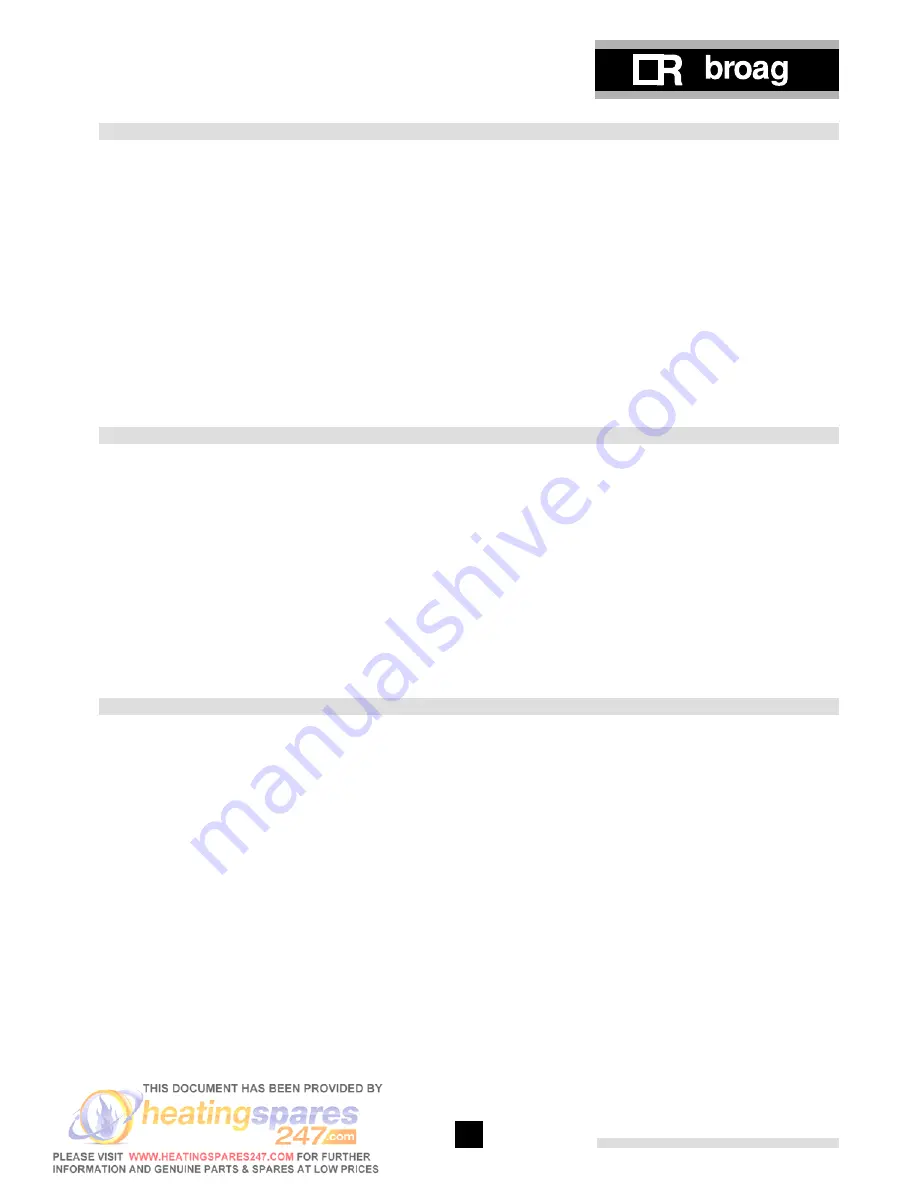
3
PREFACE
These technical instructions contain useful and impor-
tant information for the correct operation and mainte-
nance of the Remeha boiler, model Gas 350.
Read these instructions carefully before putting the
boiler into operation, familiarise yourself with its control
functions and operation, strictly observing the instruc-
tions given. Failure to do so may invalidate warranty or
prevent the boiler from operating.
A competent Engineer, with the relevant certification
(i.e. CORGI, ACOPS, IEE regs. etc.) must carry out the
installation and commissioning of the boiler.
On completion a copy of the boiler log / commissioning
sheet should be returned to Broag Ltd for record pur-
poses.
If you have any questions, or if you need more informa-
tion about specific subjects relating to this boiler, or it’s
installation please do not hesitate to contact us.
The data published in these technical instructions is
based on the latest information (at date of publication)
and may be subject to revisions.
We reserve the right to continuous development in both
design and manufacture, therefore any changes to the
technology employed may not be retrospective nor may
we be obliged to adjust earlier supplies accordingly.
1 BOILER
DESCRIPTION
The Remeha Gas 350 boiler is a cast iron sectional
floor standing gas fired boiler with Class II reduced NO
X
burners. Supplied c/w control high/low and high limit
thermostats, automatic ignition and flame failure safety
controls. Suitable for all qualities of natural gas and pro-
pane, cat. II
2H3B/P
. The Remeha Gas 350 central heating
boiler is approved according to the following European
directives:
-
Gas appliance directive no. 90/396/EEC,
-
Efficiency directive no. 92/42/EEC,
-
E.M.C. directive no. 89/336/EEC,
-
Low voltage directive no. 73/23/EEC.
Remeha Gas 350 PIN: 0063AS3842
Classification type for evacuation of the combustion pro-
ducts: B
11BS
, B
11
.
For further advice or information contact Broag Ltd.
The Remeha Gas 350 is supplied with electronic junc-
tion with insulated casings.
2 CONSTRUCTION
DETAILS
2.1 General
The Remeha Gas 350 is a floor standing boiler com-
plete with temperature and safety controls. The cast iron
sectional heat exchanger is assembled using conical
nipples and jointing compounds and ceramic rope. The
finished unit is cased in an insulated enamel coated
steel enclosure. The boiler has a built in draught diver-
ter. It has water and gas connections within the casings
at the rear right hand side (when viewed from the front).
The boiler is supplied prewired requiring only permanent
mains supply and external control connections.
2.2 Burners
The burners are stainless steel, atmospheric type with
cooling rods to reduce the flame temperature. They gua-
rantee a low noise level and a reduced NO
X
-emission.
Front and top access is required for service work to be
carried out.
2.3 Boiler
Floor
The Remeha Gas 350 boiler is supplied as standard
with reflecting floor plates with ventilation underneath.
2.4 Delivery
The boilers are supplied in sections for on site assem-
bly. The gas train, control panel, burners and casings
supplied loose for fitting one site by others. The 4 - 6
units can also be delivered pre-assembled with the main
block pressure tested.