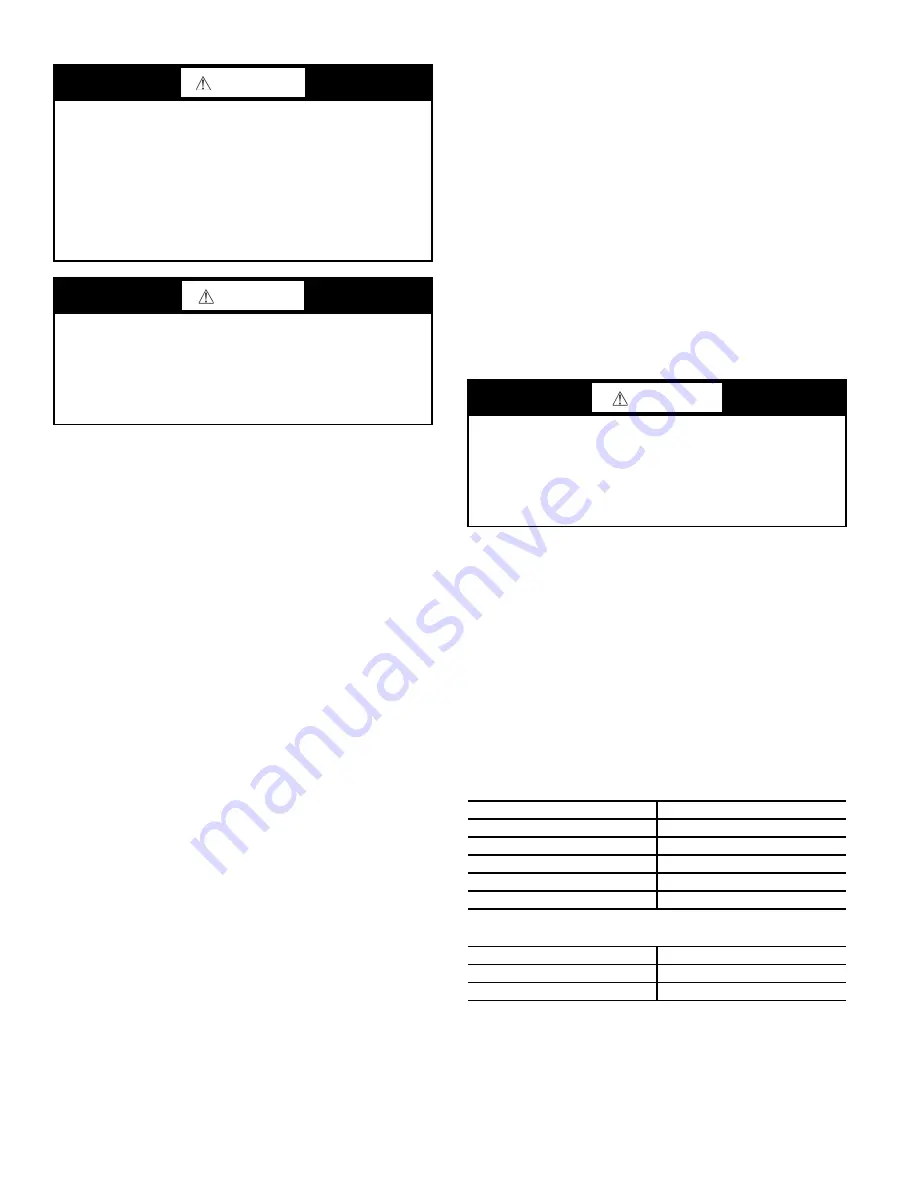
2
INSTALLATION GUIDELINES
Replacement/Retrofit — R-22 to Puron Refrigerant
Replacement/retrofit installations require change-out of outdoor
unit, metering device, and filter driers. Change-out of indoor coil
(evaporator) and interconnecting tubing is recommended.
EXISTING EVAPORATOR COIL
If the existing evaporator coil may be re-used, check with the
coil manufacturer to verify the coil construction is suitable for
operation with the higher pressures of Puron
®
refrigerant
(R-410A). Also determine if the existing TXV valve is com-
patible with R-410A, replace if necessary. The minimum facto-
ry test pressure rating must be 250 psig (1725 kPa). Existing
coil will need to be purged with Nitrogen to remove as much
mineral oil as possible to eliminate cross contamination of oils.
ACID TEST
If the existing system is being replaced because of a compres-
sor electrical failure, assume acid is in system. If system is be-
ing replaced for any other reason, use an approved acid test kit
to determine acid level. If even low levels of acid are detected,
install a 100 percent activated alumina suction-line filter drier
in addition to the replacement liquid-line filter drier. Remove
the suction line filter drier as soon as possible, with a maxi-
mum of 72 hr of operation. Recommendation: Install a ball
valve in the liquid line at the filter drier location when install-
ing a suction filter in the suction line.
EXISTING REFRIGERATION PIPING
Reuse of existing refrigerant piping involves three issues: quality
(strength) of existing tubing, cleanliness and tube size. Inspect all
tube segments and joints for signs of damage, corrosion or poor
brazing. Flush the interconnecting piping system with dry Nitro-
gen to eliminate as much trace of mineral oil as possible.
Same tube sizes are capable of handling higher flow rates (ex-
pressed as tons of cooling capacity) with Puron refrigerant com-
pared to R-22 at constant pressure drops. For example, a
1
/
2
-inch
OD liquid line is rated at 33% higher tons with Puron than with
R-22 (at 5°F pressure drop). A 1
1
/
8
-inch OD suction line is rated
at 53% higher tons with Puron than with R-22 (at 2°F pressure
drop). Refrigeration lines selected for R-22 use are typically
oversized for Puron applications. Carefully check the existing
suction line size against the table for maximum size; replace ver-
tical riser segments if necessary. Check existing liquid line size
against sizing data in Table 8 or 9; replace with smaller lines
when feasible.
INSTALLATION
1. Remove the existing evaporator coil or fan coil and install
the replacement coil when appropriate.
2. Drain oil from low points and traps in suction line tubing
(and hot gas bypass tubing if appropriate) and evaporator
if they were not replaced. Removing oil from evaporator
coil may require purging of the tubing with dry nitrogen.
3. Unless indoor unit is equipped with a Puron approved meter-
ing device, change the metering device to a thermal expan-
sion valve (TXV) designed for Puron refrigerant (R-410A).
4. Remove the existing outdoor unit. Install the new outdoor
unit according to these installation instructions.
5. Install a new field-supplied liquid-line filter drier at the
indoor coil just upstream of the TXV or fix orifice meter-
ing device.
6. If a suction line filter drier is also to be installed, install
suction line drier downstream of suction line service valve
at condensing unit.
7. If required, install a 100% activated alumina suction line
filter drier at the outdoor unit.
8. Evacuate and charge the system according to the instruc-
tions in this installation manual.
9. Operate the system for 10 hr. Monitor the pressure drop
across the suction line filter drier. If pressure drop exceeds
3 psig (21kPa), replace suction-line and liquid-line filter
driers. Be sure to purge system with dry nitrogen and
evacuate when replacing filter driers. Continue to monitor
the pressure drop across suction-line filter drier. Repeat
filter changes if necessary. Never leave suction-line filter
drier in system longer than 72 hr (actual time).
Rated Indoor Airflow (cfm)
Tables 1 and 2 lists the rated indoor airflow used for the AHRI
efficiency rating for the units covered in this document.
Table 1 — 569J***A/B/G/H with 524J***A
Table 2 — 569J***D/E/F with 524J***A
Identify Factory Options
Factory options will affect 569J unit pipe sizing selections.
Coil type impacts liquid lift limits; Hot Gas Bypass impacts the
selection of suction tube size in vertical riser segments. Check
this unit’s Model Number against the Model Number Nomen-
clature, Fig. 1. Determine the significance of this unit’s values
in Position 12 (Coil type) and Position 8 (Hot Gas Bypass,
WARNING
PERSONAL INJURY AND ENVIRONMENTAL
HAZARD
Failure to follow this warning could cause personal injury
or death.
Relieve pressure and recover all refrigerant before system
repair or final unit disposal.
Wear safety glasses and gloves when handling refrigerants.
Keep torches and other ignition sources away from refriger-
ants and oils.
CAUTION
PERSONAL INJURY HAZARD
Failure to follow this caution may result in personal injury.
Sheet metal parts may have sharp edges or burrs. Use care
and wear appropriate protective clothing, safety glasses and
gloves when handling parts and servicing air conditioning
equipment.
CAUTION
EQUIPMENT DAMAGE
Failure to follow this caution can result in equipment dam-
age.
Do not install a suction-line filter drier in liquid line. A liq-
uid-line filter drier designed for use with R-410A refriger-
ant is required on every unit.
MODEL NUMBERS
FULL LOAD AIRFLOW (CFM)
569J*07A/B — 524J*07A
2400
569J*07G/H — 524J*07A
2625
569J*08A/B — 524J*08A
3000
569J*12A/B — 524J*12A
4000
569J*14A/B — 524J*14A
4375
MODEL NUMBERS
FULL LOAD AIRFLOW (CFM)
569J*12D/E/F — 524J*12A
4000
569J*14D/E— 524J*14A
4400