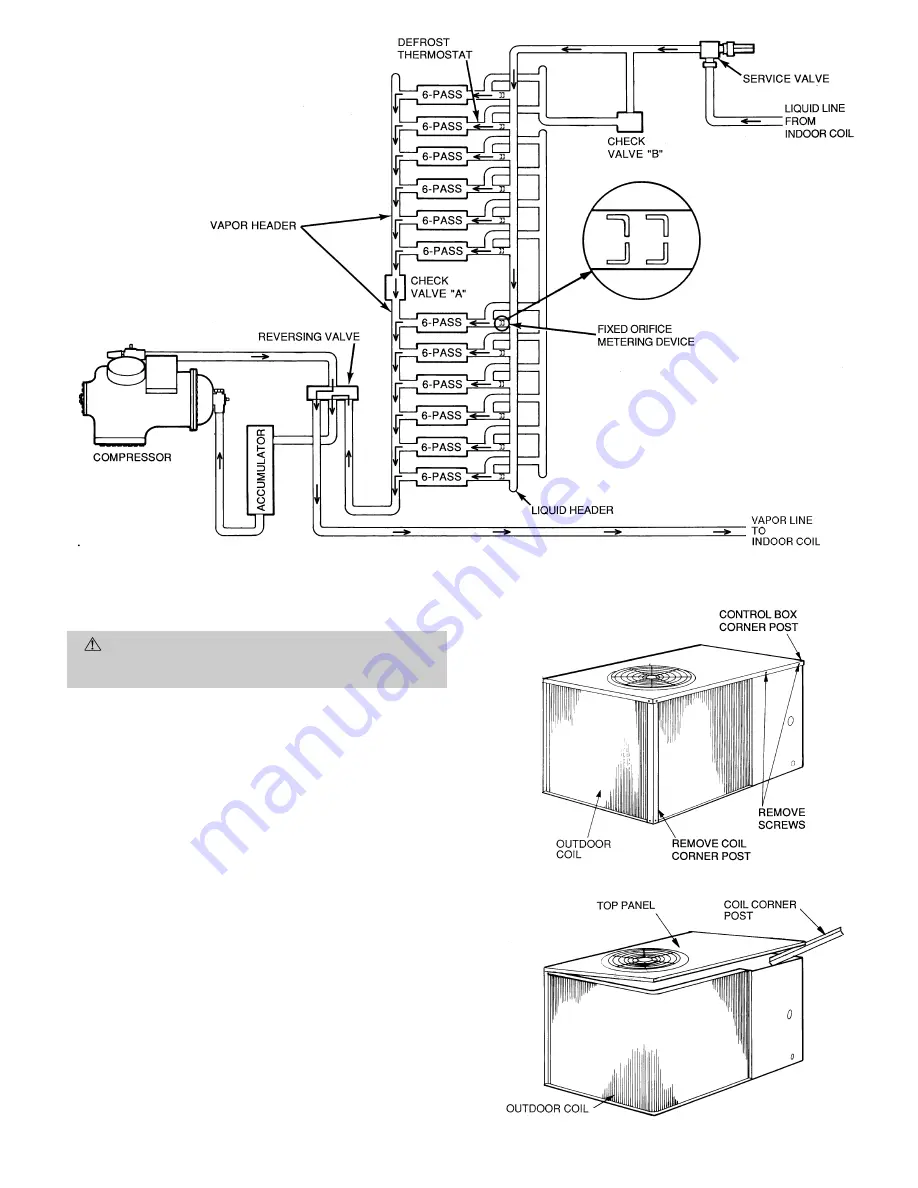
SERVICE
CAUTION:
When servicing unit, shut off all electri-
cal power to unit to avoid shock hazard or injury from
rotating parts.
I. CLEANING
Inspect unit interior at the beginning of each cooling season
and as operating conditions require.
A. Outdoor Coil
Inspect coil monthly. Clean outdoor coil annually and as re-
quired by location or outdoor-air conditions.
Clean coil as follows:
1. Turn off unit power.
2. Remove and save top panel screws on outdoor unit.
3. Remove outdoor coil corner post. See Fig. 14. To hold
top panel open, place coil corner post between top panel
and side panel. See Fig. 15.
4. Remove bracket holding coil sections together at return
end of outdoor coil. Carefully separate the outer coil sec-
tion 3 to 4 in. from the inner coil section. See Fig. 16.
5. Use a water hose or other suitable equipment to flush
down between the 2 coil sections to remove dirt and de-
bris. Clean the outer surfaces with a stiff brush in the
normal manner.
6. Reposition the outer coil section and secure the sections
together. Remove the coil corner post from between the
top panel and side panel. Install the coil corner post and
replace all screws removed in Step 2.
Fig. 13 — Heating Mode Operation
Fig. 14 — Cleaning Outdoor Coil
Fig. 15 — Propping Up Top Panel
—11—