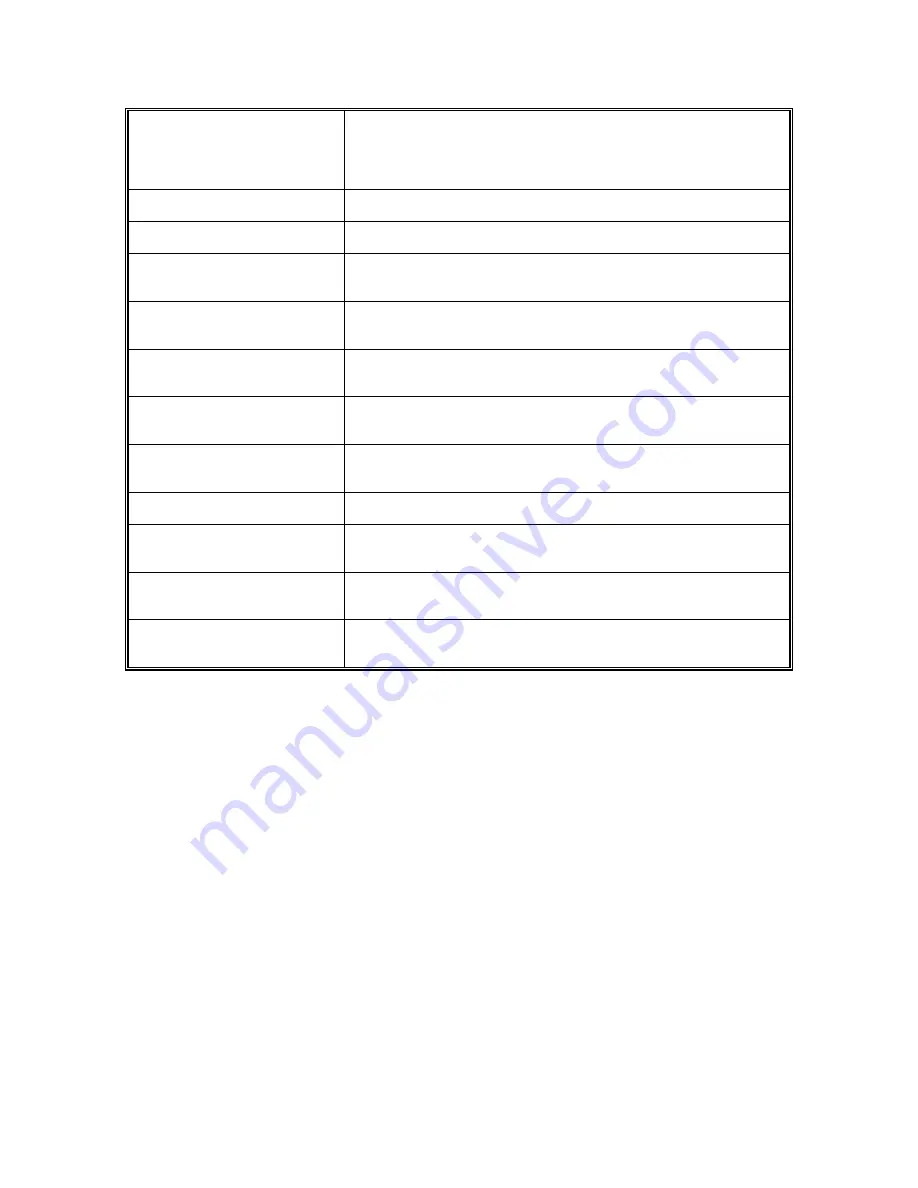
Back Harness Assembly:
Clean with oil-free cloth/rags and oil-free brushes. If extremely dirty,
clean with warm soapy water, rinse with clean fresh water, and air dry.
Confirm the serviceability of the straps, buckles, and fasteners.
SCUBA Backpack
Check for wear and other damage. Inspect serviceability.
Backpack Pad
Inspect the serviceability / check for damage.
Backpack Harness
Ensure proper functioning of adjusters and snaps. Inspect for wear
and/or other damage.
Tank Strap / Keeper
Strap
Inspect for cuts, excessive wear, or any other damage. Ensure the
serviceability of the buckle / tensioner.
Rod Extender, 14"
Ensure proper functioning. Inspect for bends, wear, and/or other
damage. Check the serviceability of the collet, collet nut, and threading.
Case
Inspect for dents, cracks, holes, or other damage. Make sure all
securing hasps/hardware functions properly.
Rod Quiver
Ensure functionality of all snaps, buckles, fasteners, and clips. Inspect
the stitching, as well as for holes and other damage.
Leather Striker Holder
Check for wear and damage. Ensure the item is serviceable.
Leather Shield
Check for burns, holes, damage, and/or wear. Ensure the shield
functions properly on torch. Replace as required.
Leather Gloves
Check for burns, tears, holes, and any other damage. Examine the
stitching and inspect the overall serviceability.
Safety Glasses, #5 Lens
Inspect for cracks, scratches, or other damage. Check for overall
serviceability.