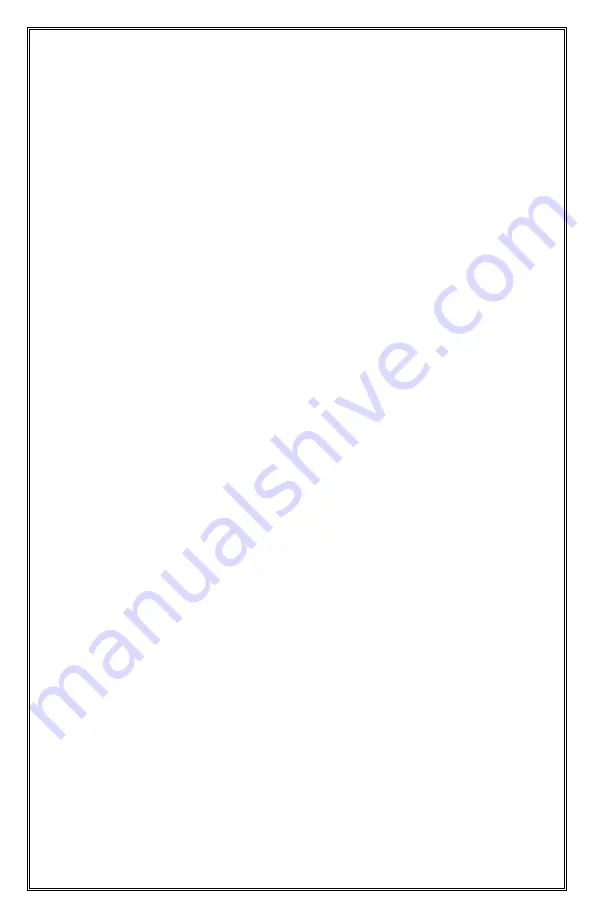
Ambient temperature before repairs were made:____________________________
Static Pressure before repair is made: High:_____________ Low:______________
Running Pressure before repair is made:__________________________________
Any odd or unusual noises before repairs are made: ________________________
__________________________________________________________________
__________________________________________________________________
How much refrigerant was recovered:__________________________________lbs.
Automated flush of system (by flush mechanic) Yes:_________ No:__________
Manual flush (by tech changing oil and/or drier) Yes:_________ No:__________
Repairs made and parts replaced: _______________________________________
__________________________________________________________________
__________________________________________________________________
Ambient temperature after repairs are made:_______________________________
How much refrigerant was charged:_______lbs. _______oz. (Virgin or Recovered)
Static Pressure: High:_____________ Low:______________
Running Pressure: High:____________Low: ______________
Vent Temperature:____________________________________________________
Cab Temperature:_____________________________________________________
Broom S/N:_________________________________________________________
Hr.:___________________________ Date:_______________________
Company or Facility who made repairs: ___________________________________
Technicians initials:___________________________________________________
MAINTENANCE
Warranty Claim Form for Broce A/C Systems
and Components