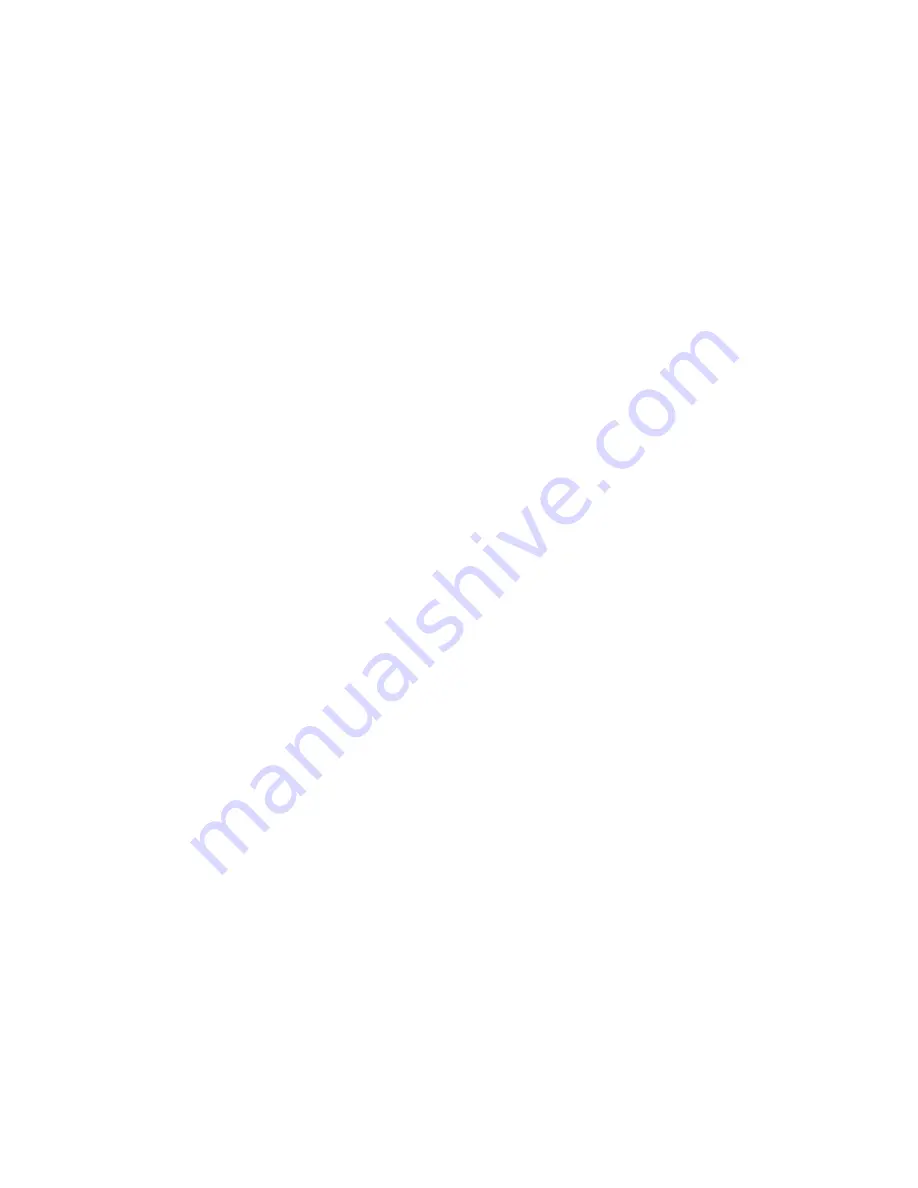
3-15
HYDRAULIC SYSTEM
The IC-280 hydraulic system consists of two sub-systems, driven by a double pump with a sin-
gle inlet port. The 29-GPM (110 L/min) vane pump supplies the hydrostatic steering function
and the boom & outrigger functions. The hoist and brake booster are powered by the 34-GPM
(129 L/min) vane pump.
The boom, outriggers, hoist, and optional front winch are controlled by one valve assembly.
The 29-GPM (110 L/min) pump flow enters the steering flow control valve first and then flows
into the left-hand section of the control valve assembly supplying the swing, telescope, boom
and outrigger sections. The flow from the 34-GPM (129 L/min) pump enters the brake booster
flow control valve first and all but 4-GPM (15 L/min) is directed to the inlet section to the left of
the hoist valve. Adjustment procedures for the crane hydraulic functions are given on page 3-22
through 3-24. The schematics of the hydraulic system are shown on pages 3-16.
STEERING SYSTEM
The steering system is shown in the schematic on the next page. The IC-280 steering system is
a load-sensing, demand-type system that takes only as much flow as is needed when steering,
and directs the excess flow to the control valve for boom & outrigger functions. The priority
flow-control valve is in the line between the 29-GPM (110 L/min) pump section and control
valve.
Oil from the 29-GPM (110 L/min) section of the pump goes into the priority valve at port "P."
When no steering is required, the entire flow goes through the priority valve and leaves through
port "EF" to the crane valve. The crane operating speed is not affected, since there is no loss of
volume passing through the priority valve.
When the steering wheel is turned, the load-sensing line signals the priority valve to divert the
required amount of oil to the steering control unit to meet the steering system requirements.
The excess oil, not required for steering, flows to the crane control valve as usual. Since the
amount of oil required for steering is usually a small portion of the pump output, the crane con-
trol valve is always operational while the unit is being steered. Crane operation speed is re-
duced such a slight amount, it is usually not noticed.
The steering control unit is non-load reactive. This means that bumps, curbs, and obstacles
cannot change the steering angle and are not felt in the steering wheel. It also means that the
wheels do not recenter when the steering wheel is released. The steering wheel must be turned
back to center at the end of a turn.
There is a check valve in the pressure line between the priority valve and the steering control
unit. This prevents pressure in the steering cylinders from venting back into the pressure line
when the pressure is low. This eliminates steering wheel kickback when the steering wheel is
released.
The steering system pressure was set at 1800 PSI (124 bar) at the factory, and this should not
need adjustment.
Summary of Contents for IC-280-A
Page 6: ...1 2 IC 280 A DIMENSIONS...
Page 7: ...1 3 IC 280 A TURNING DIMENSIONS...
Page 16: ......
Page 30: ...2 14...
Page 42: ......
Page 51: ...3 9 IC 280 A LUBRICATION CHART...
Page 58: ...3 16 HYDRAULIC SCHEMATIC...
Page 67: ...3 25 BOOM CHAIN ADJUSTMENT...
Page 72: ......
Page 73: ......
Page 74: ......
Page 75: ......