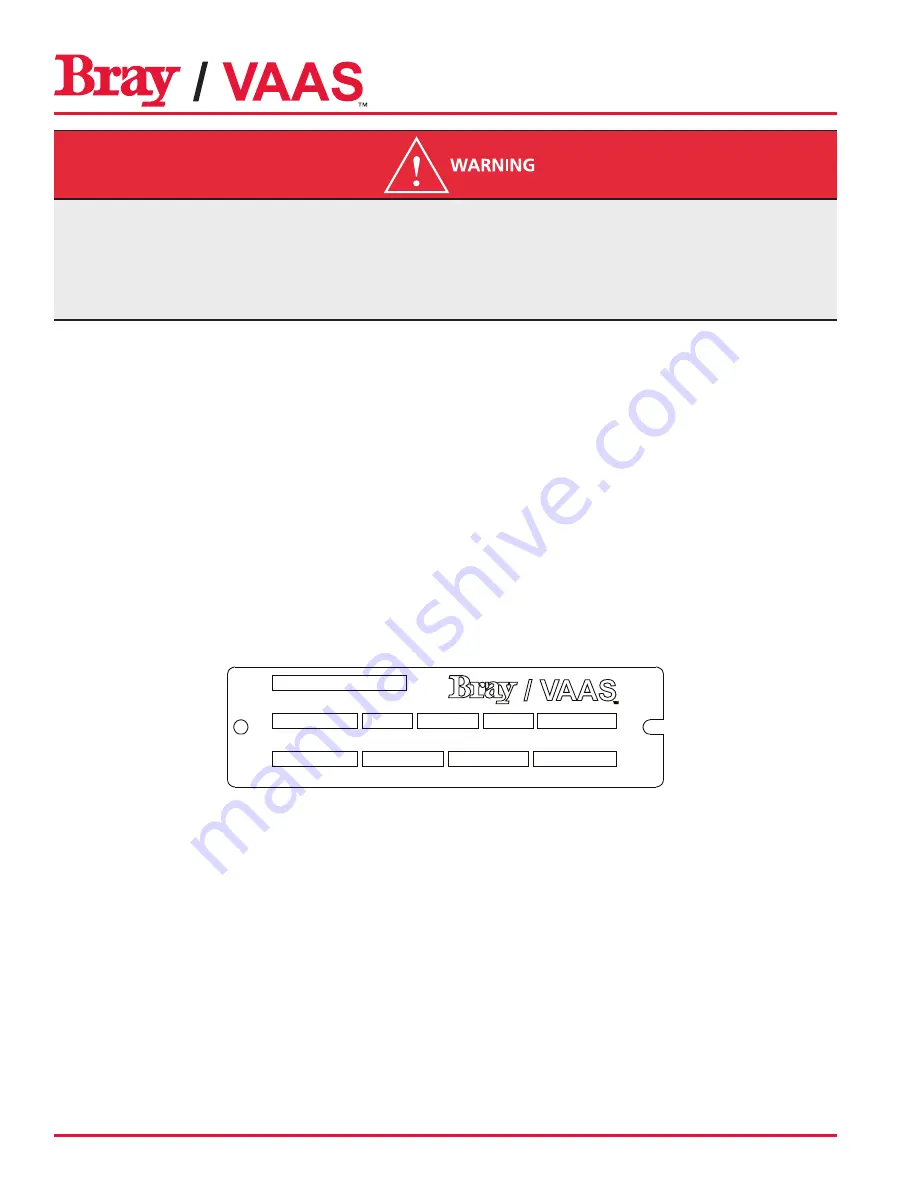
2
O-Ported Series
Operation and Maintenance Manual
The valve must only be installed, commissioned, operated, and repaired by qualified personnel.
The device generates a large mechanical force during normal operation.
All installation, commissioning, operation, and maintenance must be performed under strict observation of all applicable
codes, standards, and safety regulations.
Observe all applicable safety regulations for valves installed in potentially explosive (hazardous) locations.
INTRODUCTION
The Bray/
VAAS Series 770/
780 provides repeatable bidirectional shutoff in a rugged, double-piece cast body
Additional information about Series 770/
780 valves – including application data, engineering specifications, and actuator
selection is available from your Bray/
VAAS distributor or sales representative
UNPACKING
Ensure the box is not damaged externally Remove the valve from the packaging and check for any damage to the valve
and its components during transit
Valve size and brief material specification of body (markings such as “SS” or “DI”) are marked on the valve body Stainless
steel nameplate (below) fixed on to the yoke of valve contains most of the relevant information on the valve including Bray/
VAAS work order number and unique serial number of the valve These details should be quoted for all requirements of
service and spares
SERIAL NUMBER
SIZE
MODEL FLG. DRILL
BODY
GATE
SEAT
PACKING
CWP
MAX TEMP
STORAGE
Wrap the valve with a polyethylene cover Cover the ports for pneumatic actuator/accessories with plastic caps Store
these valves in the same packing indoors and without direct exposure to the environment
INSTALLATION
• Valves can be mounted with flow in both directions
• Install the valve between flanges using fasteners & gaskets
• Bolt holes are always blind tapped and care should be taken not to bottom the bolts while tightening Refer to GA
Drawing/
Technical Bulletin for quantity and size of blind tapped holes on valve chest area If the correct size bolts are
not available, use studs and nuts for chest area bolts to avoid damage of body