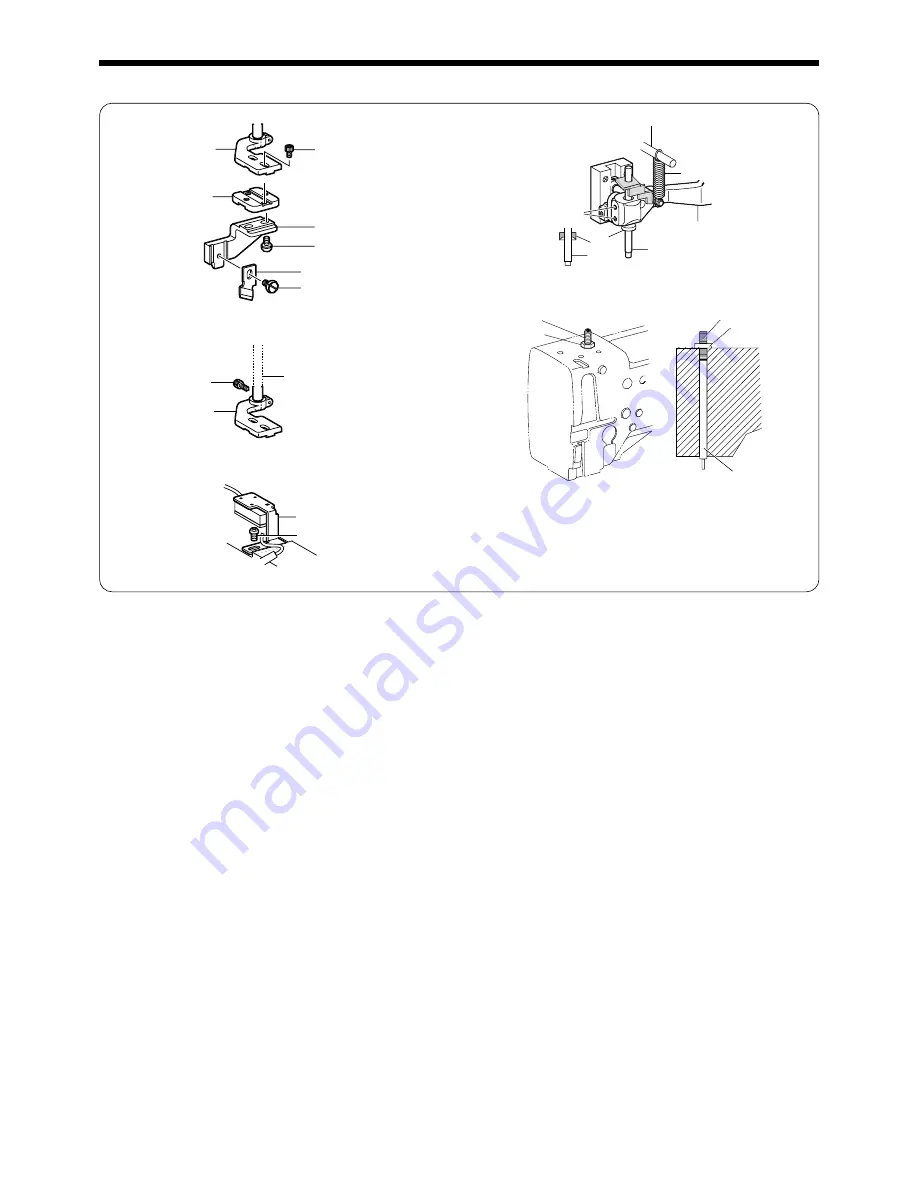
LH4-B800E
2 - 14
2. DISASSEMBLY
2-8. Cutter mechanism
Remove the screw
q
, and then remove the cutter
w
from cutter holder DL
e
.
Remove the screw
r
, and then remove cutter holder DL
e
from cutter holder M
t
.
Remove the bolt
y
, and then remove cutter holder M
t
from the cutter holder
u
.
Remove the bolt
i
, and then remove the cutter holder
u
from the cutter driving shaft
o
.
Remove the screw
!0
, and then remove the knife sensor assembly
!1
.
Remove the spring
!2
from the cutter driving arm assembly
!3
and the tension release shaft
!4
.
Remove the nut
!5
, and then remove the adjusting screw assembly
!6
from the arm.
Loosen the two set screws
!7
, and then remove the cutter driver shaft
o
.
Remove the oil rejector
!8
.
t
r
e
q
!0
o
i
u
y
!1
w
u
!3
!2
!8
!7
!6
!6
o
o
!5
!5
!4
!8
o
Summary of Contents for LH4-B800E
Page 55: ...LH4 B800E 2 30 2 DISASSEMBLY ...
Page 87: ...LH4 B800E 3 32 3 ASSEMBLY ...