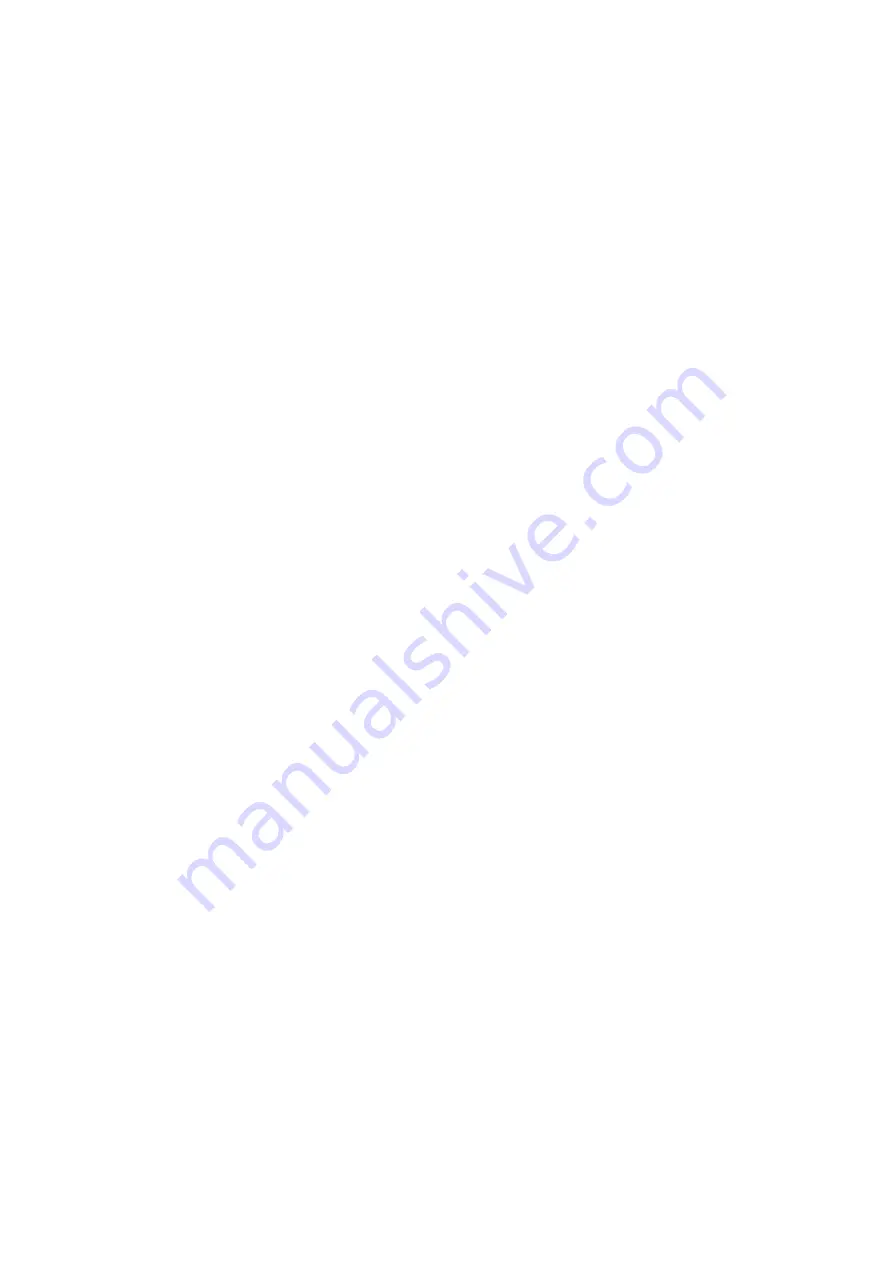
x
2.
Workflow in the Field
< Initial Actions >
1. Question the Customer for details about the system malfunction.
2. Note down the meter count.
3. Inspect the rejected print and determine the machine condition.
4. Check the Machine Log Book.
< For UM visit >
1. Perform the Level 1 troubleshooting.
2. Perform the troubleshooting.
3. Print any Internal Test Pattern to check the print quality. (See page V-51)
4. Feed paper from each tray, and clean or replace the feed role as required.
5. Repair any secondary problems that would prevent the machine from running.
6. Perform the trim activities.
< For SM visit >
1. Print any Internal Test Pattern to check the print quality. (See page V-51)
2. Feed paper from each tray, and clean or replace the feed role as required.
3. Repair any secondary problems that would prevent the machine from running.
4. Perform the trim activities.
< Final Actions >
1. Check the machine overall operation and function.
2. Check the machine appearance and consumables.
3. Perform the operator training as required.
4. Record the performed action in the Machine Log Book and Service Report.
5. Store the sample printouts in the Machine Log Book.
Summary of Contents for HL-4000CN
Page 22: ...CHAPTER I SPECIFICATIONS ...
Page 52: ...CHAPTER II INSTALLATION ...
Page 76: ...CHAPTER III STRUCTURE OF SYSTEM COMPONENTS ...
Page 129: ...CHAPTER IV ASSEMBLY DISASSEMBLY ...
Page 132: ...2 5 21 Roll ASSY IV 74 2 5 22 Cassette ASSY front IV 74 2 5 23 Holder retard IV 75 ...
Page 208: ...CHAPTER V TROUBLESHOOTING ...
Page 281: ...V 71 9 4 Straightness Fig 5 13 9 5 Magnification Error Fig 5 14 9 6 Registration Fig 5 15 ...
Page 282: ...V 72 9 7 Guaranteed Printing Area Fig 5 16 ...
Page 295: ...CHAPTER VI 5 06 ...
Page 336: ...CHAPTER VII 3 8 3 211 725 2 7 216 ...
Page 341: ...VII 4 P J LAYOUT DIAGRAM 2 1 IOT Top ...
Page 342: ...VII 5 2 2 IOT Front RH ...
Page 343: ...VII 6 2 3 MCU and HVPS PWB ESS PWB ...
Page 344: ...VII 7 2 4 Tray1 ...
Page 345: ...VII 8 2 5 2 Tray Module ...