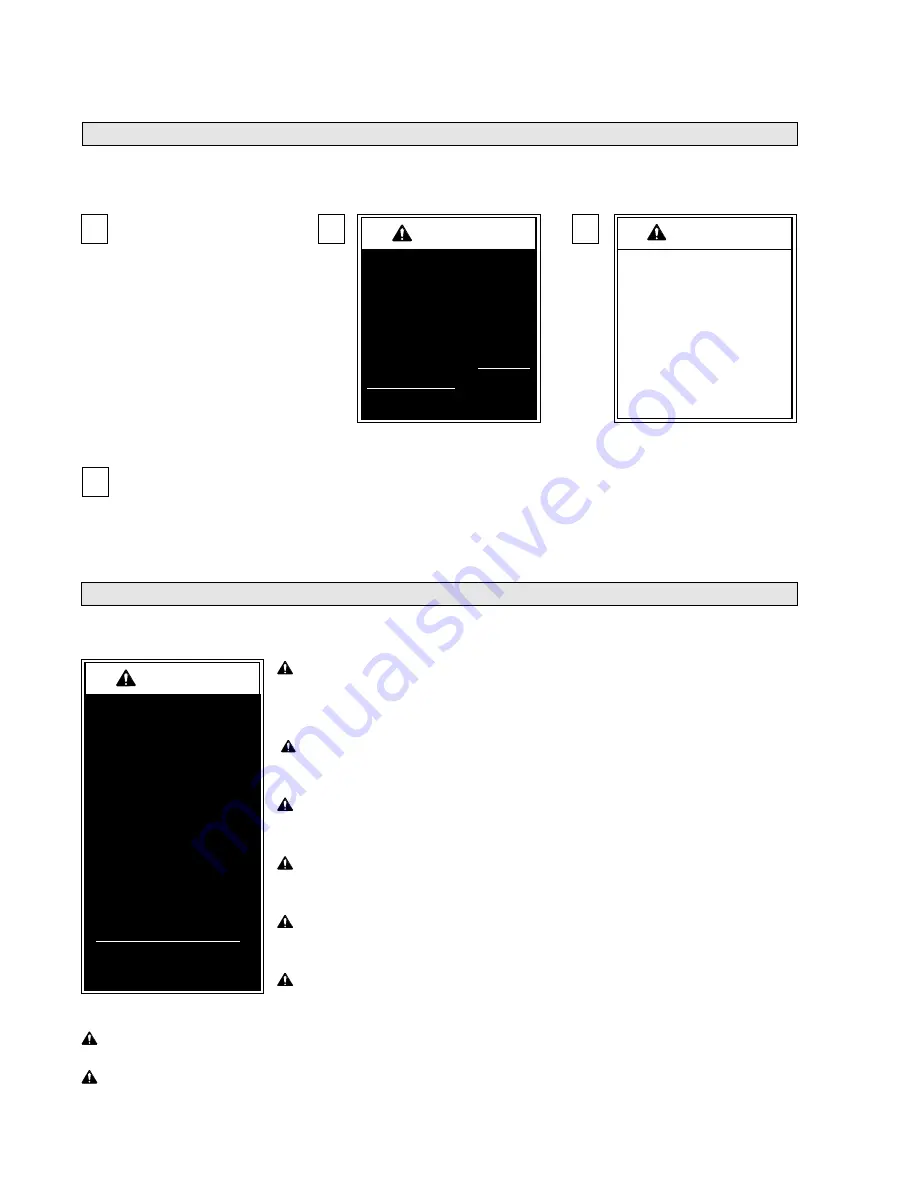
Page 4
WARNING
If installation, mainte-
nance or repair
procedures cannot
be completed exactly
as provided in this
manual or if the
instructions are not
fully understood,
contact The Braun
Corporation immedi-
ately. Failure to do
so may result in
serious bodily injury
and/or property
damage.
WARNING
Read this manual, supplement(s) and lift-posted operating
instructions decals before performing installation, operation
or service procedures.
Minimum clear door opening dimensions specified in Lift
Dimensions per lift model must be provided.
Remove any obstructions within the lift mounting/operating
area prior to beginning installation procedures.
Install lift and power platform to fully folded position before
removing shipping straps.
Do not fold or unfold the platform prior to positive securement
of base plate mounting hardware.
Check for obstructions such as gas lines, wires, exhaust, etc.
before drilling or cutting during installation procedures.
CAUTION
WARNING
WARNING
WARNING
WARNING
WARNING
WARNING
In
s
ta
ll
ati
o
n
/Serv
i
ce S
a
fe
t
y Prec
a
u
ti
o
n
s
Safety Symbols
SAFETY FIRST!
Know That....
C
CAUTION
This symbol indicates
important information
regarding how to
avoid a hazardous
situation that could
result in minor per-
sonal injury or prop-
erty damage.
The information contained
in this manual and supple-
ments (if included), is provided
for your use and safety. Familiar-
ity with proper installation,
operation, maintenance and
service procedures is necessary
to ensure safe, troublefree lift
operation. Safety precautions
are provided to identify potentially
hazardous situations and provide
instruction on how to avoid them.
B
WARNING
This symbol indicates
important safety
information regarding
a potentially hazard-
ous situation that
could result in serious
bodily injury and/or
property damage.
D
Note:
Additional information provided to help clarify or detail a specific subject.
These symbols will appear throughout this manual as well as on the labels posted on your lift.
Recognize
the seriousness of this information.
A
Installation/Service Safety Precautions
Route all cables clear of exhaust system, other hot areas, moving parts, wet areas, etc.
Risk of electrical shock or fire! Use extra care when making electrical connections.
Connect and secure as outlined in Installation Instructions and Wiring Diagrams.