing such wiring. In Canada, all electrical
connections must be in accordance with CSA standard
C22.1 Canadian Electrical Code Part 1 and applicable
local codes. Refer to unit wiring diagram.
2. Use only copper conductor for connections between
field--supplied electrical disconnect switch and unit. DO
NOT USE ALUMINUM WIRE.
3. Be sure that high--voltage power to unit is within
operating voltage range indicated on unit rating plate. On
3--phase units, ensure phases are balanced within 2
percent. Consult local power company for correction of
improper voltage and/or phase imbalance.
4. Insulate low--voltage wires for highest voltage contained
within conduit when low--voltage control wires are in
same conduit as high--voltage wires.
5. Do not damage internal components when drilling
through any panel to mount electrical hardware, conduit,
etc.
!
CAUTION
High--Voltage Connections
When routing power leads into unit, use only copper wire between
disconnect and unit. The high voltage leads should be in a conduit
until they enter the duct panel; conduit termination at the duct
panel must be watertight.
The unit must have a separate electrical service with a
field--supplied, waterproof disconnect switch mounted at, or within
sight from, the unit. Refer to the unit rating plate, NEC and local
codes for maximum fuse/circuit breaker size and minimum circuit
amps (ampacity) for wire sizing.
The field--supplied disconnect switch box may be mounted on the
unit over the high--voltage inlet hole when the standard power and
low--voltage entry points are used (See Fig. 3 and 4 for acceptable
location).
NOTE
:
Field supplied disconnect switch box should be
positioned so that it does not cover up any of the unit gas
combustion supply air louvers.
See unit wiring label (Fig. 16, 17 and 18) and Fig. 11 for reference
when making high voltage connections. Proceed as follows to
complete the high--voltage connections to the unit.
Single phase units:
1. Run the high--voltage (L1, L2) and ground lead into the
control box.
2. Connect ground lead to chassis ground connection.
3. Locate the black and yellow wires connected to the line side
of the contactor (if equipped).
4. Connect field L1 to black wire from connection 11 of the
compressor contactor.
5. Connect field wire L2 to yellow wire from connection 23 of
the compressor contactor.
Three--phase units:
1. Run the high--voltage (L1, L2, L3) and ground lead into the
control box.
2. Connect ground lead to chassis ground connection.
3. Locate the black and yellow wires connected to the line side
of the contactor (if equipped).
4. Connect field L1 to black wire from connection 11 of the
compressor contactor.
5. Connect field wire L3 to yellow wire from connection 13 of
the compressor contactor.
6. Connect field wire L2 to blue wire from compressor.
Special Procedures for 208--v Operation
ELECTRICAL SHOCK HAZARD
Failure to follow this warning could result in personal
injury or death.
Make sure the power supply to the unit is switched OFF and
install lockout tag. before making any wiring changes. With
disconnect switch open, move black wire from transformer
(3/16 in. [4.8 mm]) terminal marked 230 to terminal marked
208. This retaps transformer to primary voltage of 208 vac.
!
WARNING
ELECTRICAL SHOCK FIRE/EXPLOSION HAZARD
Failure to follow this warning could result in personal
injury or death and property damage.
Before making any wiring changes,
make sure
the gas
supply is switched off first.
Then
switch off the power
supply to the unit and install lockout tag.
!
WARNING
Control Voltage Connections
Do not use any type of power--stealing thermostat. Unit control
problems may result.
Use no. 18 American Wire Gage (AWG) color--coded, insulated
(35
_
C minimum) wires to make the control voltage connections
between the thermostat and the unit. If the thermostat is located
more than 100 ft (30.5 m) from the unit (as measured along the
control voltage wires), use no. 16 AWG color--coded, insulated
(35
_
C minimum) wires.
577E
Summary of Contents for 577E-A
Page 5: ...5 A190127 Fig 3 577E Unit Dimensions 577E ...
Page 6: ...6 A190128 Fig 4 577E 36 60 Unit Dimensions 577E ...
Page 7: ...7 A150039 Fig 5 577E B36 60 Unit Dimensions 577E ...
Page 21: ...21 A14593 Fig 16 208 230 1 60 Connection Wiring Diagram 577E ...
Page 22: ...22 A14594 Fig 17 Cont 208 230 1 60 Ladder Wiring Diagram 577E ...
Page 23: ...23 A14615 Fig 17 208 230 3 60 Connection Wiring Diagram Gas Inputs 40 60 90 KBtu hr 577E ...
Page 24: ...24 A14616 Fig 18 Cont 208 230 3 60 Ladder Wiring Diagram Gas Inputs 40 60 90 KBtu hr 577E ...
Page 25: ...25 A14618 Fig 18 208 230 3 60 Connection Wiring Diagram Gas Inputs 115 130 577E ...
Page 26: ...26 A14617 Fig 19 Cont 208 230 3 60 Ladder Wiring Diagram Gas Inputs 115 130 577E ...
Page 27: ...27 A13026 Fig 19 460 3 60 Connection Wiring Diagram 577E ...
Page 28: ...28 A13027 Fig 20 Cont 460 3 60 Ladder Wiring Diagram 577E ...