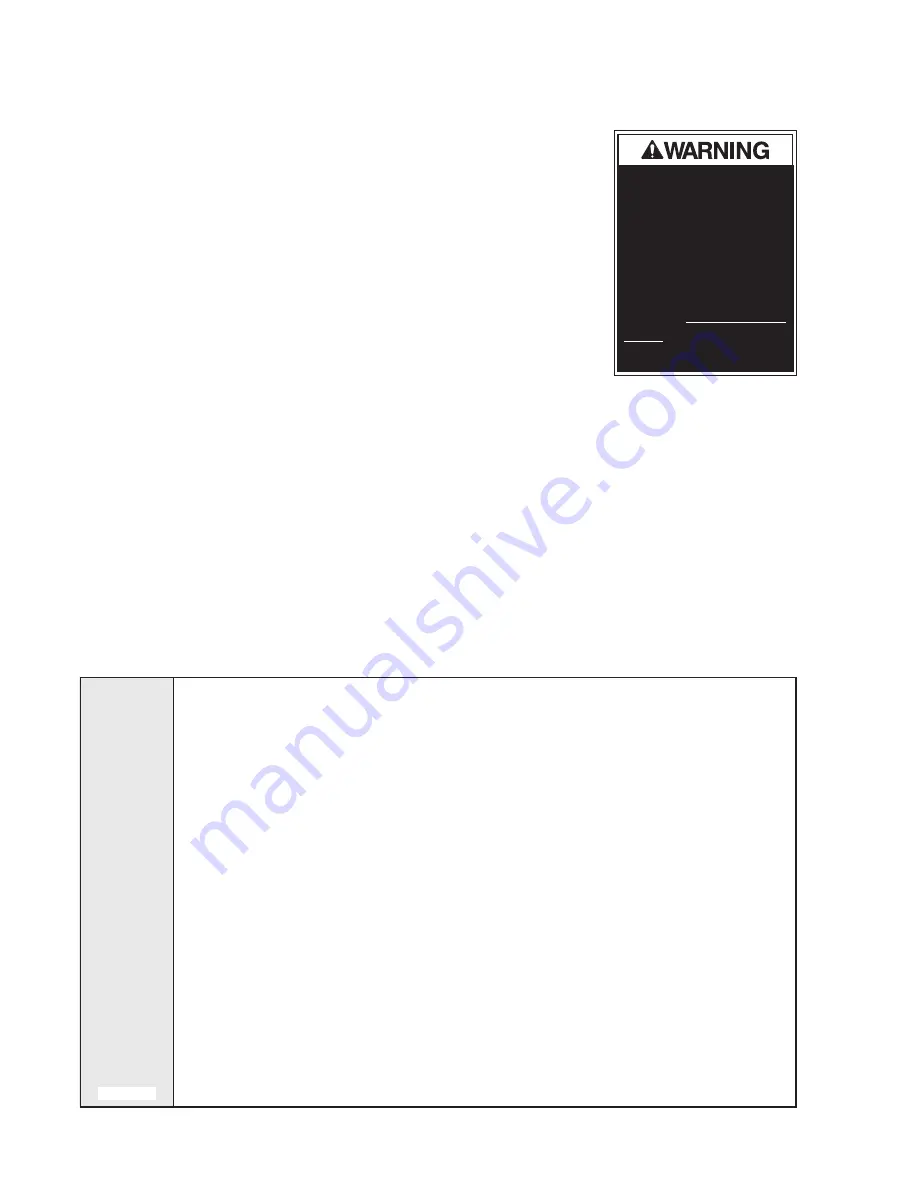
Page 10
Maintenance and Lubrication Schedule
Proper maintenance is necessary to ensure safe,
trouble-free operation. Inspecting the lift for any wear,
damage or other abnormal conditions should be a part
of the transit agency daily service program. Simple
inspections can detect potential problems.
The maintenance and lubrication procedures specified
in this schedule must be performed by a BraunAbil
-
ity authorized service representative at the scheduled
intervals according to the number of cycles.
BraunAbility dual parallel arm lifts are equipped with
hardened pins and self-lubricating bushings to de
-
crease wear, provide smooth operation and extend the
service life of the lift.
When servicing the lift at the recommended inter
-
vals, inspection and lubrication procedures specified
in the previous sections should be repeated. Clean
components and the surrounding area before apply
-
ing lubricants. LPS2 General Purpose Penetrating
Oil is recommended where Light Oil is called out.
Use of improper lubricants can attract dirt or other
contaminants which could result in wear or damage
to the components. Platform components exposed to
contaminants when lowered to the ground may require
extra attention.
Lift components requiring grease are lubricated during
assembly procedures. When these components are
replaced, grease must be applied during installation
procedures. Specified lubricants are available from
BraunAbility (part numbers provided on previous
page).
All listed inspection,
lubrication and main
-
tenance procedures
should be repeated
at 750 cycle intervals
following the scheduled
4500 cycle maintenance
procedures. These
intervals are a general
guideline for scheduling
maintenance procedures
and will vary according
to lift use and conditions.
Lifts exposed to severe
conditions (weather,
environment, contami
-
nation, heavy usage, etc.) may require inspection and
maintenance procedures to be performed more often
than specified.
Cycle Counter:
NL-2 Series lift models are equipped
with a cycle counter located on the top of the pump
module. This cycle counter allows the lift attendant/op
-
erator to easily track the number of cycles during daily
inspections of the lift.
Discontinue lift use immediately if maintenance and
lubrication procedures are not properly performed,
or if there is any sign of wear, damage or improper
operation. Contact your sales representative or call
BraunAbility at 1-800-946-7513. One of our Aftersales
representatives will direct you to a BraunAbility autho
-
rized service technician who will inspect your lift.
Outer barrier pivot points (2)
Outer barrier latch pivot point
Outer barrier latch slot
Outer barrier lever bearings (2)
Lift-Tite
™
latches (tower pivot points - 2)
Lift-Tite
™
latch gas (dampening) spring pivot
points (2 springs - 4 points)
Inspect Lift-Tite
™
latches and gas springs for wear
or damage (bent, deformed or misaligned), positive
securement (lock nuts / external snap rings) and
proper operation.
Inspect outer barrier for proper operation.
Inspect outer barrier latch for proper operation,
positive securement, and detached or missing
spring.
Adjust fold pressure and outer barrier fold pressure.
Apply Light Oil - See Lubrication Diagram.
Apply Light Oil - See Lubrication Diagram.
Apply Light Grease to both sides of slot.
See Lubrication diagram.
Apply Light Oil - See Lubrication Diagram.
Apply Light Oil - See Lubrication Diagram.
Apply Light Oil - See Lubrication Diagram.
Resecure, replace damaged parts or otherwise
correct as needed. Note: Apply Light Grease to
Lift-Tite
™
latch tower pivot point if replacing latch.
Correct or replace damaged parts.
Correct or replace damaged parts and/or relubri
-
cate. See Lubrication Diagram.
See Platfold Fold Pressure Adjustment and Outer
Barrier Fold Pressure Adjustment.
750
Cycles
continued
Maintenance and
lubrication procedures
must be performed
as specified by a
BraunAbility
authorized
service technician.
Failure to do so may
result in serious bodily
injury and/or property
damage.