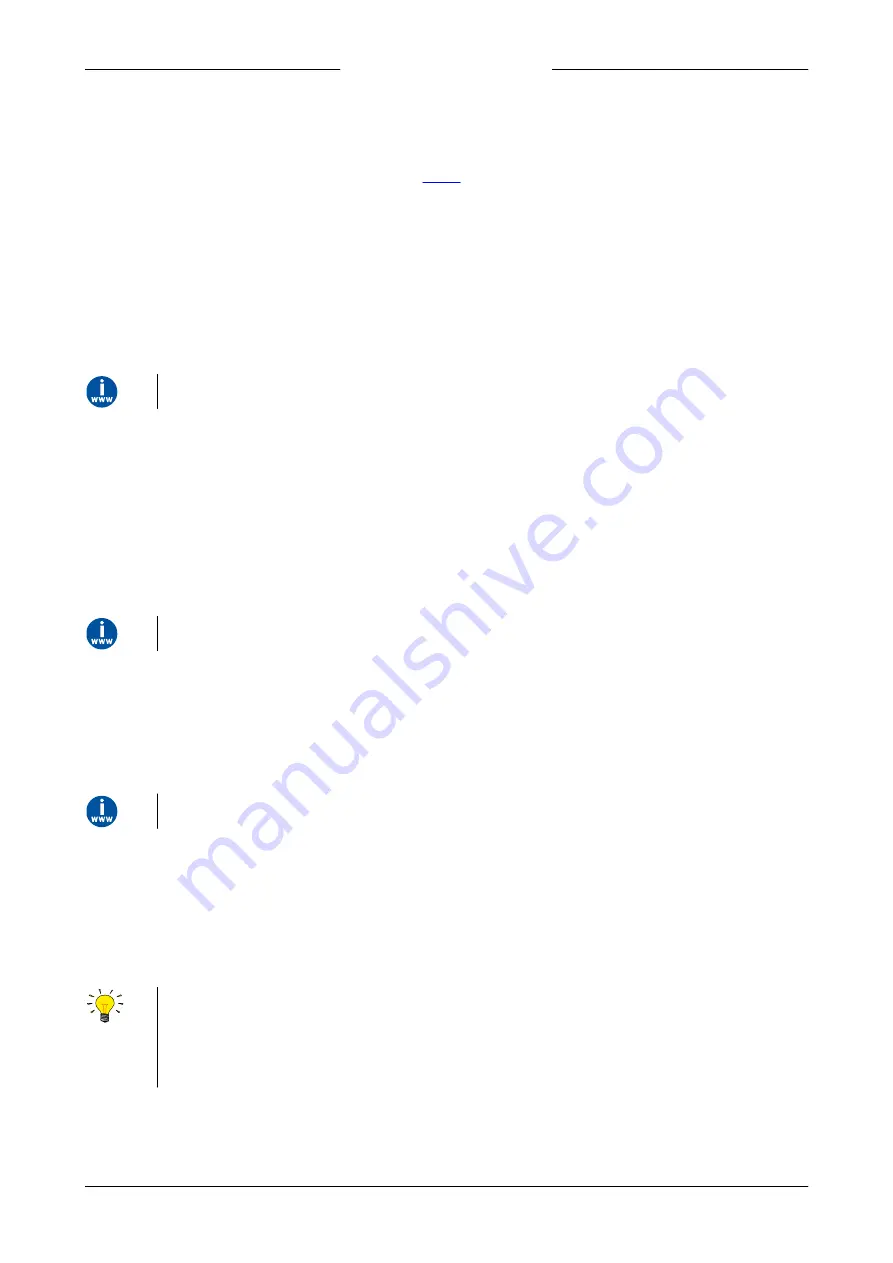
Bronkhorst®
Instruction Manual mini CORI-FLOW™ M1x
9.17.050O
26
3.9.3
Fieldbus operation
FLOW-BUS
Digital Bronkhorst® instruments can be monitored and operated via RS-232 using the free
FlowWare
software tools for
Windows. These tools provide a graphical interface to the
protocol (used by FLOW-BUS), for monitoring and
changing instrument parameters.
The FlowWare toolkit provides functionality for monitoring and operating digital instruments (FlowPlot, FlowSuite) and
selection of the active fluid and configuration of the fieldbus connection (if applicable). For instruments that support the
definition and use of multiple fluids, FlowTune™ can be used to define and store fluids in the instrument and select the
active fluid.
Digital instrument parameters are made accessible by
FlowDDE
, a Dynamic Data Exchange server (DDE) that handles
communication between the instrument and (dedicated) client software in Windows (e.g. FlowPlot). FlowDDE can also be
used by other client applications, such as Microsoft Office or custom made software, built with third party development
software like LabVIEW or a SCADA platform.
The FlowWare tools and associated documentation can be downloaded from the product pages on the Bronkhorst website:
Modbus
Instruments in a Modbus system can be monitored and operated using third party software as a master device, such as
LabVIEW, ModScan, or a Modbus PLC.
PROFIBUS-DP
Instruments in a PROFIBUS DP system can be monitored and operated using third party software as a master device, such as
TIA Portal (by Siemens).
To configure a device, a so-called GSD file (General Station Description) has to be loaded into the software. The GSD file
contains all necessary configuration information to operate the device in a PROFIBUS DP system, including all available
operating parameters with their data types.
A GSD file for Bronkhorst® instruments can be downloaded from the product pages on the Bronkhorst website:
DeviceNet™
Instruments in a DeviceNet™ system can be monitored and operated using third party software as a master device, such as
TIA Portal (by Siemens).
To configure a device, a so-called EDS file (Electronics Data Sheet) can be loaded into the software. The EDS file contains all
necessary configuration information to operate the device in a DeviceNet™ system, including communication and network
configuration, and all available operating parameters with their data types.
An EDS file for Bronkhorst® instruments can be downloaded from the product pages on the Bronkhorst website:
3.10
Adjusting zero point
Zero-stability
The zero point of a Bronkhorst® flow meter/controller (the measurement signal that indicates the absence of a flow) is
factory adjusted at approximately 20 °C and atmospheric pressure (ambient conditions), with the instrument positioned
upright. Under normal circumstances (i.e. when process conditions are constant), the zero point will remain stable. However,
several factors might cause the instrument to develop a zero-stability error over time, causing it to detect a flow when
actually there is none. The zero-stability error can be neutralized by re-adjusting the zero point.
·
If the ambient conditions or mounting orientation are significantly different from the factory adjustment conditions,
zeroing a new instrument is recommended before using it for the first time.
·
Always check the zero point after fluid connections and/or electrical connections have been disconnected or if the
instrument has been moved.
·
If the instrument still detects a (steady) flow while all valves are closed and the fluid system is leak tight, (re-)adjusting the
zero point is recommended.