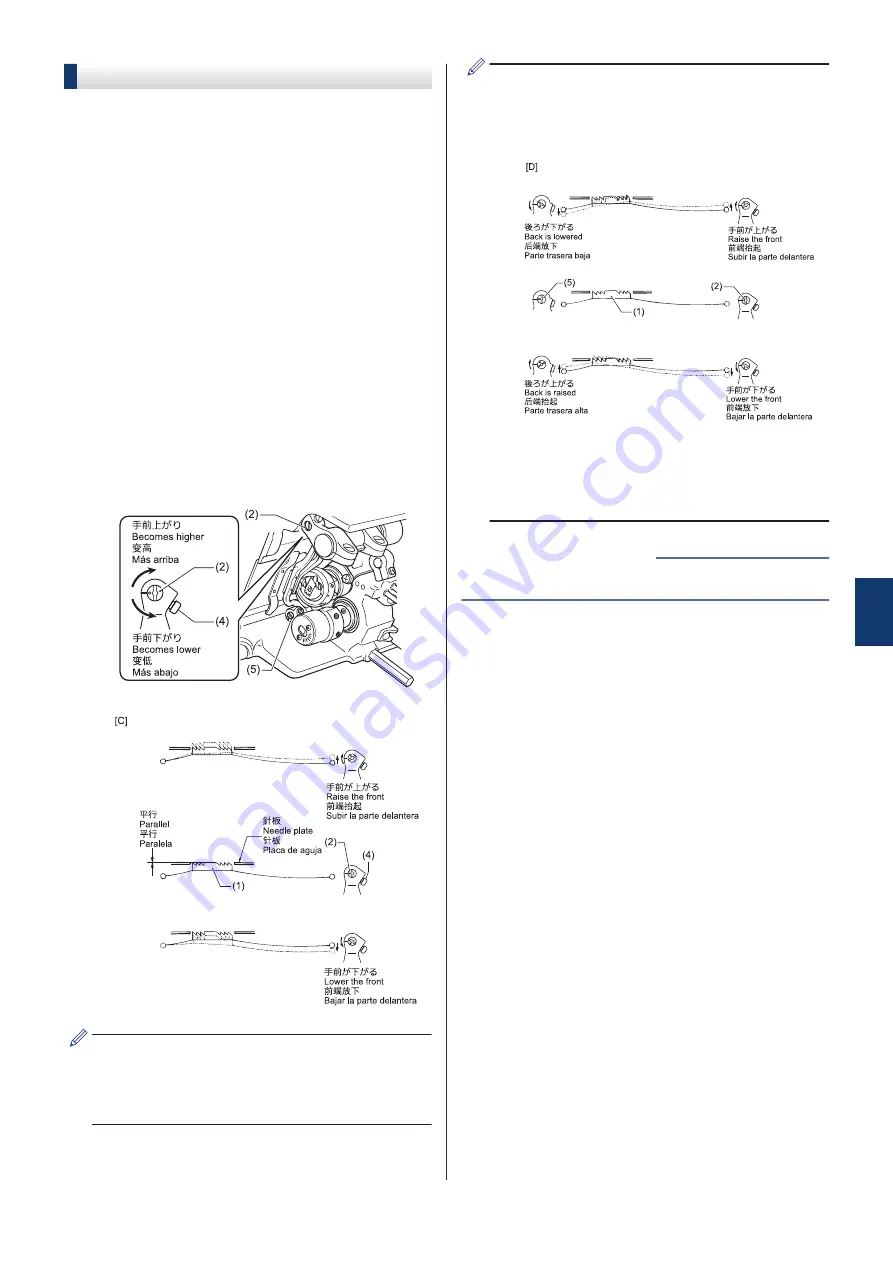
Adjusting the feed dog angle
The standard angle is for the feed dog (1) to be parallel
to the needle plate when the machine pulley is turned
forward to raise the feed dog (1) from its lowest
position until it is flush with the top of the needle plate.
1
Turn the machine pulley forward to raise the feed
dog (1) from its lowest position until it is flush with
the top of the needle plate, and stop turning the
machine pulley at that point.
2
Tilt back the machine head.
3
Loosen the two set screws (4).
4
Turn the feed base shaft (2) in the direction of the
arrow within a range of 90º with respect to the
standard position. (Figure [C])
• In order to prevent puckering, lower the front of
the feed dog (1).
• In order to prevent the material from slipping,
raise the front of the feed dog (1).
5
Securely tighten the two set screws (4).
• If you would like to tilt the feed dog (1) further,
turn the feed lifting rocker shaft (5) while
carrying out the above adjustment. (Figure [D])
To learn more, see
Related Information
.
• The height of the feed dog (1) will change after
the angle has been adjusted. It will be
necessary to re-adjust the height of the feed
dog (1).
• Adjusting the height of the feed dog on page 58
Related Information
7
Adjusting the sewing machine (Standard adjustments)
59