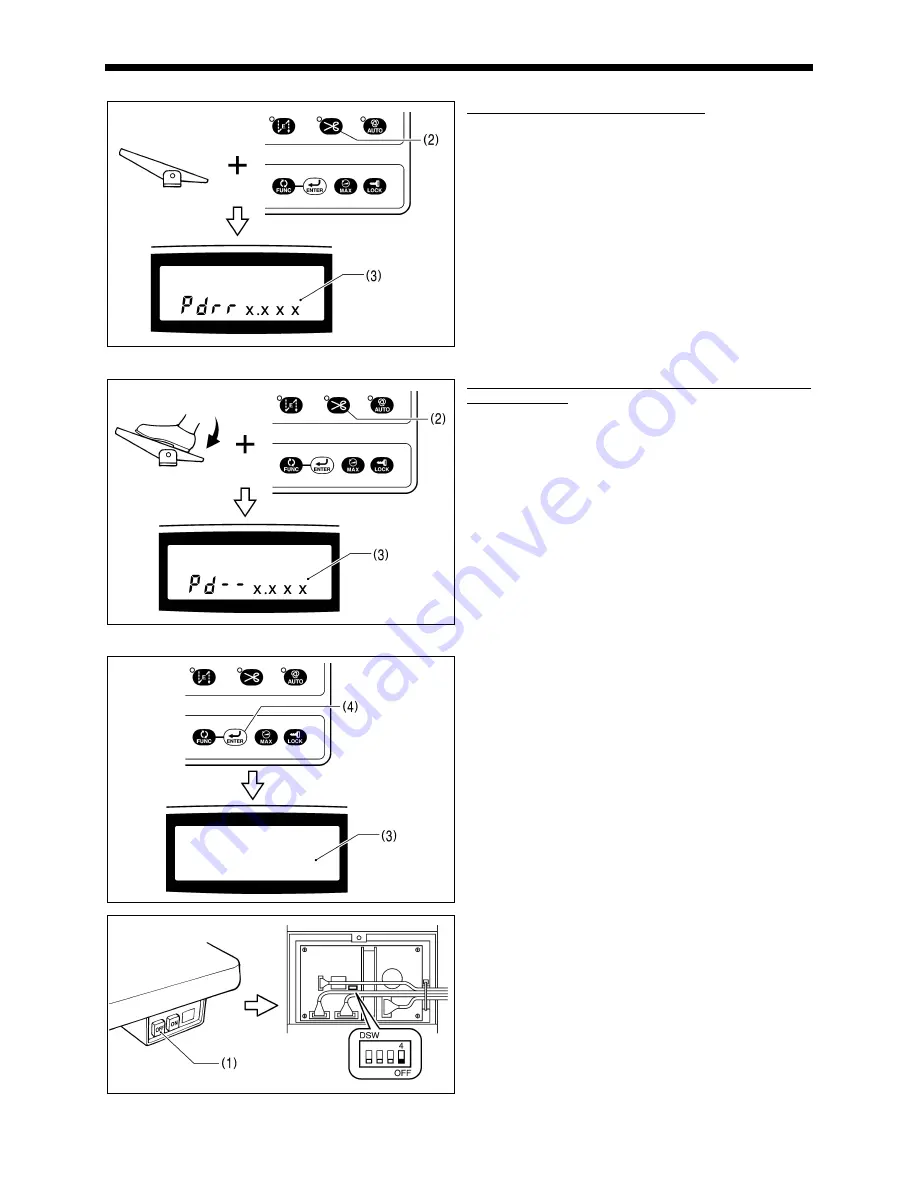
S-7200A
10. TREADLE UNIT ASSEMBLY
50
3) Memorizing the neutral position
With your foot released from the treadle, press the thread
trimming key (2).
"Pdrr x.xxx" will appear in the main display (3).
4) Memorizing the maximum backward position
With the treadle depressed backward to the maximum
backward position, press the thread trimming key (2).
"Pd-- x.xxx" will appear in the main display (3).
5) Completion of setting
1. Press the ENTER key (4).
The buzzer will sound and the main display (3) will switch
off.
NOTE:
If you do not press the ENTER key (4), the settings
will not be memorized.
2. Turn off the power switch (1).
3. Set DIP switch No.4 to OFF.
2337M
2335M
2336M
2338M