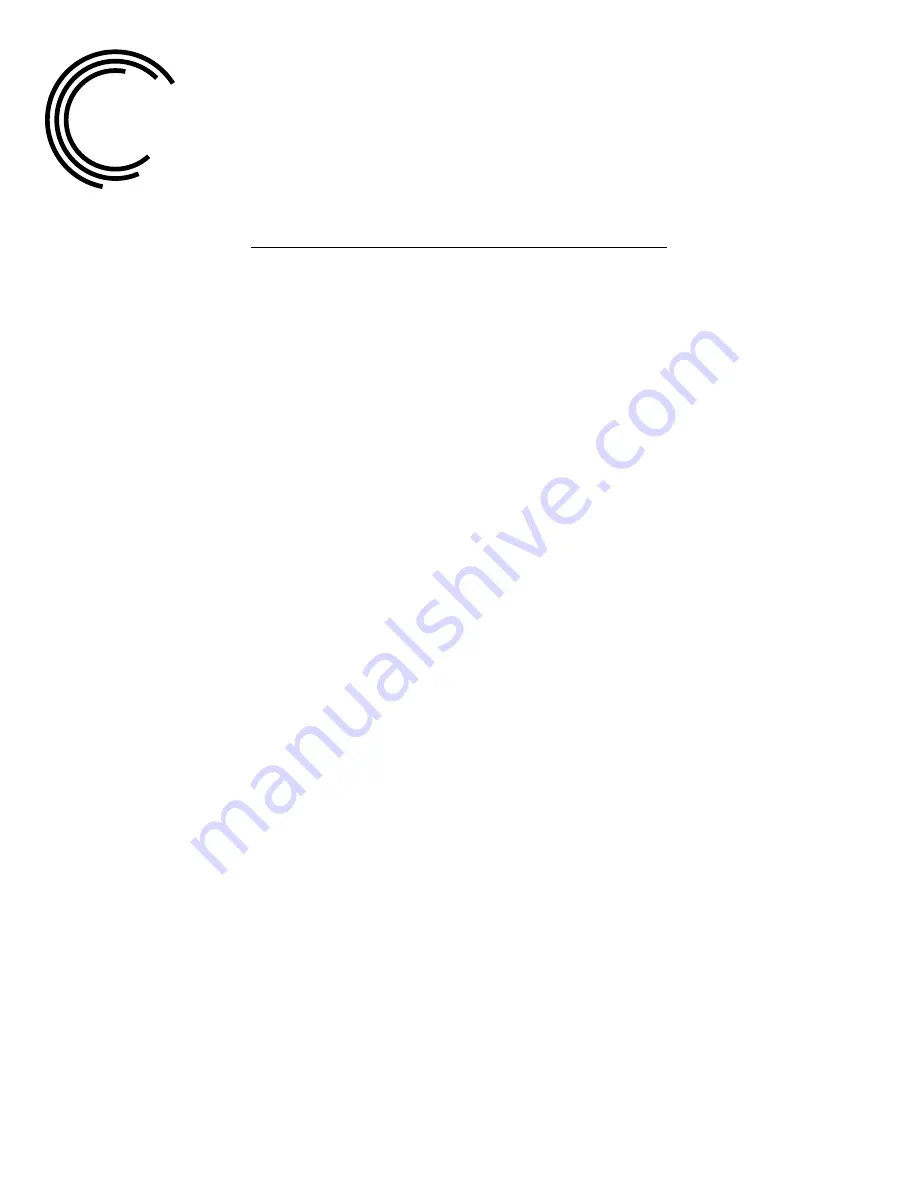
SAFETY, MAINTENANCE,
AND STORAGE
5
WARNING:
Read all instructions before using this equipment.
When using any electrical equipment, basic precautions should always be followed, including the following
to reduce the risk of, but not limited to, fire, electric shock, or injury:
1. Operate the equipment only as described in this manual.
2. Do not leave equipment unattended when plugged in a power outlet. Unplug from the outlet when
not in use and before cleaning.
3. Do not use the equipment on wet surfaces. Do not expose to rain. Store indoors.
4. Stay alert and use common sense when operating the equipment. Do not use the equipment if tired
or under the influence of drugs, alcohol, or medication. A moment of distraction while operating the
equipment may result in personal injury and to others.
5. Do not allow children and/or an unqualified person to use the equipment. Keep children and pets
away during use. The equipment is not a toy.
6. Do not use if power cord or plug is damaged in anyway. Do not pull or carry the equipment by the
power cord. Keep power cords away from heated surfaces.
7. Do not unplug the equipment from the power outlet by pulling on the power cord. To unplug, grasp
the plug, not the power cord.
8. Turn off all necessary controls before unplugging.
9. Do not handle plug or equipment with wet hands.
10. To reduce your exposure to chemical reactions, vapors and other harmful products, always work in a
well-ventilated area.
11. Wear long pants, long sleeves, and protective footwear.
12. Wear Personal Protective Equipment. Wear ANSI-approved safety goggles. As appropriate, wear a
protective mask and gloves.
13. Maintain labels and nameplates on the product. These may carry important safety information. If
unreadable or missing, visit www.brightfuser.com to contact us.
14. The warnings, precautions, and instructions discussed in this owner manual cannot cover all possible
conditions and situations that may occur. It must be understood by the operator that common sense
and caution are factors that cannot be built into this equipment. Use your own caution.
15. If the equipment is not working, visit www.brightfuser.com to contact us.
TO PREVENT SERIOUS INJURY FROM ACCIDENTAL OPERATION:
Turn the power switch of the equipment
off and unplug the equipment from the electrical outlet before performing any procedure in this section.
TO PREVENT SERIOUS INJURY FROM EQUIPMENT FAILURE:
Do not use damaged equipment. If abnormal
conditions occur, have the problem corrected before further use.
BEFORE EACH USE,
inspect the general condition
of the equipment. Check for:
• Loose parts,
• Misalignment or binding issues,
• Cracked or broken parts,
• Damaged extension cords,
• Damaged electrical wiring, and
• Any other condition that may affect its safe operation.
AFTER EACH USE,
clean parts as indicated.
• Store in an indoor dry area out of the
reach of children and pets.
• Failure to do so may result in
equipment damage and malfunction.
• Wipe external surfaces with a clean,
dry cloth.