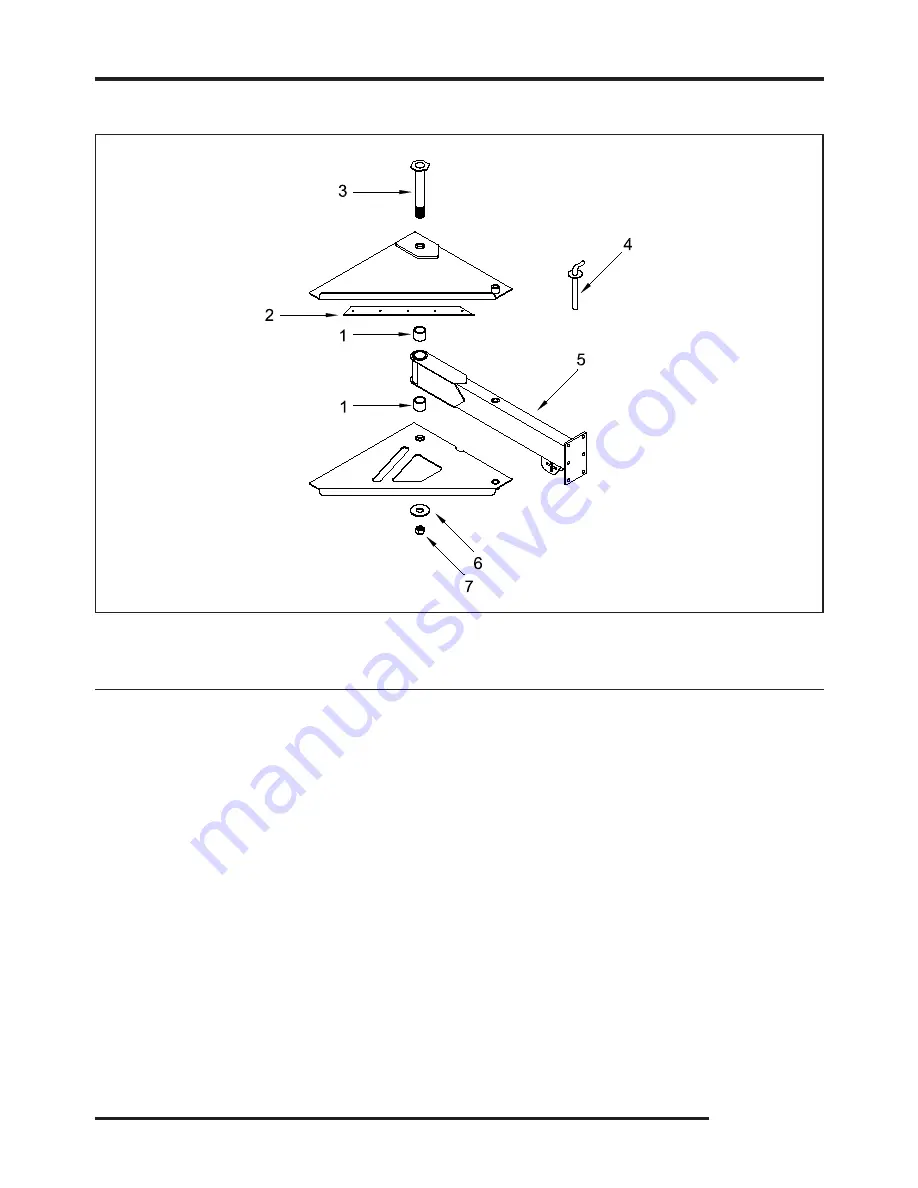
Bandit
Copyright 12/07
PAGE 117
MODELS 1290XP/1590
OPTIONAL COMPONENTS
MODEL 190
LOCATION
PART NUMBER
DESCRIPTION
1.
900-1907-82
Tension Bushing
2.
911-1002-2
Articulating Tongue Plastic Slide
.
91-1017-16
Articulating Tongue Pivot Pin
4.
980-0500-16
Articulating Tongue Lock Pin
.
911-000-0
Articulating Tongue Assembly
6.
900-90-9
Articulating Tongue Pivot Pin Washer
7.
91-901-10
Articulating Tongue Pivot Pin Nut
8.
900-906-27
Articulating Tongue Cylinder (Not Shown)
9 a.
900-3920-01
Articulating Tongue Valve (SAE O-Rings) (Not Shown)
b.
900-3901-42
Articulating Tongue Valve (Pipe Fittings) (Not Shown)
MODEL 1590 ARTICULATING TONGUE
NOTE: Parts may not be exactly as shown.
Summary of Contents for 1290XP
Page 2: ......
Page 17: ......
Page 39: ...Bandit Copyright 12 07 PAGE 23 MODELS 1290XP 1590 DECALS...
Page 40: ...Bandit Copyright 12 07 PAGE 24 MODELS 1290XP 1590 DECALS...
Page 70: ......