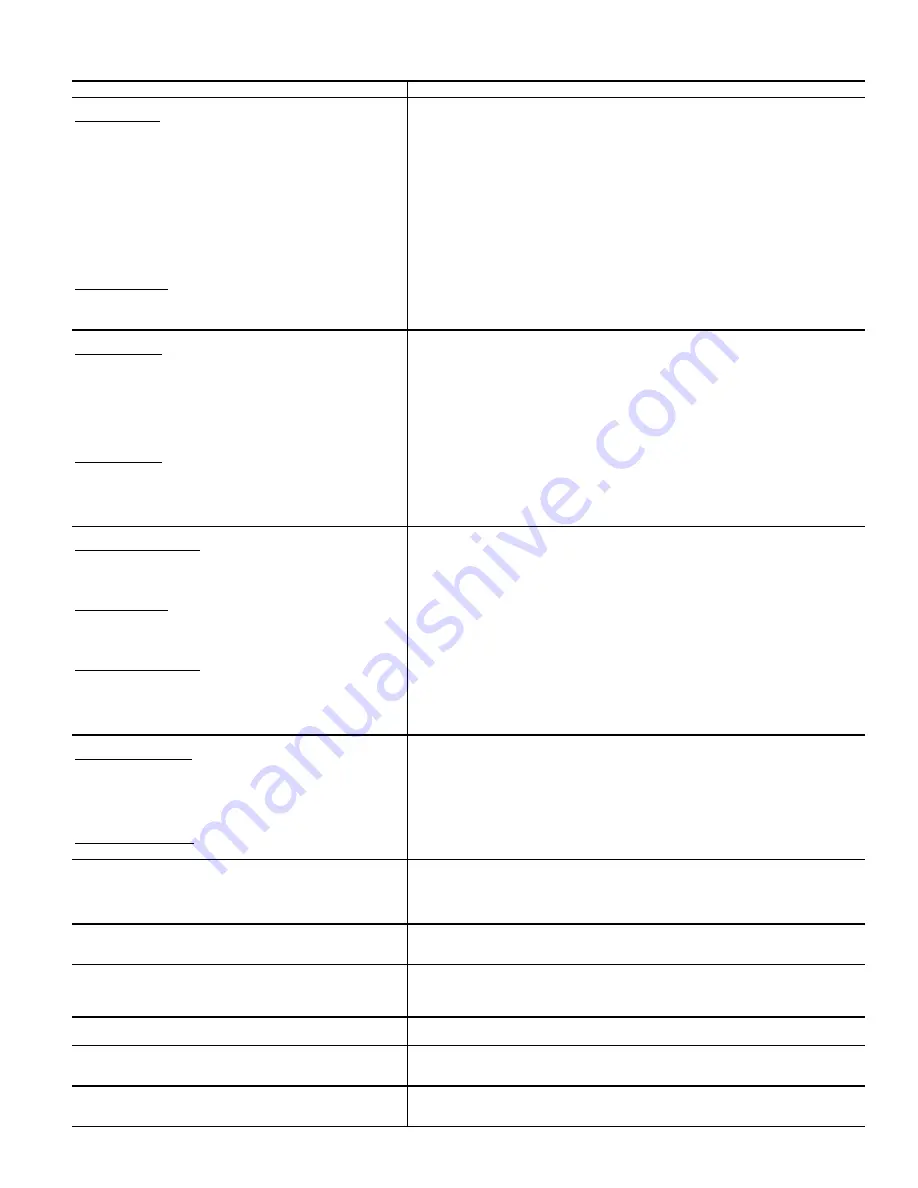
37
Table 23 — Troubleshooting
PROBLEM
SOLUTION
COMPRESSOR DOES NOT RUN
Contactor Open
1. Power off.
2. Fuses blown in field power circuit.
3. No control power.
4. Thermostat circuit open.
5. Safety device lockout circuit active.
6. Low-pressure switch open.
7. High-pressure switch open
8. Compressor over-temperature switch open.
9. Loose electrical connections.
10. Compressor stuck.
Contactor Closed
1. Compressor leads loose.
2. Motor windings open.
3. Single phasing.
1. Restore power.
2. After finding cause and correcting, replace with correct size fuse.
3. Check control transformer primary connections and circuit breaker.
4. Check thermostat setting.
5. Reset lockout circuit.
6. Check for refrigerant undercharge, obstruction of indoor airflow. Make sure liquid
line solenoid valve(s) is open.
7. Check for refrigerant overcharge, obstruction of outdoor airflow, air in system. Be
sure outdoor fans are operating correctly.
8. Check for open condition. Allow for reset. Replace compressor if necessary.
9. Tighten all connections.
10. See compressor service literature.
1. Check connections.
2. See compressor service literature.
3. Check for blown fuse. Check for loose connection at compressor terminal.
COMPRESSOR STOPS ON HIGH-PRESSURE SWITCH
Outdoor Fan On
1. High-pressure switch faulty.
2. Reversed fan rotation.
3. Airflow restricted.
4. Air recirculating.
5. Non-condensables in system.
6. Refrigerant overcharge.
7. Line voltage incorrect.
8. Refrigerant system restrictions.
Outdoor Fan Off
1. Fan slips on shaft.
2. Motor not running.
3. Motor bearings stuck.
4. Motor overload open.
5. Motor burned out.
1. Replace switch.
2. Confirm rotation, correct if necessary.
3. Remove obstruction.
4. Clear airflow area.
5. Recover refrigerant and recharge as required.
6. Recover refrigerant as required.
7. Consult power company.
8. Check or replace filter drier, expansion valve, etc.
1. Tighten fan hub setscrews.
2. Check power and capacitor.
3. Replace bearings.
4. Check overload rating. Check for fan blade obstruction.
5. Replace motor.
COMPRESSOR CYCLES ON LOW-PRESSURE SWITCH
Indoor-Air Fan Running
1. Liquid line solenoid valve(s) fails to open.
2. Filter drier plugged.
3. Expansion valve power head defective.
4. Low refrigerant charge.
Airflow Restricted
1. Coil iced up.
2. Coil dirty.
3. Air filters dirty.
4. Dampers closed.
Indoor-Air Fan Stopped
1. Electrical connections loose.
2. Fan relay defective.
3. Motor overload open.
4. Motor defective.
5. Fan belt broken or slipping.
1. Check liquid line solenoid valve(s) for proper operation. Replace if necessary.
2. Replace filter drier.
3. Replace power head.
4. Add charge. Check low-pressure switch setting.
1. Check refrigerant charge.
2. Clean coil fins.
3. Clean or replace filters.
4. Check damper operation and position.
1. Tighten all connections.
2. Replace relay.
3. Power supply.
4. Replace motor.
5. Replace or tighten belt.
COMPRESSOR RUNNING BUT COOLING INSUFFICIENT
Suction Pressure Low
1. Refrigerant charge low.
2. Head pressure low.
3. Air filters dirty.
4. Expansion valve power head defective.
5. Indoor coil partially iced.
6. Indoor airflow restricted.
Suction Pressure High
1. Heat load excessive.
1. Add refrigerant.
2. Check refrigerant charge. Check outdoor-air fan thermostat settings.
3. Clean or replace filters.
4. Replace power head.
5. Check low-pressure setting.
6. Remove obstruction.
1. Check for open doors or windows in vicinity of fan coil.
UNIT OPERATES TOO LONG OR CONTINUOUSLY
1. Low refrigerant charge.
2. Control contacts fused.
3. Air in system.
4. Partially plugged expansion valve or filter drier.
1. Add refrigerant.
2. Replace control.
3. Purge and evacuate system.
4. Clean or replace.
SYSTEM IS NOISY
1. Piping vibration.
2. Compressor noisy.
1. Support piping as required.
2. Replace compressor if bearings are worn.
COMPRESSOR LOSES OIL
1. Leak in system.
2. Crankcase heaters not energized during shutdown.
3. Improper interconnecting piping design.
1. Repair leak.
2. Check wiring and relays. Check heater and replace if defective.
3. Check piping for oil return. Replace if necessary.
FROSTED SUCTION LINE
Expansion valve admitting excess refrigerant.
Adjust expansion valve.
HOT LIQUID LINE
1. Shortage of refrigerant due to leak.
2. Expansion valve opens too wide.
1. Repair leak and recharge.
2. Adjust expansion valve.
FROSTED LIQUID LINE
1. Restricted filter drier.
2. Liquid line solenoid valve partially closed.
1. Remove restriction or replace.
2. Replace valve.