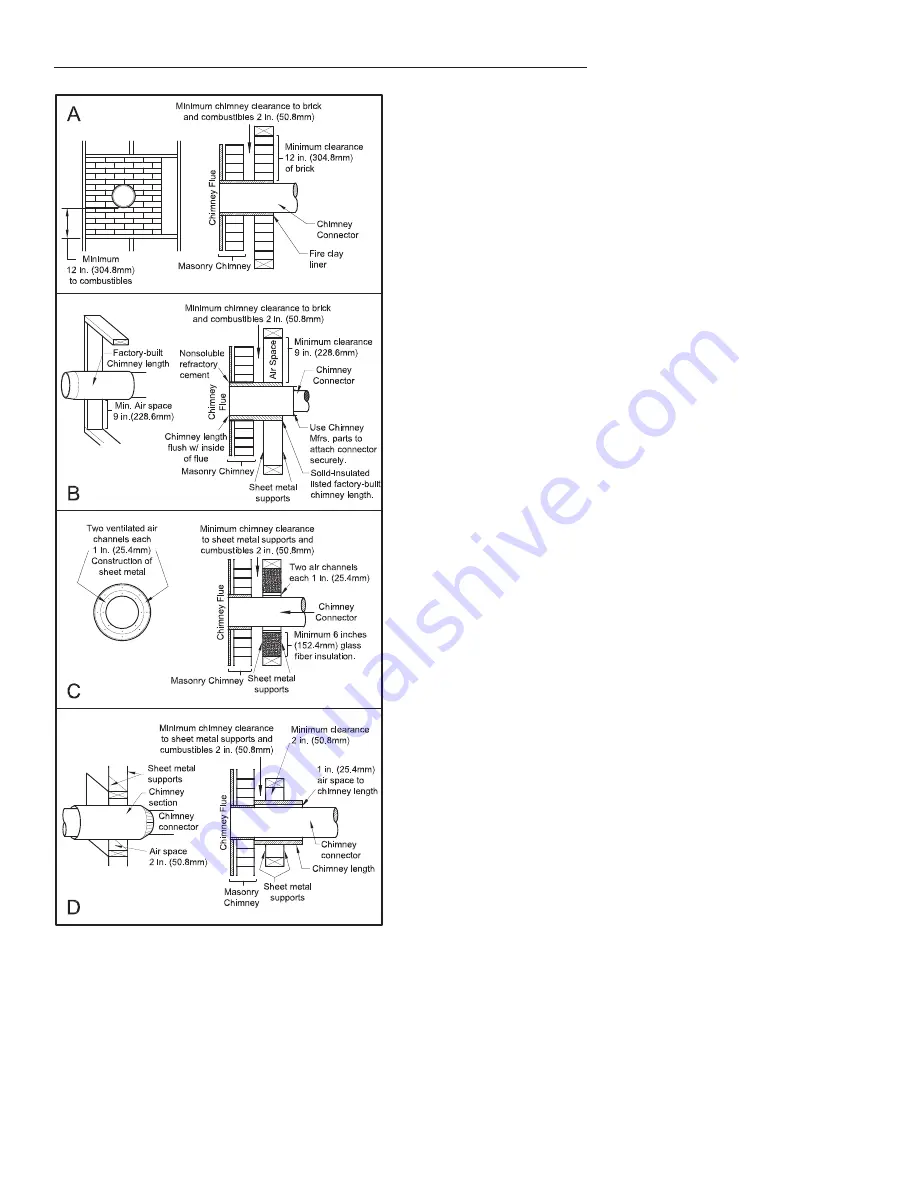
10
COMBUSTIBLE WALL CHIMNEY CONNECTOR PASS-THROUGHS
Method A. 12” (304.8 mm) Clearance to Combustible Wall Member:
Using a minimum thickness 3.5” (89 mm) brick and a 5/8” (15.9 mm)
minimum wall thickness clay liner, construct a wall pass-through. The clay
liner must conform to ASTM C315 (Standard Speci
fi
cation for Clay Fire
Linings) or its equivalent. Keep a minimum of 12” (304.8 mm) of brick
masonry between the clay liner and wall combustibles. The clay liner
shall run from the brick masonry outer surface to the inner surface of the
chimney
fl
ue liner but not past the inner surface. Firmly grout or cement
the clay liner in place to the chimney
fl
ue liner.
Method B. 9” (228.6 mm) Clearance to Combustible Wall Member: Using
a 6” (152.4 mm) inside diameter, listed, factory-built Solid-Pak chimney
section with insulation of 1” (25.4 mm) or more, build a wall pass-through
with a minimum 9” (228.6 mm) air space between the outer wall of the
chimney length and wall combustibles. Use sheet metal supports fastened
securely to wall surfaces on all sides, to maintain the 9” (228.6 mm) air
space. When fastening supports to chimney length, do not penetrate the
chimney liner (the inside wall of the Solid-Pak chimney). The inner end of
the Solid-Pak chimney section shall be
fl
ush with the inside of the masonry
chimney
fl
ue, and sealed with a non-water soluble refractory cement. Use
this cement to also seal to the brick masonry penetration.
Method C. 6” (152.4 mm) Clearance to Combustible Wall Member:
Starting with a minimum 24 gauge (.024” [.61 mm]) 6” (152.4 mm) metal
chimney connector, and a minimum 24 gauge ventilated wall thimble which
has two air channels of 1” (25.4 mm) each, construct a wall pass-through.
There shall be a minimum 6” (152.4) mm separation area containing
fi
berglass insulation, from the outer surface of the wall thimble to wall
combustibles. Support the wall thimble, and cover its opening with a
24-gauge minimum sheet metal support. Maintain the 6” (152.4 mm) space.
There should also be a support sized to
fi
t and hold the metal chimney
connector. See that the supports are fastened securely to wall surfaces on
all sides. Make sure fasteners used to secure the metal chimney connector
do not penetrate chimney
fl
ue liner.
Method D. 2” (50.8 mm) Clearance to Combustible Wall Member: Start
with a solid-pak listed factory built chimney section at least 12” (304 mm)
long, with insulation of 1” (25.4 mm) or more, and an inside diameter of 8”
(2 inches [51 mm] larger than the 6” [152.4 mm] chimney connector). Use
this as a pass-through for a minimum 24-gauge single wall steel chimney
connector. Keep solid-pak section concentric with and spaced 1” (25.4
mm) off the chimney connector by way of sheet metal support plates at
both ends of chimney section. Cover opening with and support chimney
section on both sides with 24 gauge minimum sheet metal supports. See
that the supports are fastened securely to wall surfaces on all sides. Make
sure fasteners used to secure chimney
fl
ue do not penetrate
fl
ue liner.
NOTES:
Connectors to a masonry chimney, excepting method B, shall extend in one continuous section through the wall pass-through
system and the chimney wall, to but not past the inner
fl
ue liner face.
A chimney connector shall not pass through an attic or roof space, closet or similar concealed space, or a
fl
oor, or ceiling.