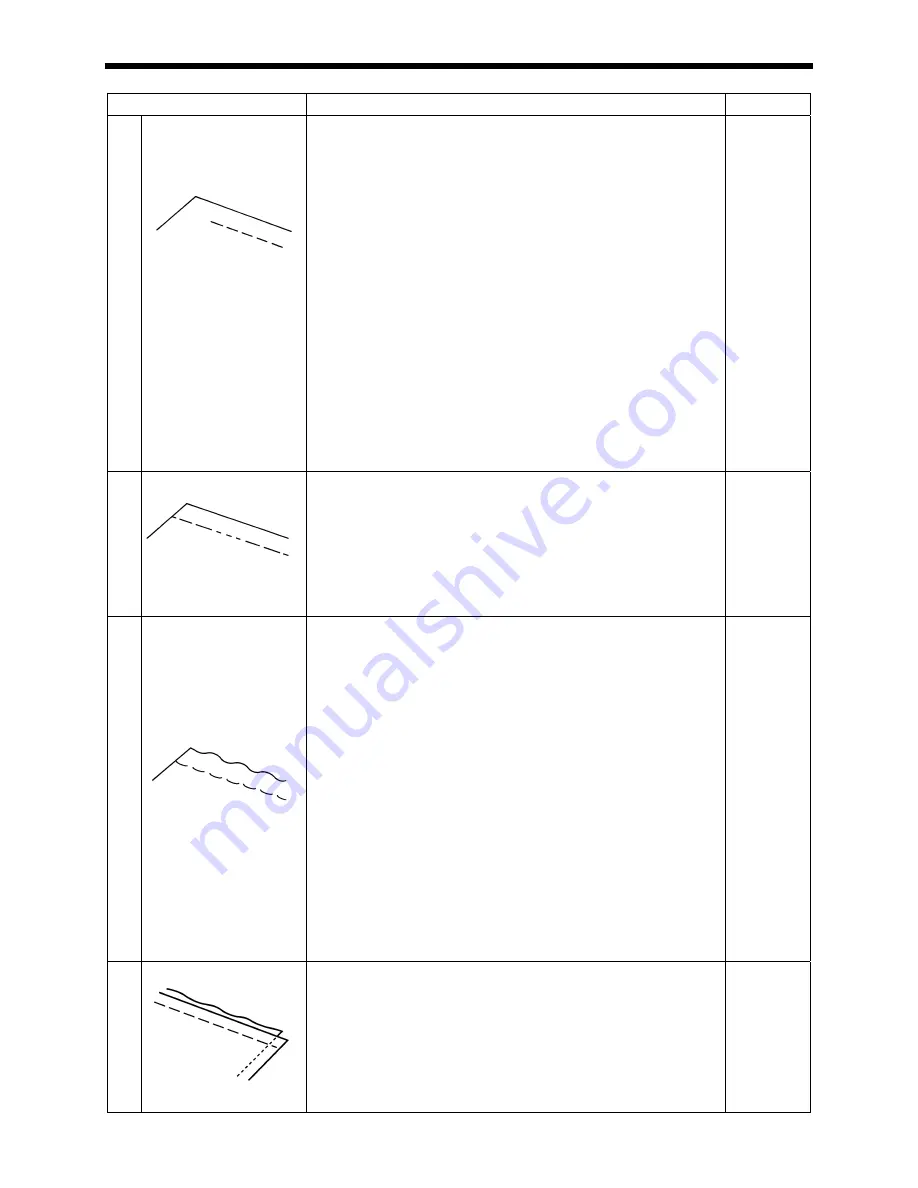
S-7200B
13. TROUBLESHOOTING
65
Problem Possible
cause
Page
5 Skipped stitches at sewing
start
Thread unravelling at
sewing start
Is the thread take-up spring tension too strong?
Reduce the tension of the thread take-up spring.
Is the thread take-up spring operating range too large?
Lower the position of the thread take-up spring.
Are the trailing lengths of the upper threads too short after thread
trimming?
Adjust the pretension.
Are the threads not being trimmed cleanly?
Sharpen the fixed knives, or replace the fixed and movable
knives if necessary.
Is the needle too wide?
Try using a needle with a count that is one lower than the
current needle.
Is the length of thread trailing out from the bobbin case after thread
trimming too short.
If the bobbin is spinning loosely, replace the anti-spin spring in
the bobbin case.
Is the sewing speed too fast at the sewing start?
Use the slow start feature.
Is the needle up stop position too high?
Adjust the needle up stop position.
26
26
Instruction
manual
Instruction
manual
Instruction
manual
34, 35
6 Uneven
seam
Is the presser foot pressure too weak?
Adjust the presser foot pressure.
Is the feed dog too low?
Adjust the feed dog height.
Is the bobbin scratched?
If the bobbin is damaged, smooth it with an oiled grindstone or
replace it.
Instruction
manual
28
7 Large degree of puckering
(excess tension)
Is the upper thread tension too strong?
Make the upper thread tension as weak as possible.
Is the lower thread tension too strong?
Make the lower thread tension as weak as possible.
Is the needle tip blunt?
Replace the needle if it is blunt.
Is the needle too thick?
Replace with as thin a needle as possible.
Are the thread take-up spring tensions too strong?
Make the thread take-up spring tension as weak as possible.
Is the thread take-up spring operating range too large?
Lower the position of the thread take-up spring to as low a
position as possible.
Is the presser foot pressure too strong?
Adjust the presser foot pressure.
Is the sewing speed too fast?
Use the sewing speed control keys to gradually reduce the
sewing speed.
Is the angle of the feed dog correct?
Tilt the front of the feed dog down slightly.
Instruction
manual
Instruction
manual
26
26
Instruction
manual
Instruction
manual
29
8 Material
slippage
Is the presser foot pressure too strong?
Adjust the presser foot pressure.
Instruction
manual
0749M
0473M
0978M
0750M